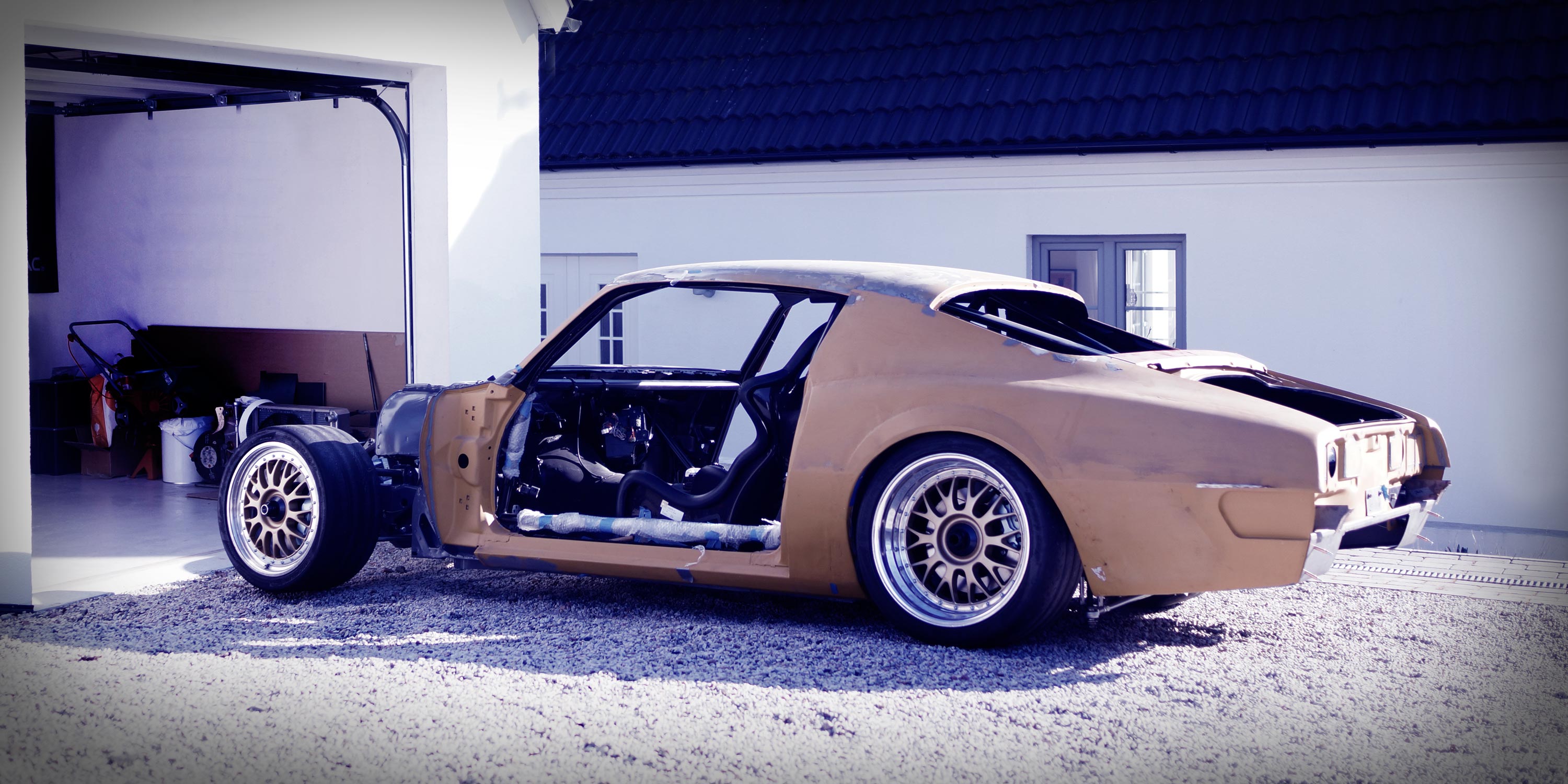
Etikett: Laser Cut
Laser cut sheet metal
Tillbehör motor
Efter att hjulupphängningarna var avklarade och bilen (teoretiskt) hade kunnat komma ner från pallbockarna, är det ”bara” motorn kvar att färdigställa. Bara.
Senast gjordes insuget klart och monterades på motorn. Spacern mellan insug och spjällhus lär inte kunna användas, så den skippades efter denna bilden togs. Att bygga luftfilterlåda kommer bli ett projekt i sig, men tills vidare får det lösas temporärt.
Efter att insuget var färdigt, landade även andra elförzinkade motordetaljer lite lägligt i garaget.
Ovan; Elförzinkat i all ära, men att föra in ytterligare en kulör på motorn kändes som att det var risk att intrycket skulle bli för rörigt. Med andra ord lackades delarna svarta. Svart, gjutjärnsgrått och silver i form av aluminium eller rostfritt räcker gott och väl i form av färgnyanser på motorn. Elförzinkningen gör fortfarande nytta eftersom 1k-lacken inte är mycket att räkna med när det gäller rostskydd. I framtiden hägrar såklart CNC-frästa detaljer istället, när man kommer så långt på prioritetslistan. Högra bilden visar även nyeloxerade fästen för torrsumpspump, samt svarteloxerad remskiva.
Nedan; Fäste för generator och AC-kompressor monterade. Guleloxerade biten (som missades vid målningen!) i bakgrunden sitter fäst i blocket. Lite röriga bilder att kolla på, men fästena sitter monterade med samma skruvar som håller bröstkåpan på motorn.
Ovan; Andra vinklar på samma detaljer. Det är stabilt, som en viss tandläkare hade sagt.
Nedan; kompressorn monterad och därefter kom även generatorn på plats. Till och med en multiribrem har hittat dit. Längden på remmen bestämdes först, därefter placerades komponenterna på motorn i datorn och sen ritades plåtarna. Med andra ord var det bara att åka och handla rätt remlängd och hänga på den.
Återmontering; Framvagn
Återmonteringen fortsätter – lite plåt trillade in för någon vecka sedan vilket gjorde att de nya länkarmarna kunde byggas klart. Snart borde bilen åter igen vara ihopmonterad och det blir mindre och mindre kvar inför första SFRO.
Ovan; Äkta pussel. Vinkelslipen kom inte fram en enda gång! Upp i fixturen med dem och börja nästa ihop delarna. Som vanligt är det ont om bilder när man befinner sig i stridens hetta, och istället får man hålla till godo med TV-kocksvarianten… ”Jag har förberett en färdig länkarm här på bilden nedan”.
Nedan; …men en bild hittades i kameran i alla fall, precis innan TIG:en sparkades igång.
Ovan; Inte VM i TIG-svetsning direkt, men det börjar ta sig (förutom vänster i bilden – där är det kräkfult. Fattar inte vad jag sysslade med…)
Nedan; Och monterat, men utan spindel… och i närbild…
Ovan; Allt på plats och inshimsat för första gången. Extremt tight – inte mycket flex i upphängningarna, trots polyurethanbussningar på ett par ställen. Känns bra. Höger bild; Pushrodsen åkte såklart med på helsvetsning också när länkarmarna fixades. Ett par M16-mutter svarvades ur och pressades på efter helsvetsningen, samt låstes med några svetsloppor för att kunna justera dem.
Tändspolar
Eftersom det blir nytt styrsystem/ECU (DTA S80 PRO) fick även nya tändspolar lokaliseras. Valet föll på GMs LSx-spolar. Tämligen poppis, robusta och asbilliga. När det handlas specialprylar i det här projektet köps det alltid hem lite extra, tex dubbla uppsättningar bromsskivor för att kunna ha ett par på hyllan. Typ 10 uppsättningar belägg, nio tändspolar, tre torrsumpsremmar, ett antal topplockspackningar osv. Bra att ha saker på hyllan om man skulle köra sönder.
Ovan; GMs LSx-spolar. Har bråkat en hel del med att försöka hitta ett vettigt ställe att montera dem på. Flertalet ställen har testats, och för närvarande leder placeringen ovanpå ventilkåporna. Inte snyggaste installationen, men alla ingenjörer vet att funktion går före form…
Lite laserskuren aluminium trillade hem för att underlätta montering.
Nedan; Monterar spolar i godan ro när man plötsligt inser att potatisälskande Bob på monteringslinan i Idaho, eller var den nu kan tänkas ligga, inte har haft en bra dag när han byggde mina spolar. Tittar man på högra spolen som är monterad mot aluplåten, inser man att fästena inte sitter i linje med varandra. Skiten har hamnat snett vid montering och därefter gjutits in i epoxi. Inte mycket att göra åt – inget man kan plocka isär och korrigera direkt. Tur att man köpte nio med andra ord…
Nedan; Jaha, så här blev det. Man äger alltså en Ontiac numera. Det var ju kanske lite snopet, även om en bokstav mindre inte är hela världen. Eller ärlden…
Hmmm, år og uga å en ite ill…
Växellådsbalk
Original växellådsbalk löper mellan subframebenen, dvs den är dryga metern bred och alltid ett helvete att få ner eftersom den sitter ovanpå rambenen och därmed måste snedställas. Men det går inte eftersom det sitter en växellåda i vägen…
Tidigt i projektet konstaterades det att det löper en tvärgående balk i karossen som kunde agera del av en ny växellådsbalk. Genom att nyttja denna, kunde den nya växellådsbalken göras kortare. Ca 25cm istället för 1,4 meter(!), vilket inte bara sparar vikt, utan även värdefullt utrymme för avgassystemet.
En liten fin laserskuren byggsats, levererad av hovleverantören (stort tack!), som kompletterades med två rörstumpar resulterade i en balk som väger drygt 2kg (original landade runt 8kg).
Ovan; Inspiration om att man kunde göra så här kom från någon bild från Speedhunters på en bil jag inte kommer ihåg vilken den var. Med motorn på plats byggdes en enkel mockup som sen mättes upp i CADen för att kunna skära till något snyggare.
Nedan; Balken i karossen hamnar på perfekt avstånd för att agera växellådsbalk. Hål kapades för att hysa infästningar, som självklart svetsades dit monterade i en fixtur för att det skulle hamna 100% rätt.
Ovan; Färdigsvetsad balk. Liten avvikelse fick göras för att optimera utrymmet för avgassystemet – Hela motorpaketet är flyttat ca 30mm åt passagerarsidan vilket plötsligt gjorde att förarsidan hade hur gott om plats som helst för avgassystem, medans passagerarsidan inte hade något. Det löstes genom att helt enkelt fasa den (det är alltså gjort på bilden…).
Nedan; Monterat och klart. 8.8-skruvarna skall bytas mot 12.9 med tiden. De fästelement som finns att köpa i järnhandeln är rätt tråkiga så planen är att köpa ett par kilon från lämpliga donatorbilar på närmaste bilskrot.
Torrsumpstråg ll
För att fånga så mycket olja som möjligt som yr runt i vevhuset, bör utrymmet kring veven vara så litet som möjligt. På förarsidan av motorn är detta redan väldigt tight eftersom tråget är format utefter vevens projicerade perimeter. På passagerarsidan öppnar det dock upp (eftersom oljan skall rinna hitåt), och därmed behövs någon som fångar oljan som slungas från vevaxeln. Detta löstes genom en skrapa som ligger några millimeter från vevaxeln och tar mycket av den oljan som slungas tillbaka upp i vevhuset. För att ta resten, och snabbt få ner det på botten av tråget, sattes ett nät i samma radie som höljet på förarsidan. Nät är nog fel benämning, hålad plåt passar bättre.
Ovan: Yttre konturen av oljetråget kan anas på bilden. För att fånga så mycket olja som möjligt från veven och vevhuset sattes en perforerad (nedan) plåt på evakueringssidan av tråget (den skall svetsas lite mer, men från insidan istället för utsidan).
Ovan och nedan; Säg en konstruktion som inte innehåller kompromisser… Även oljetråg har sådana, i detta fall fick området kring kamdrivningen pysslas om lite extra. 9 kantningar samt ett tak svetsades samman till en enda detalj innan den svetsades mot tråget (för att minska risken att tråget slår sig).
Ovan; Genombränningen kan man inte klaga på. Bilden tagen från insidan…
Evakuering av oljan gjordes i botten av tråget. Istället för att tillverka en lång ränna, gjordes tre separata utsug. Egentligen skulle man haft en 5-stegspump (1 tryck, 4 sug) som de stora grabbarna i nascar osv har. Då hade man kunnat suga från varje kammare. Eftersom tråget är i stål, är det dock lätt att uppgradera om en fetare pump skulle införskaffas i framtiden.
Istället suger mittenutsuget 50/50 från de två mittersta kamrarna. De yttre suger ca 25/75 inner-/ytterkamrar. Den totala utsugsarean från varje kammare är alltså lika stor.
Ovan; För att få en snäll båge på rören och uppnå tillräcklig längd för att ens kunna hantera ledningarna lades utloppen på motsatt sida från pumpen. Alternativet hade varit att vända dem 180º, men då hade ledningarna blivit mellan 3 och 12cm. Lite pilligt… AN10-storlek valdes på dem. Normalt är AN12, men det blir ganska klumpligt och 3st AN10 utlopp suger lätt ut mer olja än 1st AN12 klarar att pumpa in…
Nedan; För att ändå maximera utsugsvolymen användes rör istället för slang. Rören är tunnväggigare än slangarna, vilket gör att man klarar sig med en AN10-koppling (lite specialbyggd…) och ändå nästan kan ha samma volym som AN12. Endast sista centimetrarna mellan pump och rör blir slang för att kunna ta upp visst flex. Lite luddigt förklarat kanske, men jag vet vad jag gör… 🙂
Högra bilden: Nä, men titta. Vilken ”tur” att utsugen passar så bra mellan rambalkarna att motorn kan sänkas ner (ytterligare 60mm – redan 80mm sänkt) utan att ta i ramen. Med tanke på att placeringen av utsugen i tråget är låst, är det nästan som att någon har tänkt på detta när ramen ritades… Suget efter en växellåda med bättre markfrigång blir bara större och större…
Ovan och nedan; Bygge av utsug. Det är inte många droppar olja som stannar kvar i tråget – utsugen hamnar bara någon millimeter från botten av tråget.
Vanliga JIC10/AN10-kopplingar från en hydraulfirma har svarvats om. Nedre högra bilden visar hålet som blivit koniskt uppsvarvat. 10º resuterade i rätt rejäl ökning i diameter.
Torrsumpstråg
Motorn har torrsump, dvs det sitter en separat tank bakom passagerarsidans framhjul.
Eftersom utbudet av färdiga torrsumpstråg för Pontiacmotorer är högst begränsat (obefintligt), byggdes ett eget för många år sedan. Kompromisserna som gjordes då, pga en ganska klumpig framvagnsbalk, gjorde att evakueringen av oljan kunde förbättras. Det mesta av oljan har sugits ut ur ett enda steg (det på botten av tråget). Tråget har på något sätt inte varit dåligt, utan gjort sitt jobb bra. Men det går såklart inte att hålla förbättringsfingrarna borta…
Det är ju nämligen synd att inte förbättra en sådan detalj innan motorn monteras med tanke på svåråtkomligheten när väl motorn sitter på plats. Planen från början var att bygga ett nytt tråg i aluminium för att spara lite vikt, få lite gratis kylning och helt enkelt för att aluprylar är najs. Men det skiter sig eftersom en AC/DC-TIG fortfarande lyser med sin frånvaro i Pontiacens nittonkvadratsmetergarage.
Ovan; Befintligt tråg med dess kompromisser. På bilden syns de urkapningar som fick göras för att förra framvagnsbalken skulle få plats. Den nya balken är betydligt rymligare, så nu skall det gå lättare att konstruera ett nytt tråg.
Nedan; Tråget från insidan. Som synes, suger bara en utgång direkt från botten (syns lite dåligt i den svarta oljan, men uppe till höger i den vänstra bilden). Den andra tvingas suga med rör ovanfrån – och tänker man lite, inser man vad som händer när man får in luft i röret. Som sagt, tråget har fungerat även så här, men förbättringspotential finns.
Istället fick det bli ståltråg i tunnplåt, precis som det gamla.
Några förändringar skall dock göras:
- Torrsumpen har tre sugsteg, och alla dessa skall suga från tråget, istället för som det är nu där en suger från tråget, en låtsas suga från tråget, och den andra mest suger luft uppe i höjd med kamaxeln.
- Vidare skall kammarna separeras likt bilden nedan. Detta görs dels för att inte oljan inte skall röra sig för mycket innan den kommer fram till utsuget, men även för att förbättra aerodynamiken kring vevaxeln. Lite akademisk överkurs på det sistnämnda, men det är lika bra att göra rätt enligt teorierna när man ändå håller på.
- Även en skrapa (höger bild) skall integreras i tråget så att inte inödig olja slungas upp tillbaka i vevhuset, utan transporteras ut till torrsumpstanken fortast möjligt.
- Totalhöjden på tråget kan också optimeras något. Där finns gissningsvis 15mm onödig luft. Lågt tråg innebär att motorn kan sänkas ännu närmare marken, även om det för stunden är växellådan som är begränsande faktor eftersom motorn redan sänkts 80mm.
Ovan; Torrsumpstråg från någon LSx-racemotor med separerade kamrar. Skrapan på bilden till höger är faktiskt från en Pontiac-motor. Det finns sådana att köpa, men jag ska såklart krångla och satsa på en integrerad i tråget istället. I slutändan är en integrerad lösning betydligt prydligare än lösa detaljer som klämmas in mellan tråg och block.
Det största, och tråkigaste, arbetet är inte helt oväntat att försöka mäta upp dagens hålbild på blocket. Inte helt enkelt, men efter otaligt antal pappersmallar fanns ett utkast framme. Skärfilerna skickades till min hjälpande hand, Henrik, som levererade på rekordtid. Därefter punktades allt samman.
Ovan; det blev nog ett tiotal versioner innan alla hålen var rätt på plats. Nagelsax och vanlig sax för att klippa ut det. Ganska tidsödande arbete. Resultatet (till höger) blev dock riktigt bra.
Nedan; klipp-klipp-klipp… ut och prova på motorn. Nej, ett hål skall flyttas ungefär 1mm till höger, ett annat 1mm upp och vänster, tredje flyttas tillbaka 1mm osv. Ctrl P och klipp-klipp-klipp och börja om igen… Tålamodsprövande.
Ovan; Flänsarna runt om är 3mm. Utsidan av tråget byggs i 1,25mm och väggarna är 2,5mm. Notera att väggarna skiljer sig åt beroende på överfallets utformning. Den effektiva delen av skrapan, som riskerar att komma i kontakt med vevaxeln, frästes ner från 3mm till 1,1mm istället. Om någonting i motorn skulle gå sönder, kommer skrapan slås sönder istället för att ha sönder resten av motorn.
Styrarmar
Det var meningen att styrarmarna skulle CNC-fräsas. Egentligen inte ett behov, men för att få lite snygg rund radie på ytterkanten så hade det varit smidigt. Tyvärr visade det sig bli alldeles för dyrt att leja bort fräsningen, så istället kläcktes den eminenta idén att laserskära ytterprofilen och därefter bara borra hålen i fräsen. Det visade sig vara en ganska bra idé – ofta är det planing och fräsning av konturer som tar längst tid i en manuell fräs. Att ”bara” borra lite hål med rätta kordinater går ganska fort.
Ovan: Godis. Ny leverans med delar från… Lasermannen! Nya vipparmar, förstärkningar till övre länkarmar, nya infästningar till coilovers i subframen med ett hål till på höjden och sist men inte minst råämnen till styrarmarna (till höger).
Nedan; Lite planing och några hål senare så gick de från stålbitar till styrarmar.
Nedan; Färdiga. 1:10-kona för volvo styrled. Tre hål för att enkelt kunna exprimentera med styrutslag och antal rattvarv.
Ovan och nedan; Slutgiltigt resultat blev bra! Monterad på spindeln, passar som handen i handsken. Styrleden tar inte emot bromsskivan när den sitter i innersta hålet, och det tiden kommer det komma en värmeplåt mellan spindel och skiva som skyddar gummimembranet på leden. Styrväxeln har kortats ca 20cm vilket gjorde att stagen till spindlarna behövde förlängas. Därför har de kompletterats med en skarvmutter (M14 skarvmutter fanns inte som standard, så det blev att svarva en egen…) och en förlängare.
Pga styrväxelns placering blir Ackermann (vinkelskillnad mellan ytter- och innerhjul då dessa har olika svängradie vid stora utslag) ganska lidande. Den blir något bättre när spindelleden flyttas ut till yttersta läget, men är fortfarande inte imponerande. SFRO brukar tycka Ackermann är ganska viktigt, men i mina ögon är det något man behöver när man ska navigera på parkeringsplatser. Enda gången man har väldigt stora rattutslag är i låg fart, övrig tid använder man sällan mycket mer än 10-15° utslag. Får se vad SFRO säger den dagen det blir dags.
Det går att få mer Ackermann genom att tex flytta styrväxeln bakåt. Problemet är ju bara att där finns infästningar för länkarmar. Man kan tänka sig att vända på infästningen på spindeln och lägga styrväxeln ovanför, men där finns ett oljetråg… Kompromisser kompromisser… 😉
Nedre länkarmar
Det börjar som ett litet plockepinn. Alla standarddetaljer – länkhuvuden, spindelleder, bussningar, skruvar etc – köps hem. Därefter svarvas hylsor till bussningar, rör kapas i rätta vinklar och gängade hylsor till länkhuvuden svarvas. Plåt skärs och kantas.
Därefter är det das att tillverka en stabil fixtur – länkarmar är, och ska vara, förbrukningsvara. På så sätt slipper man förhoppningsvis reparera saker på ramen vid en eventuell smäll. I detta fall fungerar fixturen både till övre och undre länkarmar.
Notera att rören är plattovala, 40x20mm. I ärlighetens namn är det för att det ser coolt ut. Det här är en karossbil, så någon aerodynamisk fördel ger de knappast. Dock borde de vara något styvare än 30mm runda rör vid retardation. Eftersom pushrod-infästningen sitter långt ut på armen, påverkas inte själva armen nämnvärt av fjädrandet. Planen var från början att ha pushroden monterad direkt i spindeln, något man ofta ser på formelbilar. Fördelar är bl.a. att det avlastar spindelleder, länkarmar kan göras lättare mm. Tyvärr är det svårt på gatbilar pga det större styrutslaget (+-35° jämfört med gissningsvis +-15)
Motorfästen del 2
När det gäller val av motorfästen, blev det helt enkelt vanliga bussningar. De har, till skillnad från många riktiga motorfästen, fördelen att vid tex brand i motorrummet gör det inget om plasten smälter. Eftersom det sitter genomgående skruv i hylsan. Motorpaketet kan skramla bäst det vill vid en avåkning/olycka, men det kommer aldrig släppa från infästningarna. I teorin i alla fall…
Ovan; Powerflexbussningar används som motorfästen. Henrik skar till några plåtar till mig och hylsan svarvades själv. Generellt kan det vara svårt att få till hundradelarna på invändiga mått, men i detta fall förenklades det genom att det ”råkade” finnas en 28mm brotsch liggandes. Den rostfria axeln som följde med bussningen kortades ca 10mm. Skruvhålet är bara 8mm, men skall tas upp för att passa M12 var det tänkt. Plåtarna på bilden är bara punktade samman. De ska såklart helsvetsas senare. Bussningarna är köpta på Demon Tweeks, artikelnummer; PFXPF99-102
Nedan; Andra röret mellan ram och drivlina sitter på plats. Stabilt, hade Dr Alban beskrivit det som.
Ovan; Och så här blir det. Tack vare att motorn sitter bakom framvagnsbalken, blir det ett helt annat utrymme för grenrören. Även dessa kommer behöva byggas eftersom motorn är sänkt… Suck. Det finns inga genvägar till den perfekta bilen!
Styrspindlar
Det blev ett tiotal varianter av spindlar innan jag till slut bestämde mig. Det som skapade problemen var den radiella infästningen av bromsoken. Kan ju enkelt lösas med en adapter, men jag ville konstruera smart och minsann inte ha någon adapter mellan spindel och bromsok. Till slut blev det adapter ändå…
Ovan: en rad olika material och godstjocklekar användes. Sannolikt något överdimensionerade delar, men hellre det än att det går sönder. Styrspindlar är trots allt en ganska komplex detalj som tar laster i många riktningar. Trots överdimensioneringen är vikten lägre än för motsvarande vattenskuren spindel i aluminium…
Ovan; Modularitet och byggbarhet har blivit lite av projektets ledord. För att inte behöva kapa och svetsa för mycket i karossen i framtiden, har tex extra fästen placerats på strategiska platser (i bakvagnen tex om man i framtiden vill uppgradera…). På samma sätt består övre infästningen i spindeln av två alubitar (och genomgående skruvar, men de var visst slut i CADen så brickorna får vara ensamma tills vidare) som enkelt kan shimsas för att få olika SAI/KPI-vinkel
Ovan; En variant av alla spindlar som ritades. Lite dålig bild egentligen, men den består av vattenskuren 40mm aluminiumplatta med utskuren mitt för att tillåta kylluft (under scoopet) passera ut till bromsskivan. Det blev dock stål i slutet pga två anledningar; Alut visade sig behöva vara upp emot 60mm för att infästningarna för bromsarna skulle få plats. För 60mm aluminium gick det inte att hitta någon som kunde vattenskära för under 6000:- för 2st spindlar. Det skall jämföras med ca 350:- som stålspindlarna ovan kostade…
Nedan; Den skarpsynte noterar även att bromsoken lutar något nedåt. Kan tyckas vara ett löjligt argument – men allt görs för att få en låg tyngdpunkt. Nedanstående modifiering resulterade i ca 3% lägre tyngtpunkt på spindelpaketet. Många bäckar små…
En pall kommer lastad….
…Med vad då?
Ovan: Med bakaxelplåt såklart!
Det finns vänliga människor, och sen finns det ännu vänligare människor. Mats på Habo Rostfria och Henrik på en annan firma (hans chef kanske läser här… Haha!) har varit mycket hjälpsamma och försett mig med plåt baserat på mina CADunderlag. Jag slipper med andra ord att stå med vinkelslipen och karva ut detaljerna. Istället kan jag genast börja pussla ihop delarna med varandra (den skarpsynte ser att jag redan tjuvstartat när denna bilden togs).
Nedan: Här är ändarna på dedionen. Inte så mycket att säga om det hela mer än att det är kul att leka med TIG:en när det är så bra passform på delarna. CADbilderna längst nere är bara som referens. Prylarna ser som sagt ut lite mer kompletta i verkligheten eftersom jag inte orkade rita de enklaste plåtarna i CADen.
Det mesta arbetet sker just nu framför datorn och svarven/fräsen. Karossen får vänta på bättre tider, men lite småsaker som är relaterade till bakvagnen sker dock fortfarande.
Nedan: Diffen monterad i karossen för att prova ut lite olika upphängningar av bakre infästningspunkten. Som synes är det ganska ont om plats. Desto bättre att börja med pappmallar innan detaljerna tillverkas…