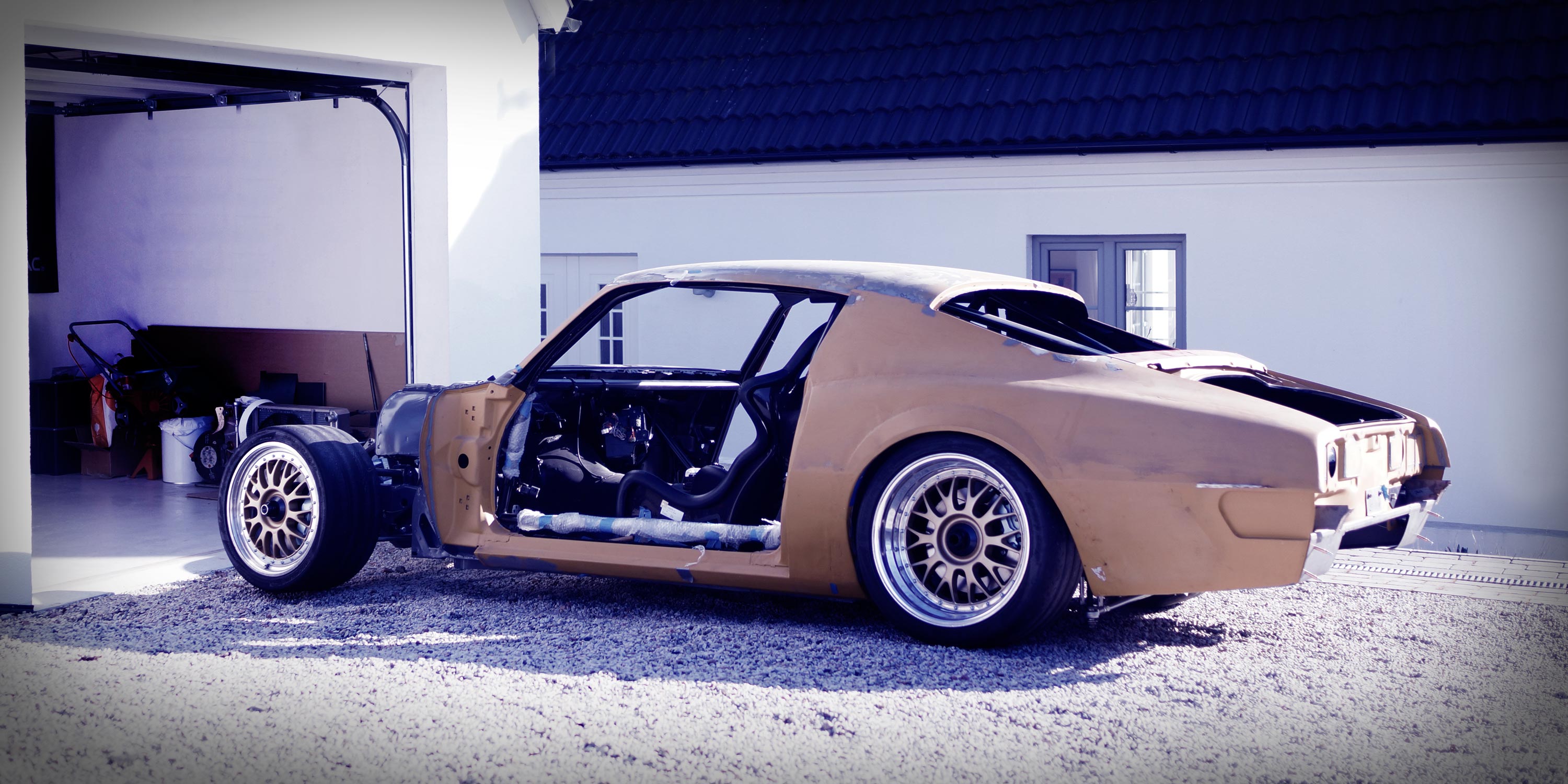
Etikett: Better Than New
Parts that has been refurbished and/or improved somehow that they are better than when they left the manufacturor
Termostathus
Kylaren har AN20-anslutning och en sådan slang lokaliserades på eBay efter lite letande. Lättviktskoppling pressad direkt på slangen och en skadad wigginsanslutning i andra änden. Kevlar-slang, bara för att… Väger absolut ingenting. Termostathuset visade sig dock ha fel anslutning för slangen (kanske inte så konstigt), så det fick bli lite justering.
Ovan; Termostathuset innan fräsen började tugga i det.
Nedan; Anslutningen kapades bort och därefter frästes en recess för att stumpen från wigginsanslutningen skulle kunna återanvändas som slangstos. Den skarpsynte ser att en recess även gjorts för svetsfogen.
Nedan; Färdigsvetsad och färdig. Helt färdigställd och fin… Färdig. …men ser den inte lite tung ut?
Orörd vägde den in på 450 gram. Halvt kilo termostathus… Det funkar ju inte.
Nedan; Jo men visst var den lite tung. Upp i fräsen och börja karva bort onödigt material. Grovfräsning med vanlig pinne och därefter finfräsning med fullradie. Lite nervöst på några ställen eftersom de gängade hålen verkade handborrade och knappast satt på några jämna avstånd. Men fräsen lät bli att slakta dem, trots en omättlig hunger på aluminium.
Nedan; Färdigt resultat, från 552 gram(!!!) till 185 gram. O-ringsanslutningar istället för packningar, liten styrning i nedankant för att alltid hamna rätt mot termostaten (eftersom jänkehålhålen gör att man kan placeras huset precis hur som helst) nya pluggar och nytt termostatlock.
Nedan; Det går ju inte att återanvända samma lock som tidigare, nu när termostathuset blivit så fint. Sagt och gjort beställdes nytt termostatlock från staterna, anslutning från Kina och en Sverigetillverkad aluminiumstump. Notera att brickorna är försänkta… Nördigt.
Ja, det är försänkta ytor för brickorna så att dessa hamnar flush med resten av huset.
”Renoverar” insuget
I samband med att insuget skulle återmonteras konstaterades det att det genom året hade blivit ganska dassigt. Med andra ord fick det sig en översyn innan det var dags att montera det på motorn.
Ovan; På bild såg det helt OK ut, men i verkligheten var insuget ganska sunkigt.
Nedan; Försök att eloxera insuget misslyckades. Hade det bara varit samma material i alla detaljerna så hade det sett helt OK ut. Nu visade det ju sig vara flera olika material och igensvetsade pluggar etc. Eftersom det kändes lite fattigt att måla det i ”aluminiumlook” togs omvägen via krymplack istället.
Utan provbitar och tidigare erfarenheter gick sprayburken direkt på insuget. Tråkigt om experimentet skulle misslyckas, men ingen minns en fegis.
Fördelen med att eloxera det först är i alla fall att insidan av insuget bliv kliniskt ren, samt att färgen biter bra i eloxeringen.
Nedan; Därefter IR-torkning för att få upp värme i färgen. Ca 30 nervösa minutrar passerade innan det på bara några minuter började krympa lite varstans på insuget. Fem minuter senare hade det krympt överallt där värmen kom åt.
Ovan; Färdigt resultat. Blev faktiskt riktigt snyggt. I framtiden ingår att skaffa lite mer klassiska ventilkåpor och då kommer dessa också lackas med samma typ av krymplack.
Ovan; En del kringkomponenter som såg lite tråkiga ut snyggades till. Fuelrailen var oxiderad, repig och smutsig. Och tung. Eftersom kanterna var handsågade, frästes dessa vinkelräta. Därefter fastades ytan av i svarven och centrumdelen som skymtar på högra bilden svarvades av.
Nedan; Eftersom Kauffman-topparna saknar originalstyrningarna för insuget, kasar packningen runt någon millimeter hit och dit. För att vara säker på att den centrerar i kanalen gjordes styrningar till insuget istället som packningen kunde pressas på. De är bara 0.5mm höga medans packningen är 1.5mm, så det bör inte vara risk att dra dem i botten.
Nedan; Rena detaljer återmonteras.
Nedan; Bränsletrycksregulatorn såg också lite tråkig ut. Skavd polering med oxid på många ställen. Eftersom det inte finns så mycket polerad aluminium på andra ställen så plockades den ner och eloxerades i naturfinish. Skruvarna som var svartoxiderade, och hade börjat rosta lite, elförzinkades och AN-kopplingarna fick koniska hål för att… Ja, det var mest av principiella skäl – diameterövergångar skall ske så snällt som möjligt.
Nedan; Färdigt insug, redo att monteras så fort nya längre skruvar (eftersom de rostfria skruvarna inkluderade i motorskruvkitet var i kortaste laget) har anlänt från ett stort land i öst.
Spakställ
I samband med elsystemet byggs, passas det även på att åtgärdas en rad andra elrelaterade saker. Växelspaksknoppen i klassisk vit design med T56-växelmönster har knapp för lämplig funktion. Kabeln kan såklart inte löpa på utsidan som någon tyckt den skall göra, utan istället måste den ju löpa inuti spaken.
Ovan; Långhålsborra 250mm i en kromad stång… Kinesstål visserligen, men det var ganska hårt ändå. Sladden leds uti nederkant och buntband låser den. Skavskydd i form av okrympt krympslang. När man ser bilden slås man av att det saknas något… Dammtätning för själva leden. Tillverkaren har struntat i det – man får vad man betalar för…
Nedan; Upp med spakstället i fräsen med andra ord. Swish swish så finns där ett litet urtag och med topplocket monterat så blir det en utmärkt fläns för att hålla en damask.
Nedan; På med lite sprayfärg på huset igen, korta ställskruvarna och lås dessa med körnslag efter att rätt slag ställts in och ett varv eltejp utanpå för att hindra eventuell smuts i gängorna för ställskruvarna. Därefter på med originaldamasken till GMs vanliga spakställ som plötsligt passar som handen i handsken.
Nedan; Montera det på växellådan och som pricken över i:et användes en damask till kardantunneln från en Firebird -96. Riktigt bra passform mot kardantunneln. Man kan nästan tro att någon hade det i tankarna när kardantunneln byggdes. Tätt och fint.
Med tanke på allt säkerhetstänk borde det undersökas om det finns någon form av brandskyddade damasker istället, så är i princip kupén helt avskärmad från allt brandfarligt.
AC-paket
För hardcore fans som följer detta projektet så minns man kanske uppdateringen för tre år sedan att det köpts ett AC paket? Fullt förståeligt om de flesta följarna inte minns…
Vintage Air mini köptes för ett tag sedan, istället för att försöka leta donatorer på skroten. Ett tämligen (med amerikanska mått) fint byggt paket med elektriska spjäll, SPAL-fläktoch lite annat trevligt. En snäll kollega släpade hem detta på flyget. Bara historien om flygplatspersonalens irritation över ”trycksatta kärl” inte fick tas med på flyget är en historia i sig. Lång historia kort; Envis kollega – flygplatspersonal: 1-0.
Inga fel på paketet förutom en detalj; Det är recirkulerande! Dvs det tar inte in någon frisk luft, utan skickar bara runt luften inuti kupén. Så kan vi inte ha det…
Nedan; Stiligt paket. Dyrt, men kändes som helt ok produkt för pengarna faktiskt.
Nedan; Själva fläktinloppet sitter vänt nedåt, och framför inloppet löper såklart ingångar för vatten och gas. Med andra ord i princip omöjligt att få dit en friskluftskanal att ansluta en slang på.
Fläkten slets väck för att mocka upp en anslutning för luftkanal. Skrev ut en liten tolk i 3D-printern för att se att dimensionerna stämde. Nu ska bara luftintaget ritas, men det har inte gjorts än eftersom lämpligt friskluftsfilter skulle lokaliseras först (alltid bekvämt med filtrerad luft för en stackars pollenallergiker…).
Nedan; För att flytta luftintaget från alla slangar, fick fläkten helt enkelt vändas 180 grader. Eftersom den offsetade för mycket inåt och tog i burrör och lite annat, fick den samtidigt vridas något. Några pappmallar (och noggranna CFD-analyser för att försäkra sig om laminärt flöde, haha!!) senare så gick det att skriva ut en luftkanal i 3D-printern.
Nedan; Ett något justerat paket. Ser lite lustigt ut, men det är ingen som lider av det när det väl är på plats.
kamaxelgivare & bröstkåpa
Eftersom nya sprutet är lite mer sofistikerat än det gamla hedenhös-Electromotive som satt där tidigare, finns möjligheten att köra sekventiell insprutning. För att kunna det, behövdes en givare på kamaxeln. Inte helt trivialt att komma åt kamaxeln någonstans – fördelaren är sedan länge borta. Efter lite om och men konstaterades det dock att bröstkåpan framför kamaxeldrevet var bästa stället. Eller det minst dåliga i alla fall. Rätt mycket pyssel med att få dit en dock, vilket borde avspeglas i alla momenten nedan…
Ovan; Kamaxeldrivning och lämplig indikeringspunkt behövde ordnas för givaren
Nedan; Sagt och gjort – Väck med drevet, upp med det i fräsen och koordinatborra ett M6-hål. Två faktiskt – blev lite osäker på om hjulet var balanserat och man därmed skulle behöva montera en motvikt på andra sidan av hjulet. Under arbetets gång blev det dock ganska uppenbart att 19 grams extravikt på ena sidan knappast skulle bli ett problem.
Nedan; Indikeringspunkt tillverkad. Man kan använda en skruvskalle också, men jag ville ha så mycket material som möjligt för att få säker avläsning. Därmed blev det hockeypuck med stoppskruv och några små låsningar med TIG:en. Skruven sattes sedan med Loctite 270 som tål över 150 grader samt är oljeresistent.
Ovan och nedan; Sen var det dags för att ge sig på bröstkåpan. Friskt fräst och hälften vunnet, som man brukar säga…
Skrev ut ett antal fullskalamallar för att hitta lämplig position. Därefter körnslag i kåpan som får utgöra nolla vid fräsning. Hålet gick skrämmande snabbt att ta upp och sen fanns det ingen återvändo…
Ovan; När kåpan var fräst, var det bara att sätta igång med själva fästet för givaren. Rigga om fräsen, tillverka ny bit. Även denna med hål för att kunna nolla in fräsen inför slutgiltig bearbetning.
Nedan; Därefter över med bitarna till svetsen för att lappa ihop dem. Grundtanken var att svetsa från insidan för att behålla en snygg utsida. Tyvärr sprack det pga svårigheter att komma åt i dalen (som blir förhöjningen i ovankant på bilden), så den fick svetsas från utsidan också…
Nedan; Färdigsvetsad kåpa fick därefter en slutgiltig bearbetning i fräsen. Ville inte göra denna förrän efter svetsning pga det tunna godset. Resultatet blev ju dock ganska tjusigt. Givaren passade till och med!
Även höjdled (som är rätt känsligt) stämde så när som på någon hundradel.
Nedan; Färdigbearbetad och svetsad detalj. Nya anslutningar för vatten, eftersom någon tomte (undertecknad…) gav sig på dessa i förra motorbygget för ca 10 år sedan. Inloppet blev större än tidigare eftersom nya kylaren använder större slanganslutning.
Aluminiumet är 40 år gammalt gjutgods och har sett sina bättre dagar. Med andra ord målades det i… gjutjärnsgrått (!) för att matcha motorblocket.
Ovan; Pricken över i:et; en Firebird-block-off-mekanisk-bränslepumps-plåt. Köpt för 350:- för tio år sedan. Repig, sned fågellogga, för stor fågellogga som täcks av skruvskallarna samt en ytterkontur som inte stämmer med bröstkåpan över huvud taget. Samma land som kom på och utvecklade iPhone tillverkar alltså denna pryl… Högt och lågt. Nåja, den fyller sitt jobb i alla fall. Med tiden kanske det blir en egen, som såklart är urfräst på baksidan för att spara vikt.
Verktygsuppgradering
Vintern var kall. Inte mycket av den spenderades i garaget tyvärr, så vårens uppdateringar på bilprojektet är risk att bli lite… fattiga.
Inget liggande på soffan dock – i vinter har CNC-styrsystemet till garagefräsen som köptes för två år sedan fixats ihop och monterats. Ja, precis – numera har en CNC-fräs knutits till projektet, vilket borgar för smaskiga framtida uppdateringar…
Ovan; Hur lastar man 550kg fräs på hyrsläp när det inte finns någon travers eller lyft hos säljaren? Med hjälp av internetforum, såklart. ”Lilla” lastaren kom till hjälp och därefter gick lyften på släp ner till jobbet där den kunde lyftas av. Logistik att köra den direkt till garaget saknades, så det fick lösa sig med tiden…
Fräsen först – en Mattsson & Zetterlund VF600. Tillverkad i Sverige från typ 60- till tidigt 80-tal tror jag. Stabil historia och kan fräsa ungefär 300x200mm stora detaljer. Kan tyckas lite, men ganska få konstruktionsdetaljer är mycket större (och det går alltid att ta omtag om det skulle behövas). 550kg tung, vilket gjorde det ganska ”intressant” att baxa in den i garaget.
Den hittades på blocket uppe i norra Sverige. En äldre herre som köpt den för 20 år sedan och inte ens pluggat in den i väggen efter dess. Inga skador på bord, ingen rost osv. Väldigt fint skick. Verkar mest ha mysfrästs lite med då gejdrar var i nyskick.
Problemet med en 20 år gammal maskin som inte gått något är att allt fett har torkat in. Allt fett. Överallt. Med andra ord fick den plockas ned i molekyler och tvättas rent. Detta har skett sporadiskt under en ettårsperiod ungefär (bilen har gått som prio1). Samtidigt konverterades den från trapetsskruv till kulskruv, tillsammans med lite allmän översyn.
Nedan; …genom att plocka ner den i molekyler kunde den tas hem till garaget. Si och så med molekylerna dock – fundamentet kvalade in på ca 220 kg! Det gick åt ett par öl för att få in det i garaget. En fräs som inte varit använd på 20 år har en hel del intorkat fett i sig. Allt fick plockas ner och tvättas rent innan den ens var startad och kontrollerad att den funkade.
Nedan; Allt fick rengöras… allt.
Trapetsskruvarna kastades ut till förmån för kulskruvar. I samband med konverteringen drogs även slangar där smörjnipplar tidigare satt för att kunna centralsmörja hela fräsen.
Det senaste året har den mest använts för att göra något enstaka mindre jobb i form av plana av en yta, borra lite hål och andra väldigt enkla uppgifter.
I oktober -15 köptes stegmotorer, drivsteg och alla andra delar som krävs för en CNC-konvertering och kring december sattes arbetet igång med (ganska) full fokus.
Inlärningströskeln får man nog så här i efterhand säga ha varit väldigt hög – mycket av problemlösningen har varit Trial and Error i kombination med ett antal timmar läsandes på internetforum för att se hur andra löst felen. Sånt tar tid…
Förutom att bara få fart på fräsen och dess mjukvara (mach3), har vändglappen minimerats, samt lära sig CAM-beredning också tagit ett litet tag. Myckettid lades på att leta glapp och nu, efter många timmar, slår måtten på någon hundradel ungefär. Den precisionen räcker gott och väl för en garagemaskin. Repetetivt vetifasen – den klarar säkert inte 1000 detaljer med exakt samma mått, men några enstaka program har hittills använts ca 10ggr ggr med samma resultat.
Ovan; Massor med tid gick åt till att leta och justera glapp för att få precision. För stunden glappar det ca 2 hundradelar i Y-led, och 7 i X-led. Blir till att försöka få rätt på hundradelarna i X-led med tiden. Tills vidare får den bekänna färg och sen blir det säkert någon form av uppgraderingsprojekt när man fått lägga några timmar i den.
Elskåp, hemmabyggt och göms i fundamentet. 400V/230V/24V/5V. Geckodrives stegmotordrivare och lite annat godis. Trångt som fasen, men fräsen står på hjul för att kunna vara flyttbar i det lilla garaget, och då går det inte att hänga skåpet stationärt på väggen…
Ovan; Det finns inget som är så skönt som första gången, oavsett vilken debut det handlar om. I det här blev det ett rör till catchtanken. Simpel detalj, men ack så najs att titta på medans fräsen gör jobbet själv.
Nördigare ”dröm” än så här finns nog inte, men det kommer nog bli den bästa garagekompisen någonsin (sorry, Affe. Jag och fräsen har liksom en relation på en annan nivå). Med tanke på hur många detaljer som har handjagats fram och hur många timmar som lagts på sånt, skulle ju en sådan här maskin ordnats fram redan i början av projektet. Men nu finns det ju å andra sidan saker som kan uppgraderas efter att bilen har reggats, så det är nog ingen risk att fräsen råkar bli dammig…
Det som aldrig kommer sluta fascinera med en CNC-maskin är ju att den jobbar på utan att man själv behöver vara aktiv. En sådan sak resulterar ju i dubbla framsteg i garaget eftersom undertecknad kan hålla på med något annat. Åtminstone lite senare – först måste nyhetens behag gå över; Efter åtskilliga timmars handjagande är det lätt att fastna framför fräsen med drömsk blick och se hur den dansar över bordet helt av sig själv.
Ovan; Nu börjar 20m2-garaget bli ganska fullt… En bil på tio kvadrat, fräs, verktyg och bänk tar ytterligare 3m2. 7m3 kvar att gå på med andra ord. Oceaner av plats…
Drivaxeldamasker, det löste sig
Fortsätter förra veckans raljerande kring damaskerna och hittar någon sida på nätet som beskriver hur man sticker av flänsarna till diffen och borrar nya mönster för att kunna köra Porscheknutar med Ford 8.8-klump. Jättebra, men det känns lite trist att börja om nu, särskilt eftersom man med porscheaxlarna fortfarande behåller yttre Lincoln-knuten.
Denna och förra veckans post beskriver ett arbete som sker till och från under flera veckor (samt några nätter då sömn hade föredragits istället). Till och från kollas alternativen upp. Flera av alternativen kollas dessutom flera gånger, i hopp om att internet har ändrat sig och blivit snällt. Det har det inte.
Men så kommer snilleblixten, som anses självklar i efterhand, att utöka sökningen kring systerbilar. Inte bara till de som har samma bakvagn, utan till de som använder samma diffklump istället. Vilket även inkluderar bilar som Ford F150, Lincoln Navigator, Ford Explorer och ett helt batteri med andra fordon.
Plötsligt trillar det upp nya sökträffar på eBay, nya affärer som listar komponenter. Gud verkar ha anlänt med damaskåterbäringen som eftersöktes i förra veckan.
Ovan; Plötsligt finns de bara där, på eBay av alla ställen. Hela internet har dammsugits, och nu finns de framför näsan på en. Haschtag Win på den liksom!
En eBay-säljare får förtroendet att leverera damasker efter att ha visat dimensioner som stämmer ganska bra överens med Mark VIII. Visserligen lite små, men gummiprylar brukar vara övertalbara när det gäller töjning. Leveransen tar evigheter känns det som. Två evigheter till och med, men till slut finns de hemma i garaget och skall bara provas.
De passar. Lyckan är obeskrivlig och motivationen når nya toppnivåer!
Ovan och nedan; Montering av drivaxlarna var tämligen rätt fram.
Reservdelsförsörjning – damaskjävlar
Projekt byggda i Europa bör byggas med Europeiska delar. Projekt byggda i Europa bör byggas med Europeiska delar. Projekt byggda i Europa bör byggas med Europeiska delar. Projekt byggda i Europa bör byggas med Europeiska delar. Projekt byggda i Europa bör byggas med Europeiska delar. Projekt byggda i Europa bör byggas med Europeiska delar. Projekt byggda i Europa bör byggas med Europeiska delar. Projekt byggda i Europa bör byggas med Europeiska delar. Projekt byggda i Europa bör byggas med Europeiska delar. Projekt byggda i Europa bör byggas med Europeiska delar. Projekt byggda i Europa bör byggas med Europeiska delar.
Precis.
Den här typen av omfattande projekt har alltid sin beskärda del av motgångar. Det har hittills varit förhållandevis lite, men just drivaxlarna visade sig bjuda upp till en riktig strultango.
Ovan; En av låsringarna sprack när axlarna demonterades. Att få tag på en ny var lättare sagt än gjort eftersom måtten var lite ovanliga. Det hade inte gått, om jag inte gnällt på ett forum där en vänlig läsare gick ut och inventerade sitt garage – hittade två C-ringar i nästan exakt samma dimensioner, tog sig tid att kontakta mig och erbjuda mig dessa, samt lägga sakerna i kuvert, frankera och lägga på lådan. Ett beteende som är lite ovanligt i dagens självupptagna värld. Ett oändligt stort tack skall denne personen ha – helt ovärderlig hjälp!
Tyvärr är dock inte detta den enda motgången…
…”Någon” har nämligen råkat köra en skruvmejsel genom ena damasken vid demontering.
Ingenjörajäveln ska alltså inte bara trumlas i ett bad av svarvspånor och tvagas med rostfri stålborste (från ”länkarmsfadäsen” här om veckan), utan därefter även doppas i begagnat drivaxelfett (alla vet hur det luktar). Man kan såklart rädda klanterier likt denna genom att beställa hem reservdelar och ha på hyllan när det är dags för återmontering, men detta gjordes inte. Antagligen pga det helt enkelt var omöjligt att få tag på reservdelar, i kombination med en slapphänt 80-talist med inställningen ”men ååååh palla, det fixar jag sen liksom”.
Ovan; Det är ett yttepyttelitet hål, här på bild lagat med cyanoakrylat i ett försök att reparera befintliga damasker. Lagningen blev nog bra, och kommer nog att hålla. Men det känns ändå lite risky att förlita sig på dessa. Dessutom behöver reservdelar finnas om/när dessa går sönder så om man låter bli att försöka hitta nya damasker nu, skjuter man bara problemet framför sig.
Men det är ju bara att leta upp lämplig internetshop och köpa en uppsättning nya?
Drivaxeldamasker till Lincoln Mark VIII, som tillverkades mellan 1993 och 1998. Lincoln… Få se nu, Ford lade ner märket vid 2008. Reservdelsförsörjning, från nedlagda märken? Lika troligt som att solcellsdrivna ficklampor eller pedaldrivna rullstolar skulle bli nästa storsäljare.
Efter några timmars googlande börjar insikten om att de faktiskt inte finns som reservdel längre komma, men en del företag verkar fortfarande ha lite gammalt liggandes på hyllorna. Med andra ord inventeras varenda drivaxeldamaskåterförsäljare (hej, Sture Allén) för att se vad som finns. Yttre damask finns lite överallt. Inre lyser med sin frånvaro. Det är så klart inre som är trasig.
Forumanvändare borde ha svar? Lincolnförarna verkar dock inte vara den typen av bilägare som byter damasker för skojs skull. Svaren uteblir och ovissheten är fortfarande komplett.
Det säljs ”refurbished half shafts” i någon form av utbytesprogram, så damasker måste finnas någonstans. Drivaxlarna är ju kortade, så det är knappast lönt att köpa nya kompletta axlar. Timmar och åter timmar på google leder mig fram till en gammal HTML-sida om en kille som byter bakvagn i sin Mustang och skriver om nåt litet företag i innersta USA som hjälpte honom.
Hittar företaget, inser att det är fax som gäller om man ska ha tag på dem då inget telefonnummer eller mailadress finns på hemsidan. Faxar flera gånger utan svar.
Hittar även några andra företag som sysslar med drivaxlar. Ett svarar att ”jajamän, de har minsann damasker på lager – hur många vill jag ha?”. Lyckan är komplett! Prisa Gud, här kommer damaskåterbäringen! Jag tänker att tio stycken är lika bra att köpa, men priset är ganska saftigt. Fortsätter konversationen, dubbelkollar några mått, skickar bilder och allt är ”inga problem”. Varningsklockor ringer – har de koll? Ber om bild tillbaka på produkten de planerar att UPSa till Sverige. Ingenting stämmer, man ser direkt att den inte passar. Konfronterar dem och frågar hur de tänker sig att den skall passa – möts av tystnad. Tillbaka på noll. Prisa inte Gud. Förbannade drivaxeltillverkare, utsända av Satan själv för att försvåra för entusiaster.
Ovan; Drivaxeldamaskjävlar. Två stycken.
Tillbaka till internet då. Dags att börja leta gemensamma bilmodeller där samma bakvagn funnits. Lincoln MKVIII, Ford Mustang SVT Cobra (specialmodell med individuell bakvagn), Ford Thunderbird och någon Oldsmobile. Mustangen har större drivaxlar, så de damaskerna passar inte. De andra tillverkas det inte heller några damasker till längre.
Någonstans i misären önskar man sig att man hade europeiska delar. Även om de inte fanns längre, hade det varit enklare att traska in på Biltema och hitta något som låg nära i dimensionerna. De stora reservdelsnasarna har inte mycket amerikanardelar på hyllorna och tyvärr skiljer sig det en del kring kulturen olika bilbyggarkontinenter har. Millersippande, köttgrillande och beväpnade konstruktörer i USA väljer helt andra dimensioner på sina damasker än sömnframkallande, humorlösa och gråklädda Düska ingenjörer.
Det ser helt enkelt mörkt ut och funderingar kring hur man tillverkar gjutverktyg för damasker börjar mala i bakhuvudet. Även funderingar kring va fan man håller på med egentligen vaknar till liv – alla andra tittar på TV, umgås med vänner eller sover medans en annan sitter och kuckelurar i garaget och försöker sig på stordåd. Kanske dags att bli som alla andra istället?
Bilhelvete.
Diffkåpa
Lite justeringar har fått göras på diffkåpan för att den skulle passa. Bland annat har det stora originalfästet frästs bort och ersatts med en slät plåt. För de två nya upphängningarna fick den ena göras ett litet urtag på diffkåpan också.
Ovan; Nymodifierad kåpa i svart skrud. Det är visserligen aluminium, men den var inte särskilt fin i skicket, så det fick bli färg ovanpå.
Nedan; Så klart satt luftningen precis där bussningen behövde plats. Inte mycket att be för mer än att fräsa bort den och skaffa ett nytt filter. Med lite planering hamnade det fortfarande bakom oljefällan på insidan.
Ovan; Loctites packning är oslagbart. Tyvärr torkar det i röret eftersom användningsintervallet är ganska sällan. Högelastiskt är det dock – ”fnuppen” på bilden lyckades dras ut ur pipen i ett stycke.
Nedan; Kåpan och klump på plats. Måtte den aldrig behöva tas ner igen då det var ganska tungt och osmidig. Även om huset är i aluminium, så väger diffen as (35kg). Rostig magnetisk plugg fick följa med obehandlad – man ska ha något att uppgradera i framtiden också…
Nedan; Därefter stoppades drivaxeländarna i för att kunna mocka upp rätt längd av axlarna. Otroligt svårt att ta vettiga bilder på undersidan av bilen.
Bränslepump
Som med allt annat blir det special hela tiden…
Här är bränslepumpen, en Walbro 255, som kommer monteras inuti tanken. Så mycket som möljigt hamnar i tanken för att inte sprida komponenter i onödan. Risken om något skulle läcka blir mindre, samt ljudnivån från pumparna blir också mindre.
Ovan; Bränslepumpen monteras internt. Lägre ljudnivå och skulle den börja läcka så blir läckaget internt i tanken istället för i bagaget. Känns bättre. Det blir en del special – Pumpen är förvisso standard. Kopplingen för att mata pumpen med bränsle är ganska hemmapysslad dock. Själva banjoskruven har fått hålet uppborrat för bättre flöde. Slangen är 10mm, och till M10 banjoskruvar finns bara 8mm slangfäste i vanliga affären. Med andra ord får ett fäste för 12mm väljas istället… och adaptrar (i aluminium, som glödgats efteråt för att bli mjukt) tillverkas.
Högra bilden: Fräsig AN-koppling köptes på trycksidan för att kunna använda rör upp till tankflänsen (även den egentillverkad eftersom hålbilden för pumpar, nivågivare etc blir special…). Även där var så klart hålet för litet. 60 sekunder senare i svarven så är hålet större.
Nedan; Även utloppet från catchtanken fick en egen dimension på slanganslutningen. Pumpen monterad på catchtanken i medföljande vibrationsskydd (blir intressant att se om det tål bensin…). Mer om catch-tanken nästa vecka.
Speciallösningar tar en hel del tid. Egentligen är det sällan själva tillverkningen som tar tid, utan snarare komponentletandet – försöka hitta komponenter i rätt dimensioner innan man ger upp och tillverkar eget…
Bromsar, renovering
Det här var ju (från början) ett budgetprojekt. Det är fortfarande ett budgetprojekt i form av att det går mycket arbetstid istället för pengar för att lösa problem.
Budgeten innebar att det var bara och glömma att köpa nya flashiga AP-ok, Brembo eller liknande. Och sexkolvsok måste det ju vara för det är ju… coolt.
E-bay dammsögs efter möjliga kandidater långt innan projektet egentligen påbörjades och ett par rejäla hejdare lyckades ropas hem för ett blygsamt kostnad. Som vanligt med begagnade prylar är det alltid bra att börja med att renovera dem, så slipper man strul senare längs resan. Bromsoken var inget undantag – nya O-ringar, ny ytbehandlning på alla fästelement, polering av värmeplåtarna och lite ny färg lyfte oken till nyskick.
Lekte även med tanken på att fräsa in PONTIAC på oken, men det föll på att det inte fanns någon gratis-tid i en CNC fräs någonstans. Budgetprojekt, remember?…
Ovan; När väl oken kom hem från staterna visade de sig vara betydligt större än förväntat. På den högra bilden står ett A4-kuvert i oket som en storleksreferens. I välkänt Wilwood-manér, har den svarta ytbehandlningen övergått till en lila-violett färg. Inte så lockande, så…
Nedan; …därför togs beslut att måla om dem. Plasti-Cote motorgrund och därefter Pontiacs motorblåa nyans som en liten hyllning till företagets glansdagar. Även fästelementen fick ny svartoxid då den gamla var rätt rostig på sina ställen.
Nedan; Antingen besitter undertecknad små nätta frökenfingrar, eller så har bromsoken kapacitet att stoppa vilket lok som helst. Det sistnämna stämmer bättre. Som synes på handleden är de inte fjäderlätta, men strax under 4kg/st får anses vara ok för ett så stort ok.
Återmontering
Motorn är på väg ihop igen. Nya lager, nya packningar och en polerad vevaxel äregentligen enda ändringen sedan tidigare. Ren upprustning med andra ord. Den är redan rätt så potent och något mer trimbehov finns inte i dagsläget.
Specen ser ut så här;
- Motorblock: Pontiac 400, borrat 0.030″, allt gjutskägg på insidan bortslipat, toppdeckat 0,010″
- Vevaxel: Pontiac 400, slipad 0.020″, internt balanserad
- Kolvar & stakar: Eagle smidda kolvar och SCAT H-profil med ARP-skruv. Allt viktbalanserat och nästan 3kg lättare än original
- Övrigt bottendel: Sachs kamkedja, några modifieringar för förbättrad torrsumpssmörjning, egenbyggt torrsumpstråg, borttagen fördelare, Meziere elvattenpump
- Kamaxel: Hemlig, men ingen Mount Everest-kamprofil utan en ganska modest. Körbarhet – inte maxeffekt…
- Toppar: Kauffman Racing D-port alu-toppar. Titanventiler och retainers. Ferrera lättviktsfjädrar. CNC-portade till 320 CFM
- Insug: Edelbrock Torker I, konverterat för insprutning. Bosch 465cc-spridare, någon Mustang-tryckregulator. Wilson Racing spjällhus. DTA S80-PRO styrsystem. LSx separata tändspolar
- Barnes 4-stegs torrsumpspump samt värmeväxlare i kylaren för snabbare uppvärmning – och bättre kylning.
- Smitt svänghjul, lättat från 17kg till 8kg
- ARP-skruv i stakar, överfall, topplock mm
Lagren visade efter knappt 100 mil ganska högt slitage varför veven har polerats. Det finns anledning att misstänka ett krånglande oljetryck som boven i dramat och som nu förhoppningsvis är åtgärdat.
OM oljetrycket skulle fortsätta krångla blir det till att riva hela motorn och börja leta felorsaker. Det har inte gjorts denna gång pga tidspressen – motorn behöver hamna i bilen snart för att systemen kring denna skall kunna konstrueras och därför var ett tvåmånadersprojekt med motorn föga lockande. Även om oljetrycket fortsätter krångla lite, kommer den i alla fall hålla över besiktningar och när väl pappren finns i handen kan bilen lämnas till lackering samtidigt som jag bygger ny motor. Prioriteringar med andra ord…
Men, inget ont som inte har något gott med sig. Ett motorprojekt måste så klart spåra ur, och det är ju inte helt omöjligt att fodra ner blocket och byta vev så att motorvolymen blir 301 istället för 400cui. Denna historiska motorvolym hade passat bilmodellen otroligt bra, samtidigt som V8:or låter rätt härligt på 10000rpm. Dessutom finns det ett Kinslerinsug som ligger i gömmorna i garaget. Med andra ord hade nästa version av motorn sett ut något sånt här istället. Nästan så att man hoppas på fortsatta problem för att ha en ursäkt att bygga ny motor!
Ovan; Nya lager och vevaxelpackning. Använder BOP-engineerings packning istället för original-rep som brukar börja läcka inom 10 mil…
Nedan; Det är alltid svårt att komma ihåg att dokumentera nya prylar. Så fort man får dem i handen vill man montera dem, varför kameran ibland glöms av. När jag tittar i kameran är den enda bilden på den nypolerade veven tagen strax innan överfallen åker på. Försökte kontrollera lagerspelet med lite plastiguage, men jag tror Mekonomen har haft sina plastigauge på hyllan för länge eftersom den var snustorr och pulveriserades så fort man tog i den. Lyckades hitta några bitar som var någorlunda, men man ska nog inte ta de 0.076mm som en 100% sanning…
Ovan; Nya lager. Clevite har visst köpts av Tyska Mahle sedan jag handlade lager senast. Kan ju knappast gjort saken sämre att jänkarna fått lite tysk styrning.
Nedan; BAM! Veven sitter åter där den hör hemma. Allt draget enligt instruktioner och fritt fram att nagla fast torrsumpstråget med gott samvete.
Ovan; Och så var det kamkedjan… En Sachs-historia med ställbar förtändning genom att man helt enkelt sätter det nedre drevet i ett annat läge. Det visade sig faktiskt att den satt 2º tidigare än 0º. Motorn gick väl inte direkt dåligt, men den hamnar på 0º tills att denna inkarnationen av motorn är helt mappad och körbar innan det experimenteras vidare. Tveksamt hur den där förtändningen påverkar motorn egentligen eftersom tändsignalen tas direkt på vevaxeln numera med ett 60-2 drev. Den påverkar med andra ord endast öppning och stängning av ventilerna.
Nedan; Brickan som håller kamdrevet har sett sina bästa dagar. Den hade deformerats kraftigt och låg och tryckte mot skruvens gängor. Ny bricka svarvades av verktygsstål och fett applicerades på gängor och under skalle innan den momentdrogs. Inte för att momentet är särskilt kritiskt på just den skruven, utan snarare för att man får chansen att känna sig som en high-tech rymdraketbyggare när man står där med momentnyckeln i högsta hugg.
Motorjobb…
Motorrenoveringar är verkligen ett nödvändigt ont, inget annat. Där finns redan någon som tänkt ut hur allt ska vara och även om man så klart kan börja experimentera här, är det inget som intresserar mig. Motorn är renoverad för mindre än 1000 mil sedan, men ett rutinbyte av lagren kändes ändå nödvändigt. Efter granskning av de gamla lagren, togs beslutet även att lämna in veven för polering.
Ovan; Så just nu är veven urplockad och lämnad för polering.
Blocket behöver nog en ommålning också. Frågan är om det skall vara gjutjärnsgrått igen, eller om det skall vara Pontiac 60-talsblått istället. Som äkta ingenjör fyller färgen egentligen bara en funktion – skydda mot korrosion – och därför kan det vara svårt att bestämma nyans. 😉
Ljusblått eller grått – vad tycker du?
Guld – vad annars?
En sak var klar när det här projektet påbörjades; inga snabbfix, inga ”det där gör jag sen” och definitivt inget ”det får bli som det blir”. Genomtänkt från början. Att slutresultatet kan betraktas som en prototypbil där eventuella barnsjukdomar kommer tvinga fram omkonstruktion är ju självklart (därav att allt finns CADat – enkelt att konstruera om i datorn utan att behöva riva hela bilen). Men medvetna fullösningar under byggets gång finns inte.
Så gäller även funktioner som tex värmen i kupén. Det blir AC i bilen, men så många värmekällor som möjligt försöks förebyggas vid redan vid källan. Torpedväggen vid torrsumpstanken, som innehåller 100ºC olja, har därför isolerats med blingig guldfolie. Samma folie kommer hamna i kardantunneln och avgassystemet kommer få reflektorplåtar där det är möjligt.
Om alla felkällor åtgärdas så kan det ju innebära att man 9 av 10 dagar kan klara sig utan AC, vilket i sig då hade resulterat i ca 20kg viktbesparing om man kunnat acceptera lite för varmt den där tionde dagen…
Gaspedal
Man ska inte försumma de små detaljerna… Känsla i ratt, pedaler och växelspaken är såklart något av det viktigaste på hela bilen…
Ovan; Även gaspedalen har fått en översyn. Det var typiskt fabriksglapp i alla leder vilket såklart behövde ordnas till. Original plast-pedal har fått ge vika för rejsig aluminiumpedal istället (som uppenbarligen inte är med på bilden…)
Nedan; Det fanns både axiellt glapp och radiellt i leden till vänster. Det axiella var enkelt att åtgärda med en bricka (fjädern på andra sidan pressar dessutom axeln lite lätt mot brickan, vilket gör att det blir nollglapp trots låg friktion). Radiellt fick hålet genom pedalarmen brotchas upp till ett metriskt. Därefter svarvades en mässingsbussning som pressades i axeln och i sin tur bearbetades till någon hundradels spel mot axeln. Resultatet blev riktigt bra!
För att kunna justera pedalen i rätt vinkel mot golvet, ordnades en liten justerskruv på pedalaxeln.
Nedan; Jag vill helst slippa allt för mycket skruvar på torpedväggen. För att göra detta, ordnades en adapterplatta mellan torpedvägg och gaspedal. Ett fäste för gaspedalsfästet med andra ord. I denna svetsades M6-skruv som skallarna skars bort på för att få en slät undersida.
Originalglappet togs bort med hjälp av kopparshims som lades mellan plattan och pedalarmen. Glappet blev inte riktigt noll här, men bra nära.
Överambitiöst kanske? Men gaspedalen är ju halva känslan av bilen! 😉