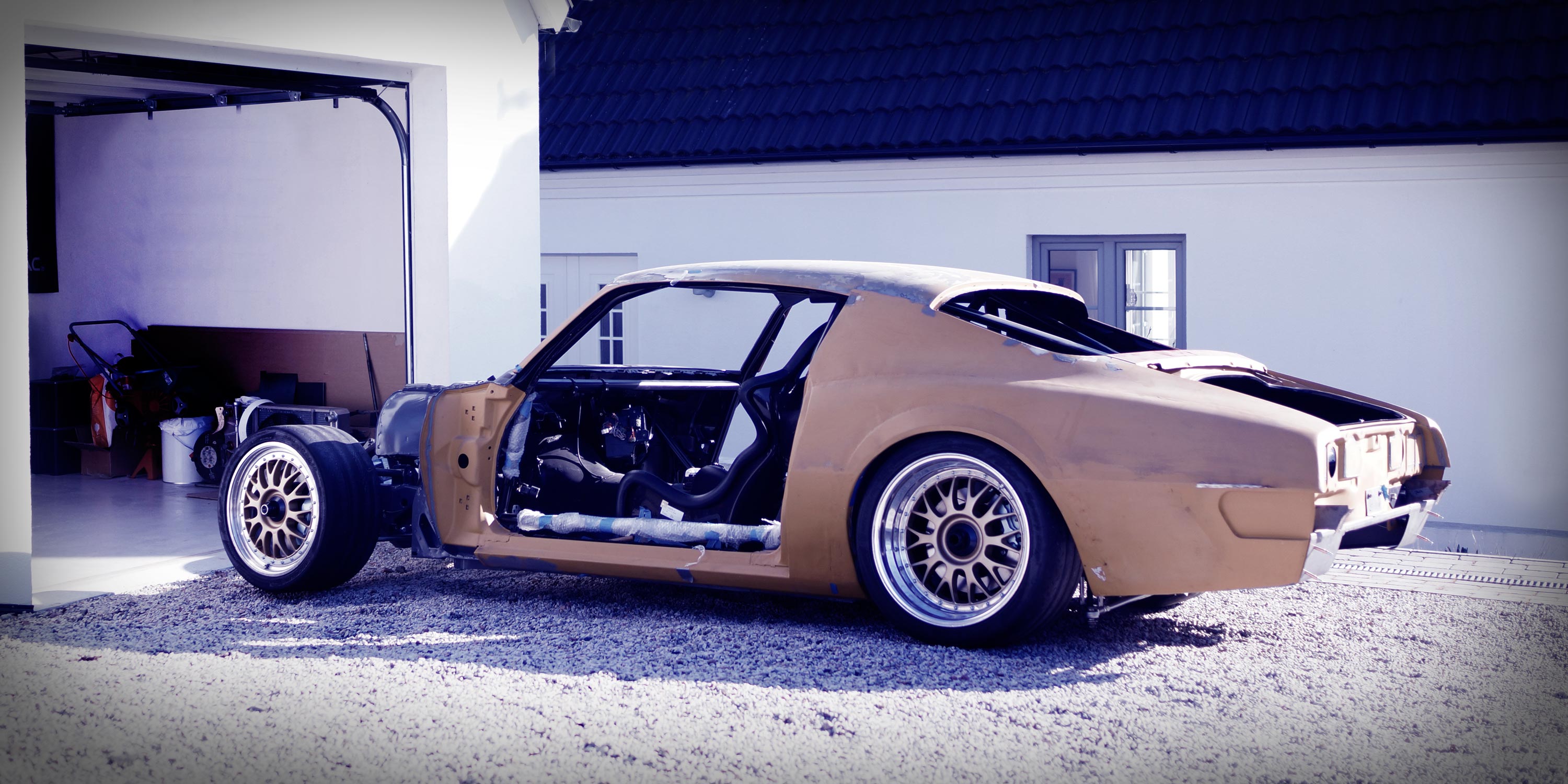
Bromsvåg och pedalställ
Bra bromsbalans mellan fram och bakhjul innebär bromsvåg. Detta hade ganska enkelt kunnat integreras i bromspedalen vilket inneburit att cylindrarna kunnat skruvas direkt på torpedväggen. Det innebär dock att om man någon gång skulle vilja gå tillbaka till servoassisterad bromsfunktion så får man börja kapa och svetsa i torpedväggen vilket kanske inte alltid är så kul. Det finns ändå en risk/chans att bilen kompletteras med servo i framtiden om pedalen skulle visa sig vara allt för tungtrampad.
För att både kunna äta kakan och ha den kvar letades en box, där vågen installeras i, upp. Grundtanken var att tillverka en egen (så klart!), men denna Sellholmbox dök upp på en säljesannons till ett överkomligt pris.
Ovan; Tanken var alltså att det skulle se ut så här om det var hemmagjort. Nu trillade det ju in lämpliga detaljer i färdigt skick, och då kändes det inte lönt att gå sin egen väg längre…
Ovan; Wilwoodcylindrar i lämpliga diametrar, samt Sellholm box.
Nedan; Cylindrar monterade och även en bild på delarna installerade. Orgie i egentillverkade prylar… Vippan till själva bromsvågen fick tillverkas och skymtar på bilden. Även axeln till hållaren. Eftersom jag bara hade tillgång till metriska brotschar (att ta upp hål i vippan med) fick det tillverkas ett nytt rör till bromsvågen som hade metrisk utsida. För att inte få in damm eller motorljud i kupén, användes en gummibälg från MecMove. För att få denna att sitta fast mot torpeden, 3D-printades en fläns att fästa dem mot som i sin tur skruvades mot bromsvågen. Många detaljer som knappt syns när det väl är klart.
Nedan; Färdigt. Även bromsrör på plats. På bilden syns även lite andra prylar -3D-printade hållare till dämparresevoarerna och kopplingscylindern. Den sistnämnda kommer lite mer om nästa vecka.
P-broms… Det går bra nu…
För den som tror att det bara är att ”bygga ihop” en bil med egna komponenter är det ganska fel. CAD, misslyckade försök, ny CAD, misslyckat… Ny CAD, prov i verkligheten, tillbaka till CAD osv. Tålamodsprövande det här med att bygga bil.
P-bromsen är inget undantag. Den fick aldrig riktigt vara med på ritbordet utan vilket egentligen aldrig var meningen. Det bara blev så. Sånt får man sota för i efterhand genom extra arbete och anpassningar. Bilderna visar bara ett första misslyckat försök. Grundtanken var att försöka belysa att det ofta ligger väldigt många försök bakom egenutvecklade prylar, men kameran fick inte riktigt alltid följa med på alla försöken… Misslyckat försök att försöka visa misslyckade försök med andra ord.
Ovan; Försök 1 blev någon form av skruv i befintligt fäste på spindeln. Ganska lagom placering på hålet i förhållande till var armen på oket hamnar. Dock känns konstruktionen något klen och vajerdragningen efter spindeln och längs karossen är fortfarande ganska oviss.
Nedan; Dock blev i alla fall vajerdragningen från infästning och upp till ok väldigt bra. Kylkanalen till bromsskivan fick bändas lite i sidled. Bromsvajrar är faktiskt original till bilmodellen (trummor med andra ord). Fjädern på vajern är för trummorna. Jag har låtit den sitta kvar, då längden var förbluffande lagom och den faktiskt tvingar tillbaka bromsarmen vilket gör att… Ja, det känns bara bra helt enkelt.
Nedan; Försök två blev egentligen en vidareutveckling av försök 1. En platta som sprider kraften på två skruvar, samt lite justering på infästningen för att inte vajern ska krocka med dedionen.
Högra bilden visar den fantastiska anledningen till att om man ska rita prylar i CAD, ska man rita allt. Även fästelement. Oket kunde placerats 10mm längre bakåt egentligen, men nu hamnade det där det hamnade. Lagom mycket i vägen för att vara för lite i vägen för att egentligen orka bry sig. En fil löste biffen även om det är principiellt fel.
Nedan; Monterat på bilen känns det ju såklart väldigt bra. Till och med vajern visar sig gå att leda någorlunda bra fram till originalpedalen.
Ovan; Så var det bara wiren som skulle dras också!
I en optimal värd hade allt byggs klart innan någon ytbehandling gjorts (karossen skulle alltså inte varit lackad än) och då skulle man såklart bara svetsat fast ett sådant här fäste istället. Nu fick det skruvas i karossen istället. Försänkt skruv på undersidan för att… öh, minska luftmotståndet eller nåt.
Nedan; Handbromswire infäst. Dragningen visade sig bli riktigt bra. I detta fallet ren tur snarare än framförhållning då P-bromslösningen som sagt gjorts efter allt annat varit färdigkonstruerat och tillverkat. En slangklämma håller fast wirehöljet för att avlasta infästningen lite och spara wirehöljet från knäckning eller liknande.
Även en drivaxel-mock kan skymtas på bilen. Mer om det senare…
Bromsar…
Med bromsar monterade var det dags att sätta igång med rördragning. Lite komponenter har handlats hem från andra sidan pölen. Försöker generellt använda samma komponenter fram och bak för att behöva ha färre reservdelar på hyllan. I detta fall blir det samma längd på bromsslangar fram och bak, samma anslutningar och samma rörnipplar i hela systemet. Alla relevanta prylar kan köpas som reservdelar i Sverige, men priserna råkar vara lite bättre i staterna så om inte tidspressen finns beställs det därifrån.
Ovan; Ett gäng komponenter från Speedway Motors i staterna. Alltid lika roligt att öppna påsar med nya, rena prylar i. Rostfria rör (blänker ju fint mot den sidenmatta RAL7015-färgen) istället för vanliga kopparrör. Man får hålla tungan rätt i mun så att man inte borrar hålen fel för komponenterna i nylackade prylar.
Nedan; Samma bromsslangar fram och bak, samma adptrar, nipplar, infästningar osv fram och bak. Ju färre olika komponenter desto enklare. Att dubbelkona rostfria rör visade sig inte vara det enklaste. Biltema-verktyget är att betrakta som en engångsartikel i sammanhanget. För att få tillräcklig klämkraft, fick det klämmas med hjälp av skruvstädet, och en egen dubbelkoningsfnutt fick tillverkas. Svårt att se fnutten på bilden nedan till höger.
Nedan; Rördragningen till bakbromsarna var lite pillig, men den följer väldigt nära golvet i alla fall. Funderade ett tag på att dra det inuti kupén istället, men det sitter rätt skyddat där det sitter på bilden så det blev undertill istället. Högra bilden visar slangdragning till bakvagnen. I vänsterkant av bilden sitter slangen i ett T-kors till rör som löper längs dedionen. För att inte få okontrollerad rörelse i slangen, begränsades den lite genom en hylsa (som den löper fritt i) som sitter mitt på. Det visade sig att hälften av slanglängden räckte (lika längd fram och bak för att förenkla reservdelslagret) och blev över för fjädringsvägen.
Bromsar bak
När det kom till bromsar bak gällde det att hitta något som matchade frambromsarna vad gäller kolvarea. Mestadels av lasten läggs på frambromsarna under retardation, Därför är inte styvhet riktigt lika viktig bak som på fram. Det tänkte jag inte på när jag handlade, utan kan snarast klassas som en efterhandskonstruering för att framhäva hur genomtänkt och perfekt det här projektet är…
Bakre oken var nämligen väldigt små (fysiskt) jämfört med framoken, som är gigantiska. Dock är undertecknad övertygad om att de kommer fylla uppgiften väldigt bra.
Ovan; Wilwood IR-GT4R. Rätt kolvdiameter, låg vikt och klarar nog jobbet som bakbromsar bra. 4-kolvsok har ju så klart inte någon P-broms… och det tycker ju SFRO är rätt bra att ha. Med andra ord köptes en uppsättning p-bromsok. Även dessa tillverkade av Wilwood. Sannolikt utvecklade av någon ingenjör som var trött på sitt jobb. Antagligen är det en cheddarluktande, engineer-Bob som tyckte det var viktigare att komma hem till grillen och dricka Bud än att göra bra produkter. Därefter har gissningsvis gjutverktyg varsamt tagits fram av slarviga små barnfingrar fem mil utanför en stad som inte Uppdrag Granskning känner till i Bolivia och till sist har en oförstående marknadsavdelning börjat sälja produkten utan att ens titta på den. Med andra ord som vilken vanlig manick ”made in the USA” som helst…
Nedan; Oken har fått en spacer monterad för att kunna greppa över de breda bromsskivorna. Eftersom det inte finns någon vettig infästning på dem har glidpinnar konstruerats. (många väljer att istället att montera oken stumt i en tunn plåt och sen montera denna i spindeln och låta plåten göra arbetet – jag måste ju så klart gå min egen väg och uppfinna hjulet på nytt istället… Hur var det nu med svenska, smörgåsbordsätande midsommarstångsdansande ingenjörer? De kanske inte är så mycket bättre än Budweiserdrickande jänkediton?)
Ovan; Ganska mycket TV-kocksvarning i dessa uppdateringar eftersom det aldrig visas någon action utan bara resultat, men så här blev det. Liten temperaturdekal på oket också för att kunna ha lite koll på värme… Temperaturskalan börjar på 100 grader, så svårt att ha dem som termometer på garagetemperaturen men förhoppningsvis kommer väl bilen ner från pallbockarna innan OPEC slutar sälja olja.
Nedan; I fantastisk kvalitetsanda visade sig hårdvaran till de fantastiska P-bromsoken kom så klart obehandlad i vanligt svartstål. De Aluzink-behandlades för att hålla lite längre än bara första provturen. Högra bilden visar bromsoksadaptern, en av få CNC-frästa detaljer i projektet. Även pegs och pinnbultar till bromsoket är CNC-svarvade, signerade ”Joakim”. Tack för hjälpen!
Wilwood förtjänar inte på något sätt ett dåligt rykte pga p-bromsarna. De är imponerande slarvigt tillverkade när man jämför dem med deras andra keramiskt coatade, unobtanium CNC-billettjohejsan megabromsok. Som med allt annat får man vad man betalar för och för 400:-/st kan man nog inte begära mycket mer. Framoken har ett listpris på 2800 dollar/st och P-bromsoken 99 dollar/paret som jämförelse…
Skulle det visa sig att de inte fungerar, finns det många standardbilar som använder liknande P-bromsok, Audi R8 tex. Prislappen är så klart inte 400:- (och vikten är betydligt högre…), så Wilwoodoken får bekänna färg först…
Ovan; Audi R8-ok (höger) samt Brembo eftermarknadsok (vänster).
Bromsar fram
Tidigare i våras skruvades bromsoken fast på spindlarna. Känslan av att skruva fast dem för första gången och det sitter perfekt centrerat och allt passar utan en enda provmontering tidigare – när man har byggt alla detaljer runtomkring själv är… obeskrivlig. Det är inte för att låta dryg som det tjatas om detta hela tiden, men det är en enorm kick att konstruera saker och sen få kvittot genom att det blir exakt så som man tänkte sig. (undrar om man får äta upp det där citatet efter första provkörningen?)
Bromsslangar krävde dock en hel del funderande för att få rätt på. Dels skulle längden bestämmas, sen kan inte slangen vridas, utan bara böjas vilket också ställde till en del. En del klurande i att få sånt att löpa fint.
Bromsarna förresten. Wilwood P6R (även kallade Prolite på vissa ställen). Magnesium/aluminiumhus med keramiskt coatade kolvar (för att inte överföra värme från beläggen) samt polerade, rostfria plåtar inuti tråget för att reflektera bort strålningsvärmen. Mums.
Ovan; För att inte slangen skulle ta emot någonstans och för att inte utsätta den för konstiga vridningar fick det experimenteras en hel del. Det slutade med att en position hittades där slangen behövde fixeras vid spindeln för att röra sig rätt. Med lite enkel hårdvara löstes problemet…
Nedan; Buntbandet på bilden ovan utbytt mot plåt och gummiklämma. När beläggen hamnar i oket, då känns det nästan på riktigt!
Ovan; På plats, äntligen. Bara att trampa på pedalen nu med andra ord.
Bromsar, renovering
Det här var ju (från början) ett budgetprojekt. Det är fortfarande ett budgetprojekt i form av att det går mycket arbetstid istället för pengar för att lösa problem.
Budgeten innebar att det var bara och glömma att köpa nya flashiga AP-ok, Brembo eller liknande. Och sexkolvsok måste det ju vara för det är ju… coolt.
E-bay dammsögs efter möjliga kandidater långt innan projektet egentligen påbörjades och ett par rejäla hejdare lyckades ropas hem för ett blygsamt kostnad. Som vanligt med begagnade prylar är det alltid bra att börja med att renovera dem, så slipper man strul senare längs resan. Bromsoken var inget undantag – nya O-ringar, ny ytbehandlning på alla fästelement, polering av värmeplåtarna och lite ny färg lyfte oken till nyskick.
Lekte även med tanken på att fräsa in PONTIAC på oken, men det föll på att det inte fanns någon gratis-tid i en CNC fräs någonstans. Budgetprojekt, remember?…
Ovan; När väl oken kom hem från staterna visade de sig vara betydligt större än förväntat. På den högra bilden står ett A4-kuvert i oket som en storleksreferens. I välkänt Wilwood-manér, har den svarta ytbehandlningen övergått till en lila-violett färg. Inte så lockande, så…
Nedan; …därför togs beslut att måla om dem. Plasti-Cote motorgrund och därefter Pontiacs motorblåa nyans som en liten hyllning till företagets glansdagar. Även fästelementen fick ny svartoxid då den gamla var rätt rostig på sina ställen.
Nedan; Antingen besitter undertecknad små nätta frökenfingrar, eller så har bromsoken kapacitet att stoppa vilket lok som helst. Det sistnämna stämmer bättre. Som synes på handleden är de inte fjäderlätta, men strax under 4kg/st får anses vara ok för ett så stort ok.
Headers lll – final touch
Alla projekt tar så klart alltid längre tid än man tror. Så även grenrören. Men nu äntligen är de färdigsvetsade och ytbehandlade. Den gråaktiga hinna som synts på de tidigare bilderna är ca 10 år gammal zink-behandling. Headersen blästrades då och målades med zinkspray från CRC. Därefter kördes de genom en pulverlackeringsugn för att bränna bort färgen och lämna kvar zinket. En sorts fattigmanscoating med andra ord. Resultatet har dock hållit otroligt bra. Ytan blev väldigt sträv, och drar åt sig smuts rätt lätt. Dock verkar de självrensa sig vid körning.
Denna gången fanns det inte tillgång till någon pulverlackeringsugn. Å andra sidan är inte tanken att de ska hålla 10 år heller (för då kommer de säkert sitta där i tio år…). Det sprutades på zinkfärg igen, som fick torka på vanligt sätt. Efter det isolerades rören med värmeskyddande bandage för att hålla temperaturen i motorrummet så låg som möjligt.
Ovan; Budgetcoatade headers blev ju bra bra. Hålet för Syresensor skymtar också på den sista collectorn i ovankant av bilden. Högra bilden visar avgasbandage. Lyxade och köpte rostfria ”buntband” från samma tillverkare till det underbara priset av nästan 400:- för 10st. Visade sig att det är exakt samma som finns som artikel på företaget där jag jobbar. Exakt samma. Men här kostar de 1.61+moms att köpa in. Varje gång det hamnar en motorsportbenämning på något, tiodubblas alltid priset…
Nedan; Inför lindningen sattes headersen upp i skruvstädet. Remsorna mättes upp och doppades i vatten för att bli lite mer flexlibla.
Nedan; Ja jävlar. Fyraochenhalvtimme senare så var båda två gjorda. Visade sig vara ganska klurigt att få till en bra lindning eftersom rören ligger tight mellan varandra. För att isoleringen ska göra någon nytta, skall den ju ligga mot röret. Det krävdes viss fantasi och planering när man närmade sig de första collectorerna.
Nedan; Men det blev ganska bra efter några försök. På vissa ställen har lindan dragits som en 8 mellan rören och därefter runt om ytterligare ett varv för att täcka allt. Bilden nedan kan man skymta lite isolering på röret som försvinner in i den stora klumpen.
Nedan; Eftersom så mycket svetsats på headersen, provtrycktes de efteråt. Det visade sig vara en väldigt bra idé – några mindre porer här och var som de läckte från. Nu vet man att de är täta och slipper försöka täta dem på plats sen när bilen väl är startad. Numera sitter headers på plats, lindade och klara.
Att linda headers med värmebandage väcker alltid lite diskussion (vilket syns på facebooksidan). Det stressar stålet mer då inte värmen kan strålas ut, utan allt sluts in i röret. Dessutom isolerar man från ”fel” håll när man gör det – en korrekt isolering skulle suttit på insidan av röret för att hindra värmen från att nå stålet. Med tiden kommer en korrekt lindning utmatta materialet (i teorin och säkert i praktiken om man typ hela tiden kör höga varvtal), men frågan är om detta är ett akademiskt problem eller ett reellt. Jag resonerade som så att denna version av headers är prototyp inför nästa, och då gäller det att skaffa sig mycket erfarenhet helt enkelt. Erfarenhet av att tillverka dem, om det funkar med lindning eller om man behöver coata, hur 4-2-1-modellen känns jämfört med 4-1 osv. Egentligen skulle man ju till och med coatat den ena sidan och lindat den andra men det känns kanske lite väl extremt…
Håller de tre säsonger är jag mer än nöjd. Då är förhoppningsvis resten av bilen utsorterad och man kan lägga en vinter på att bygga ett riktigt avgassystem.
Nedan; CRC Zink användes för att måla grenrören.
Garaget på bilden är extrautrustat…
En liten snabb notis om garaget och dess förutsättningar också. Det tjatas om den lilla storleken på garaget och det är ganska utmanande att planera detta på ett smart sätt. Utan loftet ovanpå hade det varit omöjligt, men som det nu är kan man lägga upp i princip allt som inte behövs för stunden där uppe istället.
För närvarande är garaget utrustat med en vettig meckbänk, verktygsvagn och ett slipat och målat betonggolv. Några mer smarta lösningar finns inte än. Det som dock står på önskelistan är: AC/DC TIG-svets, CNC-fräs, Tryckluft, bättre belysning, smidigare lyftsystem av bilen än domkraft och pallbockar, samt uppvärmning. En bättre lösning än att behöva stå med vinkelslip i samma lokal önskas också, men om man helt enkelt ska sluta skära saker med vinkelslip eller om man ska skaffa en annan lokal för detta återstår att lösa. Smörjgrop hade inte varit fel heller, men att börja bila upp en platta som bara är några år gammal känns väldigt väldigt fel…
Först ut blev tryckluft. Kompressorn har placerats på loftet tillsammans med regulator, vattenavskiljare osv. Därefter togs hål i taket för att kunna komma ner med slangar. Eftersom garaget bara är 6×3,4m gjordes bara två hål genom taket – ett i varje ände. Vid porten placerades 10m slangrulle (för att kunna nå ut på gården), och vid arbetsbänken sattes vanliga CEJN-kopplingar direkt i taket för hålla det avskalat och enkelt. Använder man inte tillbehören kan man lätt koppla ur dem och då syns det knappt att tryckluften finns där.
Här borde så klart funnits en bild på kompressorn också, men röran på loftet tänkte jag bespara internet… Det är i alla fall en helt vanlig 24L-kompressor. Inget man lackar bilar med eller kör tryckluftsdrivna verktyg med, men den räcker ett mindre garage.
Ovan vänster; Vid sidan om meckbänken hamnade uttag för arbete vid bänk och blivande fräs. Höger; På andra sidan i garaget sattes 10m slangvinda. Det är denna som kommer få fungera både utanför garaget, samt vid arbete i och kring bilen. Ja, på bilden finns det några andra projekt som återstår att ”städas upp” lite. Den vita plastlådan som skymtar på bilden är en radiomottagare för kommande öppning av infartsgrindarna, självklart egenkonstruerad den också.
Nedan; Istället för att leda slangar längs taket i garaget och dra ner dem längs väggarna, drogs slangar på loftet och ner genom bjälklaget. Det ger ett lite mindre rörigt intryck, samt gör även att garaget är lite lättare att hålla rent i framtiden.
Resultatet – hur har man ens kunnat klara sig utan tryckluft tidigare? Underbart att äntligen ha det på plats. Kompressorn på loftet gör också att man slipper en hel de av bullret vilket är väldigt skönt.
Serpentinrem
När det gäller kringutrustning på motorn, brukar dessa vara relativt spatiöst utplacerade. Det har såklart och göra med de omständigheterna som gällde just när GMs ingenjörer skulle placera dessa. Platsen fanns säkert och då var det ingen anledning att försöka tränga ihop saker och ting.
Men för detta projektet finns det en del förbättring. Dels har V-remmar en tendens att vibrera på höga varv när de ser ut som på bilden nedan, men framför allt är det rätt många tunga komponenter som sitter placerade väldigt högt. AC-kompressorn väger tex rätt många kilon och hade nog passat bättre längst ner osv.
I Pontiacens fall är det ganska mycket som ändrats, och som därmed påverkar förutsättningarna. Till exempel är vattenpumpen eldriven istället för remdriven. Det innebär att de andra kompenterna inte kan placeras fysiskt lika högt längre eftersom remmarna då tar i utsticket på vattenpumpen. Lika så servopumpen utgörs ju numera av en elmotor även den. Med andra ord har alltså komponenterna reducerats något.
Ovan; Det finns inget som säger att det på bilden inte fungerar bra. Men det finns inget som heller säger att det inte går att förbättra lite. På bilden är vattenpump, servopump, AC-kompressor och generator remdrivna. Servo- och vattenpump är eldrivet på Pontiacen och högsta prioritet var att sänka tyngdpunkten.
Nedan; Första utkastet till monteringsplåt gjordes för att faktiskt kunna se hur delarna hamnade och avstånden från andra komponenter. Där går ingen pappskiva att använda, så jag kostade på mig en skuren plåt.
Nedan; Knappast första försöket i datorn… Snarare trettiosjunde, men nu börjar det likna något. På bilden syns generator, AC-kompressor och torrsumpspump. Torrsumspumpen går på separat rem pga utväxlingsförhållandet. AC-kompressorn sitter lägst eftersom den var tyngst och generatorn ovanpå för att hålla drivremmen till högersidan på motorn. V-rem lämnas till förmån för multirib, för att därmed kunna lägga till ett extra remhjul och då öka ingreppsytan på både generator och kompressor.
Nedan; Några revisioner senare i datorn ser det ut så här. AC-kompressorn stagas i bakkant mot motorblocket och blir på så sätt en bärande detalj i konstruktionen. Generatorn kommer även skruvas mot toppen (plåtblecket vid sidan om generation), om det behövs. Tjockare gods då 4mm var lite i klenaste laget. Några lagom lättningshål utplacerade för att hålla vikten på rimlig nivå gjordes också. Slutligen gjordes justerplåten för generatorn (och därmed remspänningen) som en lös detalj istället, på så sätt kunde mer justermån klämmas in utan att det tog i generatorn i innersta läget.
Längden på remmen kan varieras mellan 1280mm och 1360mm vilket borde räcka. Kanske skulle kollat att längder i det intervallet går att beställa också innan ordern på plåt skickades…
Headers ll
Problemet med V-motorer är att mycket måste göras två gånger. Man ska inte bygga ett insug, utan två insug. Man ska inte renovera en topp, utan två toppar osv. Headers är inget undantag, dessutom ganska arbetsintensivt vilket gör att passagerarsidan var hur kul som helst att bygga. Förarsidan blev bara en pina eftersom det mest kändes enformigt.
Nåväl, inga direkta överraskningar. Precis lika mycket arbete som förra veckan, och lika mycket detaljnoggrannhet trots att det rör sig om begagnade skrotprylar. Några lärdomar har dock förts med till nummer två – främst bättre fogberedning i form av att slipa bort lite av zinkfärgen innan svetsning, samt rengöra från sot på insidan. Pinsamt att erkänna att man inte gjorde detta på första. Det hade varit betydligt mer lättsvetsat då.
Ovan; Utgångsobjektet. Samma problem här som på passagerarsidan – Treans rör som sticker bakom fyrans kan inte sitta där det sitter utan måste flyttas framåt. Dessutom ska de ihop till 4-2-1 vilket innebär att allt får kapas sönder ändå.
Nedan; Skippar alla kapbilderna eftersom de ungefär ser likadana ut som förra veckan. Istället är här slutresultatet (som blev rätt bra faktiskt). Nackdelen med att inte CADa allt, är såklart att man alltid stöter på något trubbel. När väl grenröret hamnade på plats, visade det sig att bromsröret bara låg någon centimeter ifrån. Funkar säkert, eftersom headersen skall lindas med värmeisolering men det är ändå lite tråkigt om vätskan i bromsröret skulle börja punktkoka. Liten risk, men lika bra att leda om röret så att det hamnar längre från headersen. Enda som är kvar i svetsväg är att bestämma sig för utformningen på avgassystemet så att motsvarande rörstump kan svetsas på headersen.
Nedan; Ibland är det bra när man får saker över efter modifieringar – här är ca 2kg överblivet material. Lägg märke till alla tunna ringar – det är rätt mycket provpassning, kapa lite till, provpassning och sen kapa lite till. Blir en del snitt…
Headers I
Eftersom ingenting är original längre, passar inte heller något som är avsett för originalbilar heller. Med andra ord finns det inga headers som passar Pontiacen. Rätt väg att gå, hade såklart varit att sätta sig ner och fundera över max varvtal, bottenvrid och toppeffekt och utefter dessa parametrar räkna ut de perfekta grenrören och därefter varsamt konstruera hela avgassystemet där insidan på svetsarna slipas för att inte skapa onödig turbulens när de stressade avgaserna rusar mot mynningen på avgasrören för att möta världen utanför. Ribban på det mesta i projektet ligger ganska högt, så det hade självklart varit rätt väg att gå här också.
men…
Så hade man gjort i en optimal värld. På grund av att abstinensliknande ryckningar i högerfoten har ökat under den senaste tiden kommer det göras avkall på en del arbete till förmån för att få klart bilen så fort det bara går. Inget att oroa sig för – avgasystem är perfekta vinterprojekt för framtiden när allt annat på bilen lirar och man sett att inget behöver konstrueras om. Just nu finns det bättre arbete att göra än att investera tre månader i att bygga avgassystem.
Ett annat argument som talar för att de sista hästarna ur motorn inte behövs just kan också vara den pappersprocess som bilen ska passera och där man inte imponeras av höga effektsiffror…
Ovan; Utgångsobjektet – vanlig no-name grenrör/header. Torpeden börjar bakom fjärde avgasporten, dvs röret som löper bakom denna port behöver justeras lite…
Ganska snabbt stod det klart att 4-1 headers inte kommer kunna användas på bilen. Motorn är ju sänkt, flyttad bakåt och dessutom har bilen en markfrigång som kan få en wettextrasa att känna sig tjock. Kravet var att inte en millimeter av avgassystemet skall hänga ner under karossen. Subframe, rambalkarna i karossen och profilerna som utgör subframeconnectors mellan dessa bildar längsgående skenor är perfekta (nja, repor i underredet är ju aldrig kul…) som hasplåtar om man skulle slå i någonstans. Då ska inte avgassystem eller annat slitas loss.
Problemet med detta är att på höjden under golvet finns det bara 50mm (47mm för att vara exakt) att planera in ett avgasystem på. Det innebär alltså 4o-45mm diameter på rören och om inte motorn ska dö av förstoppning måste det alltså sluta med plattovala avgasrör. Med andra ord kändes 4-2-1 headers som ett ganska naturligt val. En snabb googling visade på att det faktiskt också är en rätt bra kompromiss med ökat vrid i mellanregistret och en rad andra fördelar. Rätt utformat alltså, vilket kanske inte är chansen att det blir här. Dags att servera en snabblagad huvudrätt, kallad avgasröra, med andra ord.
Headersbyggarkarriären är ganska begränsad och därför togs beslutet att slakta de gamla headersen och helt enkelt utgå från dessa. Primär- och sekundärlängder fick bli vad det blev. Prio är endast att de ska få plats, inte läcka, samt att samla lite erfarenhet för framtida avgasprojekt.
Nedan; …och alla andra rör också visade det sig. Ja, det blir lätt så. Ett rör sparades – inte för att det inte behövde flyttas, utan för att ha koll på riktning för var de nya ska hamna. Sen började pusslandet…
Ovan; Flertalet provmonteringar för att se att det går fritt som det ska
Nedan; ”Färdigt” resultat, så när som på sista kollektorn och helsvetsning. Får bli när båda sidor är klara.
Sprängkåpa
Det kallas visserligen sprängkåpa, men kåpan som håller växellådan mot motorn bör nog snarare betraktas som ett petskydd om svänghjulet skulle besluta sig för att ge upp.
Motorn är ju sänkt vilket innebär att man får ta till några extra knep för att förhindra att denna eller växellådan blir lägsta punkten i bilen. Nedre kanten av ”petskyddet” hängde ner under karossen vilket gjorde att detta frästes bort innan växellåda och motor monterades ihop. Detta tänktes på redan när motorn provmonterades i bilen för något år sedan, och då kunde en linje ristas på sprängkåpan längs lägsta nivån på chassit för att på så sätt enkelt kunna veta var det skulle fräsas ner i framtiden.
Ovan; Fräsningen gjord. Före-bild glömdes så klart av i all iver att få jobbet klart för att kunna få i motorn. Men bultmönstret på den högra bilden var slutet istället för öppet i botten (på bilden alltså). Är inte särskilt orolig för att tappa styrka i sprängkåpan. Muncie-lådorna på 70-talet och även automatlådorna är ju öppna nedtill, så det bör inte vara några problem.
Nedan; Lyxade till det och tillverkade även ett skydd för svänghjulet för att det inte ska studsa in sten och skit i 2mm alu. Har tidigare kört utan… Ung och dum… Passade på att göra ett par rillor i plåten för att få den att se lite mer ”OEM” ut. Lite smuts och stenskott på den så kommer inte ens den mest nitiske granskaren kunna gissa att den inte suttit där från början.
Nedan; Tog av kåpan för att ta en bild. Svårt att ana, men svänghjulet ligger ca 10mm ovanför ramverket/subframen. Värmeisoleringen för det kommande avgassystemet syns också bra här på bilden.
Nedan; När man pratar om petskydd, så är det dess rätta benämning. Nedan finns ett par avskräckande bilder som jag hittade på datorn för ett tag sedan. De har legat på hårddisken ett antal år, så vem som tog dem och hur det gick till är nästan glömt. Dock var det någon form av stripkörning, ganska mycket effekt och slicks inblandade. Vad som hänt vet jag faktiskt inte, men man blir ändå medveten om att bra kvalitet på prylarna är viktigt. Skrämmande är det i alla fall med tanke på stålbitarna som lär flugit med rejäl fart. ”Ormen” på nedre vänstra bilden är startkransen som normalt sitter runt svänghjulet…
(Motor + växellåda) * chassie = Bil
Så var dagen äntligen kommen. Dagen då det var dags att para ihop drivlina med resten av bilen. Motorn har hängt i ställ sedan 2010, så det är på tiden att den får komma tillbaka i bilen nu.
Den har faktiskt varit och vänt i framvagnen en snabbis för ett tag sedan för att kunna bygga motorfästen. Det enda som skapade viss dramatik under monteringen var problemen med en lätt bil och ett tungt motorpaket; Hela bilen dansar omkring på pallbockarna när man försöker montera (med bräckjärn och gummiklubba) motorn i bilen. Under vissa stunder i monteringen blev det onödigt dramatiskt. Eftersom ingen kylare eller andra prylar fanns i motorrummet, hade det varit bättre att ha bilen ståendes på marken. Lätt att vara efterklok.
Ovan; Här är alltså skönheten. Saknas lite kringutrustning, men eftersom fästen för generator osv måste tillverkas behöver motorn sitta på plats för att se att inte framvagnen tar i.
Nedan; Svänghjulet lättades 7kg (15 kg originalvikt!) redan förra inkarnationen och efter att en Centerforce 11″-koppling monterats skruvades lådan på.
Ovan; Ett lättviktsbygge som detta skulle egentligen haft en annan motor. Inte något så förutsägbart som en LS1, utan varför inte något mer spännande som en Audi V8 från RS4, eller ännu roligare en Hayabusa V8 med lite överladdning eller kompressor. Gjutjärnsblock är ju knappast imponerande, men vissa val avgörs av hjärtat och inte hjärnan. Dessutom blev ju framvagnen så himla lätt så bilen hade blåst bort utan ett bojsänke till jänk-motor.
Nedan; En liten parentes, men 20m2 garage kräver kreativitet. Att lyfta i en motor blir inte helt enkelt om man inte rullar undan verktygsskåp, arbetsbänk, fräs och flyttar allt annat framför bilen. Då går det precis. Det som är ännu svårare blir att fånga momentet på bild för att kunna visa det. Där behövs en hel del kreativa placeringar med kamerastativet. En del av bilderna är faktiskt tagna utanför garaget, in genom dörren för att få med så mycket på bild som möjligt. Behöver mer vidvinkel än 16mm med andra ord.
Nedan; Den glider in! Och vilken skönhet sen. Plötsligt är projektet fulländat – inga fler tekniska revolutioner behöver göras i den här bilen när en så vacker motor hamnar på plats. 20cm längre bak i bilen än tidigare borgar för relativt bra viktfördelning. Om du läser här och råkar äga ett par vågar som du kan tänka dig att låna ut en dag hade det varit väldigt intressant att väga bilen som den står nu.
Nu blir det en välförtjänt semesterpaus ett antal veckor och sen är veckouppdateringarna tillbaka.
Permafrost
Motorer utvecklar värme och växellådan är inte direkt iskall heller. Det blir visserligen AC i Pontiacen, men det finns ingen anledning att inte försöka begränsa värmen som strömmar in i kupén ändå. Det gör att ACn inte behöver jobba lika hårt vilket i sin tur innebär mer effekt på bakhjulen. Förebyggande arbete har redan gjorts genom att montera guldfolie där torrsumpstanken kommer sitta. Folien är effektiv då den reflekterar bort mycket av strålningsvärmen.
När det kom till kardantunneln, fanns det mer plats för lite mer värmedämpning än bara tunn folie och därför införskaffades 0,3mm aluminium med 3mm glasfiber på baksidan (snarare 5mm tjockt i verkligheten) från Karnag. Alun har lite sämre reflektionsförmåga (även om den nog kan betraktas akademisk i sammanhanget), men glasfiberisoleringen kompenserar då den inte bara tar strålningsvärmen, utan isolerar också.
Ovan; Före och efter. Hela utrymmet bak till växellådans slut har klätts in. Finns risk att även resten av kardantunneln kläs med tiden. Området ovanför ljuddämparna kommer få 0,5mm aluplåt som reflektionsmaterial. Att bygga bort värmen är värt några kilon.
Nedan; Närbild. Skarvarna har tätats med armerad alutejp.
Nedan; Jag var lite snål när torpedväggen byggdes och det är tajt med utrymme kring topparna på motorn. För ta minimalt med utrymme monterades därför mer guldfolie. Att det blev guldfolie har ingenting med Bling-faktorn att göra. Inget alls.
Nedan; Folien måttades ut genom att fixera den med magneter. När den var bra klippt, lossades ena hörnet (fortfarande med magneter på resten) och därefter drogs skyddsplasten bort bit för bit tills att den var helt monterad (bild ovan).
Tråg på plats
Tråget är på plats på motorn. Blev hur bra som helst och flänsen (3mm) räckte gott och väl för att inte deformeras när pinnskruvarna drovs. Snart dags att börja på oljeledningarna mellan tråget och pumpen.
Ovan: Nymålat, Rostfria pinnskruv, kopparfryspluggar och muttrarna till kommande ledningar från tråget till pumpen har kommit hem. Två saker är synd med ett sånt här fint tråg. 1: Det sitter underst på motorn – ingen kommer se det. 2: Sannolikt kommer nåt litet oljeläckage, kylarläckage eller bara vägdamm att sunka ner det inom tio mil efter uppstart.