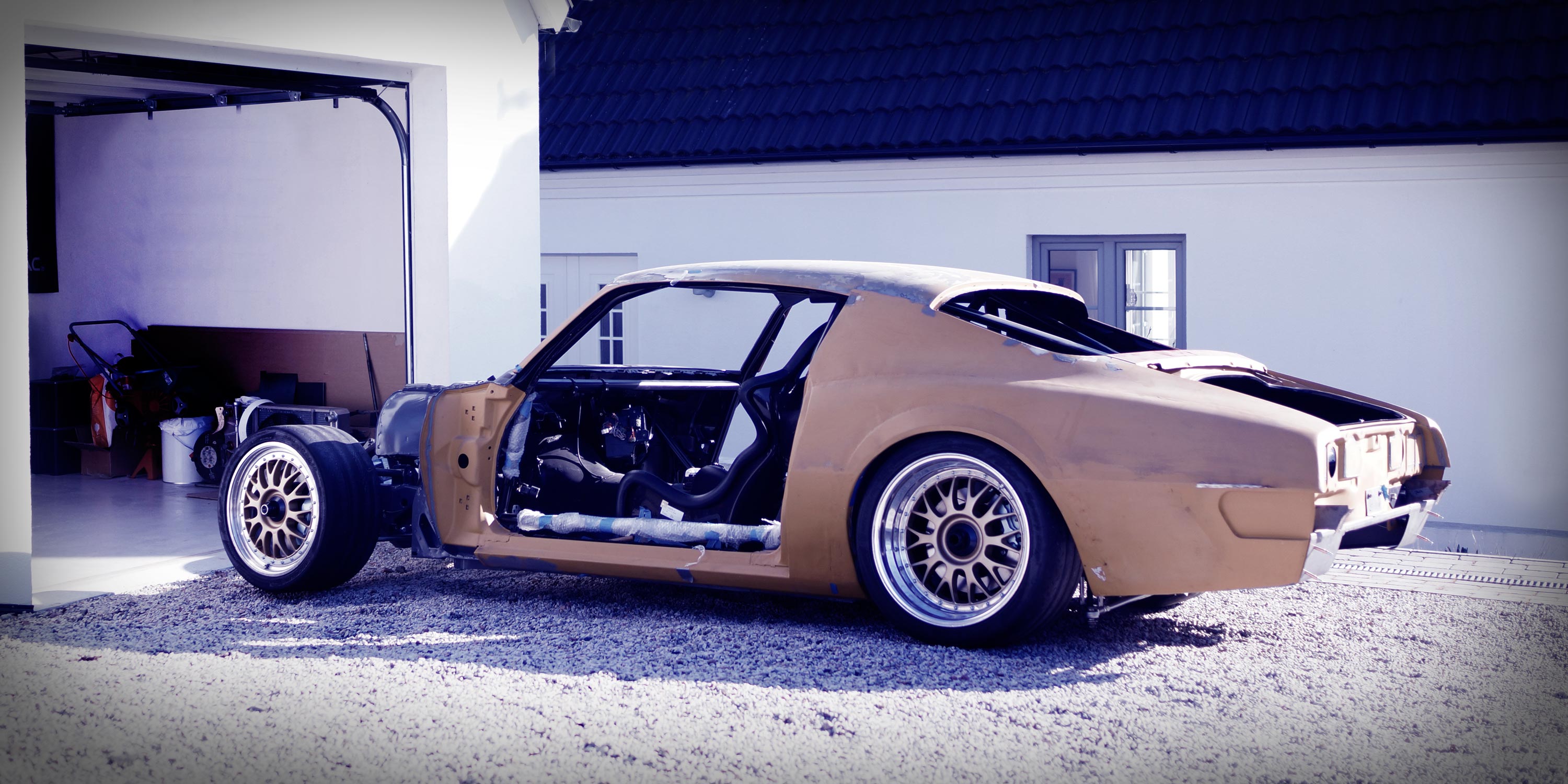
kamaxelgivare & bröstkåpa
Eftersom nya sprutet är lite mer sofistikerat än det gamla hedenhös-Electromotive som satt där tidigare, finns möjligheten att köra sekventiell insprutning. För att kunna det, behövdes en givare på kamaxeln. Inte helt trivialt att komma åt kamaxeln någonstans – fördelaren är sedan länge borta. Efter lite om och men konstaterades det dock att bröstkåpan framför kamaxeldrevet var bästa stället. Eller det minst dåliga i alla fall. Rätt mycket pyssel med att få dit en dock, vilket borde avspeglas i alla momenten nedan…
Ovan; Kamaxeldrivning och lämplig indikeringspunkt behövde ordnas för givaren
Nedan; Sagt och gjort – Väck med drevet, upp med det i fräsen och koordinatborra ett M6-hål. Två faktiskt – blev lite osäker på om hjulet var balanserat och man därmed skulle behöva montera en motvikt på andra sidan av hjulet. Under arbetets gång blev det dock ganska uppenbart att 19 grams extravikt på ena sidan knappast skulle bli ett problem.
Nedan; Indikeringspunkt tillverkad. Man kan använda en skruvskalle också, men jag ville ha så mycket material som möjligt för att få säker avläsning. Därmed blev det hockeypuck med stoppskruv och några små låsningar med TIG:en. Skruven sattes sedan med Loctite 270 som tål över 150 grader samt är oljeresistent.
Ovan och nedan; Sen var det dags för att ge sig på bröstkåpan. Friskt fräst och hälften vunnet, som man brukar säga…
Skrev ut ett antal fullskalamallar för att hitta lämplig position. Därefter körnslag i kåpan som får utgöra nolla vid fräsning. Hålet gick skrämmande snabbt att ta upp och sen fanns det ingen återvändo…
Ovan; När kåpan var fräst, var det bara att sätta igång med själva fästet för givaren. Rigga om fräsen, tillverka ny bit. Även denna med hål för att kunna nolla in fräsen inför slutgiltig bearbetning.
Nedan; Därefter över med bitarna till svetsen för att lappa ihop dem. Grundtanken var att svetsa från insidan för att behålla en snygg utsida. Tyvärr sprack det pga svårigheter att komma åt i dalen (som blir förhöjningen i ovankant på bilden), så den fick svetsas från utsidan också…
Nedan; Färdigsvetsad kåpa fick därefter en slutgiltig bearbetning i fräsen. Ville inte göra denna förrän efter svetsning pga det tunna godset. Resultatet blev ju dock ganska tjusigt. Givaren passade till och med!
Även höjdled (som är rätt känsligt) stämde så när som på någon hundradel.
Nedan; Färdigbearbetad och svetsad detalj. Nya anslutningar för vatten, eftersom någon tomte (undertecknad…) gav sig på dessa i förra motorbygget för ca 10 år sedan. Inloppet blev större än tidigare eftersom nya kylaren använder större slanganslutning.
Aluminiumet är 40 år gammalt gjutgods och har sett sina bättre dagar. Med andra ord målades det i… gjutjärnsgrått (!) för att matcha motorblocket.
Ovan; Pricken över i:et; en Firebird-block-off-mekanisk-bränslepumps-plåt. Köpt för 350:- för tio år sedan. Repig, sned fågellogga, för stor fågellogga som täcks av skruvskallarna samt en ytterkontur som inte stämmer med bröstkåpan över huvud taget. Samma land som kom på och utvecklade iPhone tillverkar alltså denna pryl… Högt och lågt. Nåja, den fyller sitt jobb i alla fall. Med tiden kanske det blir en egen, som såklart är urfräst på baksidan för att spara vikt.