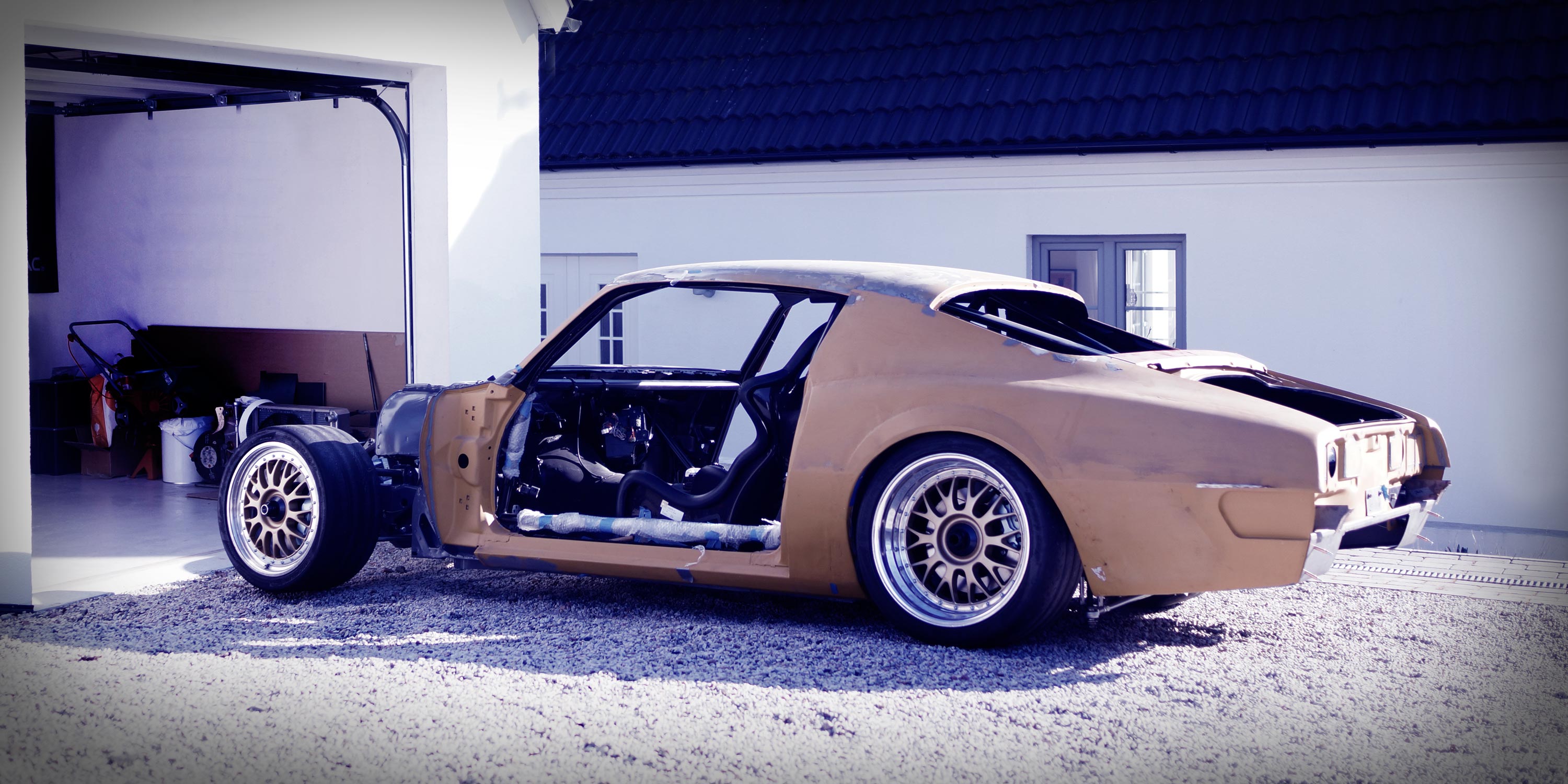
Kategori: Suspension
Framvagnsgeometri
Det är inte helt enkelt att få till en vettig framvagnsgeometri. Eftersom det är många variabler som ska stämma är det svårt att fokusera på en parameter tex. Det är som med Rubiks kub – man får försöka ta hänsyn till allt samtidigt. Vilket i sin tur innebär att om ett mått ändras fem millimeter kan det innebära vinst på camberkompensation, men brakförlust för rollcentrat.
Jag funderade länge på om jag skulle presentera bilder med måtten utsatta pga. risken att folk ”stjäl” ritningen. Det blev måttsatt (allt utom spindeln…) till slut eftersom jag inte kommer köra racing och därmed inte har någon konkurrens att tävla med. Titta gärna på bilderna och låna gärna inspiration till ditt eget projekt. Försök dock inte kopiera geometrin till ditt eget bygge utan att veta vad du gör.Väghållning är farliga saker. Eller rättare sagt avsaknaden av den. Har du inte koll på hur de olika parametrarna påverkar chassiereaktionerna så läs på innan du bygger. En bra bok i ämnet är ”Milliken & Milliken – Race Car Vehicle Dynamics”. Väl investerade 700 kronor.
Ovan; Så här blev det alltså.
Det enda kravet som fanns inför ritandet av framvagnsgeometrin var att övre länkarmen inte skulle krocka med den befintliga stålprofilen i framvagnen. Om det gick att uppfylla? Nej, såklart inte. Självklart skulle övre länkarmen nästla sig in i profilen och hamna ungefär mitt i den. Vinkelslipen kommer alltså behöva laddas med den stora kapklingan… Suck.
Ovan; Så klart skulle övre länkarmen hamna mitt ramprofilen. Trots allt fipplande och trixande visade det sig vara omöjligt att få till en bra geometri med övre länkarmen monterad ovanpå ramprofilen. Den hamnade för högt helt enkelt.
Nedan; Hur det ser ut vid två graders krängning. 0,45º camberkompensation och Rollcentrat rör sig ca 1mm/grad krängning. Jag ville knyta rollcentrat till bilens tyngdpunkt (CGH), men eftersom tyngdpunktens placering i dagsläget är okänd blev det lite att skjuta från höften. Dock blir infästningarna justerbara, så det är enkelt att korrigera detta i framtiden.
Ovan: Vänstra bilden visar 20mm utfjädring (acceleration) och högra 20mm infjädring (inbromsning)
Nedan: Vänstra bilden visar 20mm utfjädring tillsammans med 2º krängning. Högra visar 20mm infjädring och 2º krängning.
Den stora utmaningen var egentligen att få till en modell/skiss som rör sig korrekt vid krängning i datorn. Rör modellen sig fel blir ju allting fel…
Övre bärarmen
Efter att lokaliseringen av under länkarmen bestämts, var det dags att försöka hitta lämplig plats på den övre länkarmen. För att slippa kapa i rambenen, måste länkarmen hamna ovanför rambenet. Inte så konstigt kan tyckas, men spindeln blir egentligen onödigt stor i sammanhanget. Kompromisser – bilbyggandet är fullt av dem…
Ovan; Med undre kulleden bestämd i X- och Y-led, samt spindeltapslutningen bestämd var det enklare att placera övre spindelleden med tanke på att det endast kunde ske längs spindelaxellutningen. Ha i minne att länkarmarna (linjerna) bara är utkastade än så länge, så om geometrin ser knasig ut kan du tänka på att det är nästa grej att grotta ner sig i. På bilden är hjul och subframe utplacerat för att förstå de fysiska begränsningarna för hjulupphängningarna.
Tidigare har det tjatats om att bilen blir väldigt låg och att allt hamnar väldigt högt upp i karossen och det kan även tillämpas här. Notera hur högt upp den nedre länkarmen hamnar i förhållande till ramen. Det är inga frigångsproblem vid ramen, men däremot äter den friskt av utrymmet för generator, torrsumpspump, AC-kompressor (du läste rätt!) och grenrör… Lär bli utrymme för kompromissande här.
Och eftersom höjden på nedre länkarmen är spikad, kunde styrväxeln placeras ut. Istället för originalets styrsnäcka, blir det en kuggstångsstyrning istället. Som du ser på bilden, saknar den servoverkan. Istället kommer ett elektriskt servo användas. Mer om detta i en framtida uppdatering. Kuggstången hamnar i alla fall i höjd med nedre länkarmen. Ibland placeras den någonstans mellan övre och undre, men i detta fallet är det extrema utrymmesbekymmer (det är främst de nedre hästarna som är i vägen, så om motorn trimmas ner i framtiden ska jag ta bort dessa först) som gör att den måste hamna under tråget. Bonus med styrväxel monterad i samma höjd som länkarmen – blir bra kontroll över bumpsteer bland annat.
Framvagn – förstudie
Inte för att Kung Bore har ett fast grepp kring Skåne direkt, men det är ändå hög tid att sätta sig framför datorn och börja jobba med framvagnen istället för att stå ute i kylan och jobba ”på riktigt”.
Man kan tycka att det hade varit läge att bygga en helt ny framvagn, från scratch, eftersom den befintliga i folkmun benämns som ”kass”. Med kass menas att den snarare påminner om en blöd handduk i vridstyvhet än en framvagn. Egen framvagn hade såklart kunnat konstrueras och extraarbetet hade varit minimalt jämfört med en version som är baserad på originalramen. Dock handlar det igen om kompromisser – för att bilen skall kunna registreras som ombyggt fordon, måste delar av originalkonstruktionen finnas kvar. Det innebär alltså att man får göra det bästa av den befintliga situationen.
Ovan; Originalsubframen då alltså… Mätning pågår för fullt. Det visade sig vara svårare än jag räknade med att uppskatta utrymme för motor och andra komponenter som sitter mellan rambenen.
Ovan vänster; Sista bilden på subframen i nuvarande tappning monterad mot karossen. Även torrsumpstanken skymtar på bilden. Höger; Eftersom bilen kommer bli låg och där original finns ca 25mm luft mellan kaross och subframe var dessa millimetrar väldigt mycket värda. Därför studerades det noga hur nära subframen egentligen kunde komma karossen – varenda millimeter som sparades har man igen i intjänad markfrigång… Efter noggrannt måttande kunde det konstateras att med viss urkapning (skall svetsas ihop senare) gick faktiskt ramen att montera kloss intill karossen.
Nedan; Ramen monterad mot karossen. Tittar man noga, ser man urkapningen i rambenet. Eftersom profilerna fortfarande är ganska höga, blir det tyvärr 10mm nedhäng av subframen under den beräknade markfrigången (90mm). Det gör i och för sig ingenting – där finns som sagt mycket att ta på, och det kan ju vara smidigt att ha has-skydd om underredet skulle ta i någon vägbula, curbs eller liknande i framtiden…
Nedan; När tillräckliga mått hade tagits, värmdes CAD-burken upp och ramprofilerna ritades upp. Axeln i mitten är vevaxlens position i förhållande till framvagnen, vilket kommer bli viktigt senare. Det som syns på bilden är det som kommer sparas av den befintliga framvagnen. Kommande ram kommer kommer mer efterlikna ett fackverk än nuvarande balkram. Originalrambalkarna blir sannolikt något överdimensionerade för ett fackverk, men som sagt – allt handlar om kompromisser.
Ovan; Med rambenen ritade, var det dags att börja titta lite på framhjulet. Här är hjulet riggat med bromsok, bromsskiva och fälg för att ta reda på minsta avståndet mellan fälg och bromsok (indirekt bromsskivan alltså). På bilden är det ca 5mm vilket bedöms vara fullt tillräckligt, även om fälgen flexar ganska mycket vid belastning. Eftersom bromsoken är monsterbreda, är det högintressant att få dem så nära fälgen som möjligt för att hålla scrubradien låg.
Nedan vänster; Efter att rambenen var ritade, var det dags att bestämma höjdläge för nedre spindelleden. Denna bör sättas så lågt som möjligt för att tillåta plats för styrväxeln, som kommer ligga i höjd med nedre länkarmsinfästning. Dock måste det fortfarande finnas plats för fjädringsrörelserna hos länkarmen. Bilden kanske är lite svårförklarande men de svarta linjerna är yttermåtten på länkarmen vid max fjädringsrörelse. 50mm kvar till fälgen känns som bra marginal.
Nedan höger; Därefter frilades fälgen, undre knuten ritades in samt spindelaxellutningen. Scrubradien blir drygt 30mm. Det hade känts bättre i sinnet om den hamnat på 10-nånting istället för 30-nånting, men det är fortfarande radikalt bättre än originalets 120mm… Viss skillnad lär det ju i alla fall bli.
Nedan; Framvagnsgeometrin är påbörjad. Höjden på övre bärarmen skall också bestämmas innan det kan börja laboreras med geometrin. Just övre bärarmen är lite problematisk eftersom fälgen och rambenet begränsar. Ramen är rätt hög och klumpig där bärarmen hamnar vilket gör det svårt att få fysiskt plats med den ovanpå rambenet.
Penske 8100; Nu i CADen
Det är klart att stötdämparna måste CADas så att de kan monteras i hjulupphängningarna. Ett förhållandevis enkelt arbete (rita av saker är alltid enklare än att konstruera eget). Efter att ha suttit med dem några kvällar, är de i alla fall klara enligt nedan. Till och med en liten fjäder fick hänga med.
Nedan; Även lite andra projekt är på gång i CAD-världen just nu. Min kollega släpade hem en den prylar från sin senaste USA-tripp, bland annat wilwood huvudbromscylindrar. Bilen kommer bli lite för tung för att köra med manuella bromsar (i alla fall på gatan) vilket gör att där krävs ett bromsservo. Dock vill jag fortfarande ha bromsvåg, så därför kommer ett sånt här arrangemang hamna framför bromsservot (själva bromsvågen saknas på bilden).
dämpade känslor – Penske 8100
För några poster sedan konstaterade jag att fördelen med långtidsprojekt är att man kan göra bra dealar på delar till projektet. Bara några dagar efter att posten skrevs, dök det upp en uppsättning Penske 8100-dämpare på en sida för begagnade raceprylar. Jag drog iväg ett mail, men hörde inte något på två veckor och glömde av dem. Två veckor senare kom dock ett svar;
Hi, they are valved for 450 pound front springs and 550 rear springs, on a 1200kg Mosler GT3 car.I’ve only had them for a couple months, I wanted to convert them to struts for a BMW project but it’s cheaper to buy Penske struts than to convert the 8100’s. Also shipping to Sweden will be £55. Email me if you want them, I just received 3 offers today.Svaret gick med vändande post och en vecka efter landade det ett stor brun pappkartong med fyra dämpare i.
Det blev alltså en uppsättning 8100:or med separat justering för kompression och retur. Dubbeljusterbara i folkmun alltså. Meningen var först att satsa på någon Öhlinsmodell men när dessa, som ligger i samma prisklass, dök upp för ca en fjärdedel av nypriset var det bara att slå till. Egentligen skulle det ju inte köpas dämpare förrän slutet av 2012 eftersom bilen först då hade haft en någorlunda korrekt totalvikt. Istället för att beställa färdigshimsade dämpare, blir det alltså till att köra en eller ett par säsonger med nuvarande setup innan de eventuellt shimsas om.
Här näst blir det till att CADa av dämparna och stoppa in dem i bakvagnen för att se hur det blir. Egentligen blev timingen ganska bra ändå, med tanke på att det är dags att konstruera framvagnen under kommande vinter. Då kan det vara bra att ha de flesta komponenterna hemma.
Att montera subframen mot karossen…
Det är för närvarande halvtid i bakvagnsbygget. Dvs prylarna sitter monterade i karossen och ”mognar” medans det kluras på infästning av stötdämpare. Eftersom det finns en del annat att pyssla med på bilen innan den blir klar (jo, tjena…) så kländes det lägligt att framvagnen påbörjats. Sannolikt kommer samma typ av konstpauser infinna sig under denna delen av konstruerande och då kan arbetet med bakvagnen återupptas…
Subframen som syns här på bild och hör till originaldelarna på bilen, har varit ute på drift i Sverige. För att göra en lång historia kort, såldes den iväg tillsammans med resterande delar av framvagnen. Eftersom jag börjat halka efter lite i tidplanen, samtidigt som SFRO var lite lätt tveksamma till att montera dit en helt egenbyggd framvagn konstaterades det att det sannolikt är snabbare och enklare att utgå från originalramen. Det visade sig att köparen egentligen inte behövde ramen utan bara var intresserad av de lösa detaljerna (han ville köpa sakerna löst egentligen, men jag ville bli av med ramen pga platsbrist). Snällt nog, fick jag tillbaka ramen när planerna för bygget ändrades. Det hade gått att bygga en egen, men gränsen mellan ombyggt och amatörbyggt fordon hade blivit hårfin och risken för personlig tolkning kändes lite för stor.
Därför föll valet på att utgå från originalsubframen.
Ovan; Det stora problemet med originalsubframen är att den hänger väldigt långt under karossen vilket påverkar markfrigången på låga bilar. Minns inte riktigt, men det handlade om ca 35mm under beräknad lägsta punkt på bygget. Vilket i sin tur hade inneburit en markfrigång på 55mm vid lägsta punkt. Nja, inte så bra.
Subframebussningarna kan kortas utan att ramen behöver genomgå några modifieringar, men för att komma åt de sista 10 millimetrarna, krävdes det lite kapande i ramen.
Ovan till vänster; En uppsättning temporära subframebussningar svarvades till för att kunna provmontera framvagnen. Därefter sattes mätningarna igång för att se var ramen behövde kapas (höger bild). Efter många dubbelmätningar (och trippelmätningar) plockades kapen fram och ett 14mm urtag gjordes i rambenen. Är man lite fiffig, kan man dessutom fälla i originalplåten i det nykapade hålet, vilket innebär att ramen inte ens är modifierad eftersom den fortfarande består av originalmaterial *host host*.
Nedan; Färdigt resultat! Ramen sitter ca 25mm högre upp mot karossen än tidigare. Nu är den bara knappa 10mm under lägsta punkt på karossen. Att ha ett par glidmedar i form av subframe som eventuellt kan skydda vid curbs eller annan närkontakt känns rätt bra. Dessutom är de oömma, och gör egentligen ingenting om de tar i någonstans.
länkarmar, bakvagn
Det är inte supertempo i garaget för närvarande av olika anledningar. Inget allvarligt, utan om ett par veckor kommer det återgå till det vanliga några-dagar-per-vecka-mecket. Tills vidare bjuds det på något som blev klart för några veckor sedan; Länkarmarna är färdiga för provmontering. De är bara punktade samman, så när väl bakvagnen demonteras igen kommer det bli många många många timmars svetsning av diverse detaljer…
Ovan: Ballisticbussningarna lär aldrig slitas ut. Någonsin. Med tanke på att de är gjorda för off-road-racing inser man snabbt när man håller dem att de är tämligen överdimensionerade för track-day-åka. Nåja, desto bättre…
Ovan; Hemmasvarvade vantstag. M20x1.5-gänga. Att notera nästa gång man gör egna nyckelfattningar på saker; Det är bra att först kolla upp vilka standardmått fasta nycklar har innan man sätter upp sina svarvade saker i fräsen. Då slipper man stå med nyckelfattning 29mm när det är 30mm som är standard… Den typen av misstag händer en gång som sagt.
Nedan; Lite svårt att få bilder på sånt här monterat, men här är i alla fall en där man kan ana de tre längsgående länkarmarna. Hade varit skönt att åtminstone få lite grundfärg på karossen snart så att den får samma färg överallt. Börjar bli rätt trött på ”flerfärgat”.
Bakvagn! Bakvagnen! Den är ihop!
Det är verkligen 100% tempo på projektet för närvarande! När ”målet” kan börja sniffas ökar viljan av att korsa mållinjen. I detta fallet är mållinjen att få in bakvagnen i bilen för att få känna känslan av att projektet går framåt. Även om det återstår mycket jobb med att prova ut plats för fjädring, karossfärstärkningar osv. så är detta ett stort framsteg för mig.
Målet var att bakaxeln skulle vara testmonterad i bilen innan den siste maj. Med andra ord är man för en gångs skull före tidplanen, något som inte händer särskilt ofta i bilbyggarkretsar…
Ovan; Fläskiga fälgar och ball hjulupphängning. Det här kan bli ungefär hur bra som helst! Tänk om man hade kunnat köpa det här som byggsats istället! Vad najs det hade varit! Många timmar har lagts ned på svarvning, fräsning, kapning,, ritande, svetsning, räknande, konstruerande, funderande osv innan dags datum. Notera även mina billet MDF-bärarmar. Tack vare träets fjädrande egenskaper behöver man inte gummibussningar, utan kan klara sig med solida bärarmar. MDFen måste dock fuktskyddas för att klara av att köras i regn. Jo men visst…
Ovan; 34 svarvade detaljer, 2,4 meter svets (när den väl är helsvetsad), okänt antal kapningar, några kvadratmeter plåt och några hundra timmars nagelfarande i CADen så blev det till slut en bakvagn. Här syns även bromsokshållarna (tandpetarna ovanför hjulnaven).
Ovan; Med 295x30x18″ så ser det rätt kaxigt ut faktiskt. Den totala vikten på delarna som syns på bilden ligger bara några kilo över en tom 10-bultad originalbakaxel – med andra ord har tämligen många kilo sparats in på bakvagnen. Exakt hur mycket kommer bli väldigt intressant att se, men det rör sig om mer än 50 kg ofjädrad vikt som har bantats bort.
Ovan; Kan man inte ha en genomskinlig kaross så att konstruktionsporr av den här kalibern kan visas för omvärlden på ett enkelt sätt? Bakaxeln är nästan lite för mumsigt för att gömmas undan under en gammal 70-talskaross…
Så, då var det dags att montera den i bilen. Men vi kan väl dra ut på spänningen ytterligare några dagar, va?
Centrummutteraxlar
Redan i förra uppdateringen kunde navet provmonterat på fälgen skådas. Det innebär såklart att centrummutteraxlarna bak redan var klara då – dock måste man ju spara lite på godiset och fördela det jämnt till läsarna, haha.
Anyway – centrummutteraxlarna har varit tämligen pilliga att tillverka – svarvning, gängning, svarvning igen, fräsning, fräsning på rundmatningsbord osv. De har varit på gång ”till och från” under flera månader. Men till sist blev resultatet riktigt bra!
Ovan; Vi får väl börja med det färdiga resultatet. Här är centrummutteraxel och låsning för den samt nav på bilden. Centrummutteraxeln skruvas direkt på drivaxeln istället för den vanliga muttern. Därefter träs en låsning över axeln som fixerar den i förhållande till navet. På så sätt riskerar inte axeln att gängas upp. Därefter träs en centreringsbricka över (eftersom Porschefälgarna har större centreringshål än lincoln) och till slut låses allt axiellt med en segersäkring. Centreringsbrickan och segersäkringen finns på bild längre ner.
Ovan; Centrummutteraxeln. Total vikt 336 gram/st, gjorda av Impax Supreme. M40x3-gänga. På högra bilden skymtar även ett ämne till de främre axlarna.
Ovan; En lite mer förklarande bild. Det vänstra patentmecket föreställer drivaxlen, därefter kommer navet (saknas på bilden), en bricka, centrummutteraxel, låsning (mellan axel och navet), centreringsring och till slut segersäkring. Normalt brukar folk tillverka en riktigt tjock spacer och sen gänga ett rör i denna för att på så sätt få en centrummutterlösning. Problemet är att det bygger väldigt mycket utåt, scrubmåttet ändras och hjullagren slits i onödan. Min lösning är något mer komplex och kräver lite mer pillande, men i slutändan blir det riktigt, riktigt bra.
Ovan; Färdigmonterat! Eftersom styrpegsen inte är tillverkade än (har du en styrd svarv, så kan du väldigt gärna få hjälpa mig!) fick det duga med en uppsättning gamla originalskruvar istället.
Sådärja! Nu är det faktiskt klart för provmontering av bakvagnen i bilen! Mycket jobb återstår ju såklart innan den kan kallas ”färdig”, men det är såklart bra att provmontera innan den är helt färdig. Då svider det inte lika mycket om något skulle visa sig vara fel…
hjulnav
Med bakaxeln färdig för provmontering, hamnade fokus istället på kringdetaljer som måste vara klara inför testmonteringen. De detaljerna som kommer från Lincoln Mark VIII i bakvagnen är inte riktigt anpassade för Pontiacens behov, så därför är viss modifiering nödvändig. Naven är tex gjorda för bultmönster 5×108 och inte 5×130 som BBS-fälgarna kräver. Såklart fanns det inte tillräckligt med material på flänsen för att borra om bultmönstret utan operationen blev större än vad det var tänkt från början. Som vanligt.
Ovan: Här är patienten, ett nav från Lincoln Mark VIII, som kanske har sett sina bästa dagar vad gäller puts – ingenting som inte ska gå att ordna…
Ovan; Eftersom navet är för litet för att borras om till 5×130, svarvades en ring som pressades utanpå för att på så sätt få en tillräckligt stor fläns. Navet kyldes därefter ned till -40°C och ringen värmdes till 250°C. Därefter bar det snabbt av mot pressen…
Nedan; …där delarna sedan pressades ihop med varandra. Sen fick det svalna. Resultatet syns på högra bilden nedan.
Nedan; Därefter svarvades navet både på fram och baksida.
Nedan; Efter en stund i fräsen finns det numera både GM 5×120.65 (som även får fungera för BMW…) och Porsche 5×130 i naven. Det går dessutom både att köra centrummutter eller traditionellt fembult, så fälgmöjligheterna känns ganska framtidssäkra….
Nedan: Naven fick en omgång plasticote gjutjärnsgråa värmetåliga färg på sig för att behålla en någorlunda finish även om några år (dvs när bilen börjar bli körbar…).
Ovan: Woho!!! Titta, det passar! Titta titta!!! provmonterat för första gången! Härlig känsla att faktiskt börja montera saker, istället för att demontera hela tiden!
Nedan; Spindlarna glasblästrades för att passa in i resten av nybilsfinishen som komma ska. Den tillhöger är inte blästrad…
Nedan; Därefter svarvades bussningar som pressades i de nedre bussningshålen samt bromskylningen tillverkades också. Blank plåt är perfekt när det handlar om värmereflekterande prylar – sån tur att det låg lite spillplåt i en hörna på jobbet då…
Nedan: Bonusbild. Nu ska nytt hjullager monteras och därefter åker navet i.
bakaxel nästan färdig… som vanligt.
Det här med hemmapulade saker tar sin lilla tid. Så här när bakaxeln börjar närma sig färdig hade det varit ganska intressant att veta hur lång tid den faktiskt har tagit att sammanställa. Alla svarvade detaljer, alla konstiga rörkapningar, alla dubbelmätningar innan kapning osv. En sak är klar dock – jag har sparat åtskilliga timmar på att få laserskuren plåt levererad. Det är lätt att inse de gångerna då någon enstaka plåt har behövt tillverkas. Därför vill jag rikta ett extra tack till Mats och Henrik som har ställt upp med plåtleveranser i tid och otid.
Nåväl; Bakaxeln är sammanpunktad! Äntligen! På bilden nedan sitter visserligen tvärsträvorna med maskeringstejp, men även dessa punktades fast strax efter att bilden togs. Tredje länkinfästningen skall också stagas upp lite mer än vad bilden visar.
Ovan: Några extra bilder på bakaxeln
Nedan: Där finns en hel del knasiga rörkapningar i konstruktionerna. Särskilt där rören möter två ytor eller fler. Eftersom det tar en evinnerlig tid att sätta upp rören i fräsen, kapa med hålsåg en, eller två gånger skrivs istället omkretsen ut på ett papper som därefter hålls runt röret och ritas av. Därefter är det inga problem att kapa röret med vikelslipen och jämna till det i bänkslipen. 1 minut totalt, jämfört med 15-20 minuter i fräsen…
Nedan: Spindelhållarna till bakaxeln, som är lösa för att kunna shimsas till rätt toe, är också klara. Här är ju inte mycket att testmontera, utan de helsvetsades med en gång.
Nu är det lite modifieringar på naven och färdigställande av centrummutterlösningen som väntar innan hjulen kan monteras och bakaxeln kan skruvas dit. Kul!
Rörkapning
De som är flitiga läsare här, kommer säkert ihåg att bakaxelkonstruerandet började med att hitta lämpligt material?
Eftersom jag bara har en rörstump gällde det att ha tungan rätt i munnen när det var dags att sätta kapen i det. Efter ett par hundra överdrivna dubbelkollar mot CADen hamnade så röret äntligen i sågen för kapning.
Ovan till höger: Eftersom röret skulle snedkapas i båda ändarna och kapningarna skulle vara parallella med varandra behövdes det ett referensplan för att mäta in det i sågen. Referensplan är ju lite svårt på runda tingestar, men ibland är det svåra enkelt – loppa dit en fyrkantsprofil innan kapning och placera den med lämplig vinkel i sågen så blir båda sidorna parallella!
Ovan: Tadaaah! 4º snedkapat i båda ändarna, redo för att monteras i fixturen.
Nedan: och då blir det så här fint! Nu börjar man snart kunna gissa att det ska bli en bakaxel…
Ovan: Mmmmmm, härlig kick när man monterar rören i fixturen och det bara passar direkt… CAD är Guds gåva till… typ hela mänskligheten! Röret har 4mm gods, så självklart fasades kanterna inför svetsningen…
Nedan: Fin passform ute i kanterna också.
Härnäst blir det till att punkta samman bakaxeln och släpa ut den till bilen för att kontrollera att verkligen allt passar som det ska.
Bakaxelfixtur
Det är effektiva dagar i verkstaden just nu. Inför att bakaxeln ska svetsas ihop måste den fixeras. Annars slutar det sannolikt med att den kommer se ut som en banan.
Tyvärr har jag inte riktigt resurserna att CNC-fräsa den där billet-alufixturen utan får nöja mig med betydligt mindre exklusiva material än så. MDF är tex.ett alldeles utmärkt material att bygga med. Sagt och gjort fick Bauhaus såga upp 25mm MDF-plattor i lämpliga storlekar som sedan borrades i fräsen för att hålen skulle hamna så exakt som möjligt. Man kan ju tycka att en fixtur i trä borde gå ganska snabbt att slänga ihop. Det gör det inte – det tar flera efter-jobbet-vardagskvällar innan det blir klart. Dessutom hamnar hålen spegelvänt mot vad man tänkte att de skulle göra… Oftast är det fräsens fel, inte han som styr den…
Men efter en veckas flitigt jobbande är den numera klar.
Ovan: För att få hålen så rätt som möjligt i förhållande till varandra, borrades dessa i fräsen. Lite pilligt när träskivan är större än fräsbordet…
Nedan: Och såklart CAD-referensen så att man ser vad det ska bli i slutändan.
Nedan: Här är dedion-fötterna, som jag kallar dem, monterade i fixturen.
Nedan: Tadaaah! Färdigt. Nästan i alla fall. Lite stagning mellan ändarna återstår för att få den tillräckligt styv inför svetsning. Som sagt, lätt som en plätt att bygga fixtur…
Så, då var det dags att kapa röret i lagom stora bitar då… Något jag dragit mig för ganska länge eftersom det blir väldigt dyrt att köpa ett nytt om jag skulle göra fel. Vid närmare eftertanke går det att dra ut på det någon vecka till… Eller månad.
En pall kommer lastad….
…Med vad då?
Ovan: Med bakaxelplåt såklart!
Det finns vänliga människor, och sen finns det ännu vänligare människor. Mats på Habo Rostfria och Henrik på en annan firma (hans chef kanske läser här… Haha!) har varit mycket hjälpsamma och försett mig med plåt baserat på mina CADunderlag. Jag slipper med andra ord att stå med vinkelslipen och karva ut detaljerna. Istället kan jag genast börja pussla ihop delarna med varandra (den skarpsynte ser att jag redan tjuvstartat när denna bilden togs).
Nedan: Här är ändarna på dedionen. Inte så mycket att säga om det hela mer än att det är kul att leka med TIG:en när det är så bra passform på delarna. CADbilderna längst nere är bara som referens. Prylarna ser som sagt ut lite mer kompletta i verkligheten eftersom jag inte orkade rita de enklaste plåtarna i CADen.
Det mesta arbetet sker just nu framför datorn och svarven/fräsen. Karossen får vänta på bättre tider, men lite småsaker som är relaterade till bakvagnen sker dock fortfarande.
Nedan: Diffen monterad i karossen för att prova ut lite olika upphängningar av bakre infästningspunkten. Som synes är det ganska ont om plats. Desto bättre att börja med pappmallar innan detaljerna tillverkas…
Bakvagnsbussningar
Eftersom jag har fått rätt mycket frågor om mina bakvagnsbussningar kommer här lite bättre information. Bussningen tillverkas av Ballistic Fabrication och är egentligen menad som universiell off-roadbussning, vilket gör att den utan några större ansträngningar sannolikt kommer orka med livet i Pontiacen…
Ovan: Hårda bussningar har såklart stenhård logo. Ballistic Fabrications versioner är inget undantag…
Användandet av uniballs i bilen undviks i största möjliga mån. Det är en gatbil och då skall lederna vara robustare än race-avsedda uni-balls. Till bakvagnen föll valet på eftermarknadsprylar till off-roadbilar från staterna. Det finns liknande uni-ballsinspirerade bussningar till originalbilar också – Mercedes, Alfa Romeo och BMW har typen av stålkula som är lagrad i plast och vars karaktär påminner om uni-balls. Dock verkar de ha relativt liten vinkelrörlighet jämfört med uni-ballsditot.
Bussningen isärplockad. Smörjnippeln och justerringen gör att dessa sannolikt kommer hålla hela bilens liv…
Bussningarna från Ballistic Fabrication är förvisso ganska stora (ytterdiametern på hylsan är 65mm) och klumpiga, men det mesta är stort på bilen så i detta fall var det ingen fara. Dessutom hanterar en stor bussning kraften bättre internt, vilket gör att den håller längre.
Ovan: Eftersom stagen behöver vara justerbara, tillkom det en M20x1.5 gänga i änden.
Nedan: Resultat, samt hur bussningen ser ut när den är monterad. Någon form av tätning till sidorna behövs också, men det löser sig nog med tiden.