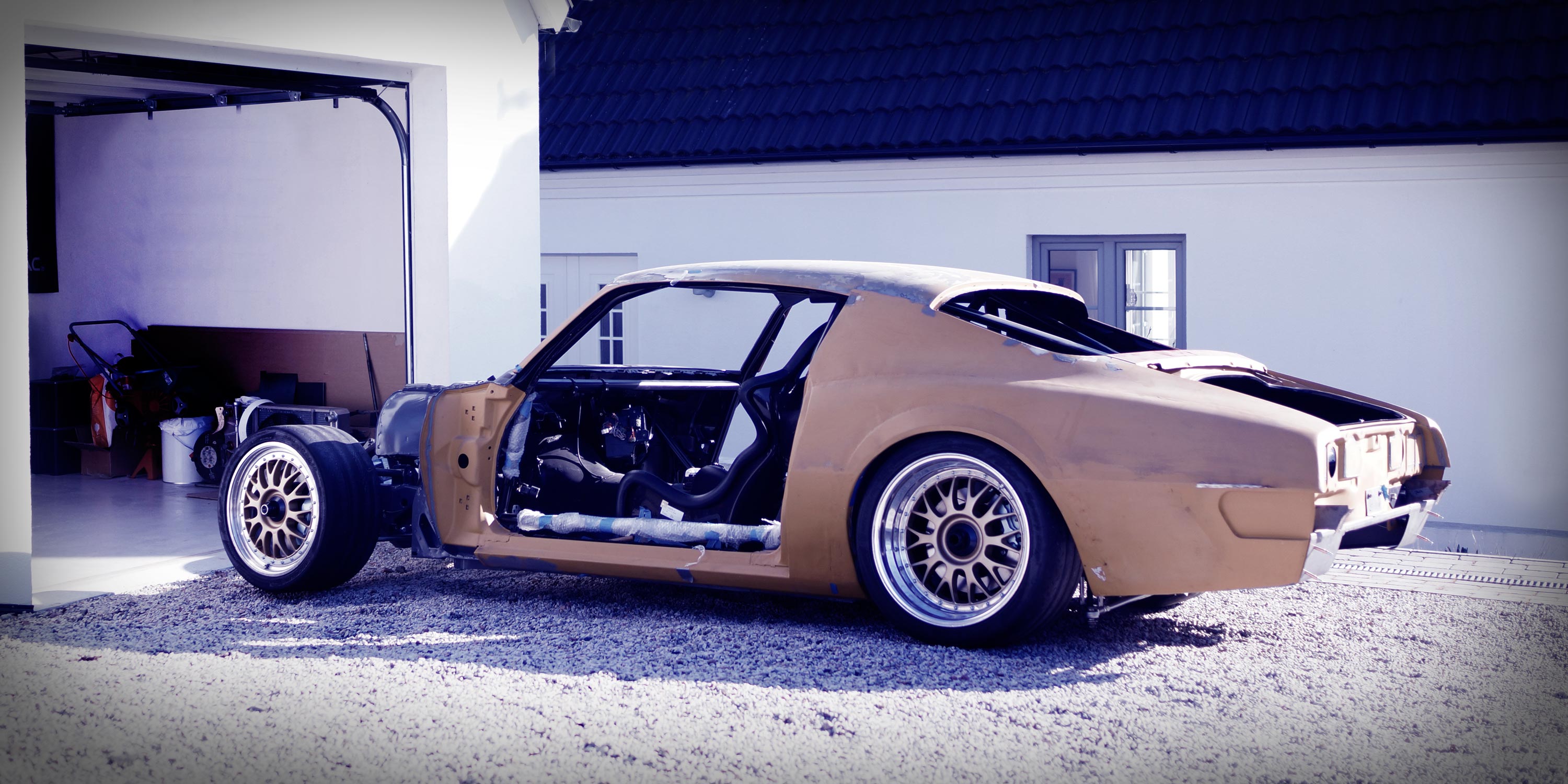
Kategori: Suspension
Bromsar bak
När det kom till bromsar bak gällde det att hitta något som matchade frambromsarna vad gäller kolvarea. Mestadels av lasten läggs på frambromsarna under retardation, Därför är inte styvhet riktigt lika viktig bak som på fram. Det tänkte jag inte på när jag handlade, utan kan snarast klassas som en efterhandskonstruering för att framhäva hur genomtänkt och perfekt det här projektet är…
Bakre oken var nämligen väldigt små (fysiskt) jämfört med framoken, som är gigantiska. Dock är undertecknad övertygad om att de kommer fylla uppgiften väldigt bra.
Ovan; Wilwood IR-GT4R. Rätt kolvdiameter, låg vikt och klarar nog jobbet som bakbromsar bra. 4-kolvsok har ju så klart inte någon P-broms… och det tycker ju SFRO är rätt bra att ha. Med andra ord köptes en uppsättning p-bromsok. Även dessa tillverkade av Wilwood. Sannolikt utvecklade av någon ingenjör som var trött på sitt jobb. Antagligen är det en cheddarluktande, engineer-Bob som tyckte det var viktigare att komma hem till grillen och dricka Bud än att göra bra produkter. Därefter har gissningsvis gjutverktyg varsamt tagits fram av slarviga små barnfingrar fem mil utanför en stad som inte Uppdrag Granskning känner till i Bolivia och till sist har en oförstående marknadsavdelning börjat sälja produkten utan att ens titta på den. Med andra ord som vilken vanlig manick ”made in the USA” som helst…
Nedan; Oken har fått en spacer monterad för att kunna greppa över de breda bromsskivorna. Eftersom det inte finns någon vettig infästning på dem har glidpinnar konstruerats. (många väljer att istället att montera oken stumt i en tunn plåt och sen montera denna i spindeln och låta plåten göra arbetet – jag måste ju så klart gå min egen väg och uppfinna hjulet på nytt istället… Hur var det nu med svenska, smörgåsbordsätande midsommarstångsdansande ingenjörer? De kanske inte är så mycket bättre än Budweiserdrickande jänkediton?)
Ovan; Ganska mycket TV-kocksvarning i dessa uppdateringar eftersom det aldrig visas någon action utan bara resultat, men så här blev det. Liten temperaturdekal på oket också för att kunna ha lite koll på värme… Temperaturskalan börjar på 100 grader, så svårt att ha dem som termometer på garagetemperaturen men förhoppningsvis kommer väl bilen ner från pallbockarna innan OPEC slutar sälja olja.
Nedan; I fantastisk kvalitetsanda visade sig hårdvaran till de fantastiska P-bromsoken kom så klart obehandlad i vanligt svartstål. De Aluzink-behandlades för att hålla lite längre än bara första provturen. Högra bilden visar bromsoksadaptern, en av få CNC-frästa detaljer i projektet. Även pegs och pinnbultar till bromsoket är CNC-svarvade, signerade ”Joakim”. Tack för hjälpen!
Wilwood förtjänar inte på något sätt ett dåligt rykte pga p-bromsarna. De är imponerande slarvigt tillverkade när man jämför dem med deras andra keramiskt coatade, unobtanium CNC-billettjohejsan megabromsok. Som med allt annat får man vad man betalar för och för 400:-/st kan man nog inte begära mycket mer. Framoken har ett listpris på 2800 dollar/st och P-bromsoken 99 dollar/paret som jämförelse…
Skulle det visa sig att de inte fungerar, finns det många standardbilar som använder liknande P-bromsok, Audi R8 tex. Prislappen är så klart inte 400:- (och vikten är betydligt högre…), så Wilwoodoken får bekänna färg först…
Ovan; Audi R8-ok (höger) samt Brembo eftermarknadsok (vänster).
Bromsar fram
Tidigare i våras skruvades bromsoken fast på spindlarna. Känslan av att skruva fast dem för första gången och det sitter perfekt centrerat och allt passar utan en enda provmontering tidigare – när man har byggt alla detaljer runtomkring själv är… obeskrivlig. Det är inte för att låta dryg som det tjatas om detta hela tiden, men det är en enorm kick att konstruera saker och sen få kvittot genom att det blir exakt så som man tänkte sig. (undrar om man får äta upp det där citatet efter första provkörningen?)
Bromsslangar krävde dock en hel del funderande för att få rätt på. Dels skulle längden bestämmas, sen kan inte slangen vridas, utan bara böjas vilket också ställde till en del. En del klurande i att få sånt att löpa fint.
Bromsarna förresten. Wilwood P6R (även kallade Prolite på vissa ställen). Magnesium/aluminiumhus med keramiskt coatade kolvar (för att inte överföra värme från beläggen) samt polerade, rostfria plåtar inuti tråget för att reflektera bort strålningsvärmen. Mums.
Ovan; För att inte slangen skulle ta emot någonstans och för att inte utsätta den för konstiga vridningar fick det experimenteras en hel del. Det slutade med att en position hittades där slangen behövde fixeras vid spindeln för att röra sig rätt. Med lite enkel hårdvara löstes problemet…
Nedan; Buntbandet på bilden ovan utbytt mot plåt och gummiklämma. När beläggen hamnar i oket, då känns det nästan på riktigt!
Ovan; På plats, äntligen. Bara att trampa på pedalen nu med andra ord.
Bromsar, renovering
Det här var ju (från början) ett budgetprojekt. Det är fortfarande ett budgetprojekt i form av att det går mycket arbetstid istället för pengar för att lösa problem.
Budgeten innebar att det var bara och glömma att köpa nya flashiga AP-ok, Brembo eller liknande. Och sexkolvsok måste det ju vara för det är ju… coolt.
E-bay dammsögs efter möjliga kandidater långt innan projektet egentligen påbörjades och ett par rejäla hejdare lyckades ropas hem för ett blygsamt kostnad. Som vanligt med begagnade prylar är det alltid bra att börja med att renovera dem, så slipper man strul senare längs resan. Bromsoken var inget undantag – nya O-ringar, ny ytbehandlning på alla fästelement, polering av värmeplåtarna och lite ny färg lyfte oken till nyskick.
Lekte även med tanken på att fräsa in PONTIAC på oken, men det föll på att det inte fanns någon gratis-tid i en CNC fräs någonstans. Budgetprojekt, remember?…
Ovan; När väl oken kom hem från staterna visade de sig vara betydligt större än förväntat. På den högra bilden står ett A4-kuvert i oket som en storleksreferens. I välkänt Wilwood-manér, har den svarta ytbehandlningen övergått till en lila-violett färg. Inte så lockande, så…
Nedan; …därför togs beslut att måla om dem. Plasti-Cote motorgrund och därefter Pontiacs motorblåa nyans som en liten hyllning till företagets glansdagar. Även fästelementen fick ny svartoxid då den gamla var rätt rostig på sina ställen.
Nedan; Antingen besitter undertecknad små nätta frökenfingrar, eller så har bromsoken kapacitet att stoppa vilket lok som helst. Det sistnämna stämmer bättre. Som synes på handleden är de inte fjäderlätta, men strax under 4kg/st får anses vara ok för ett så stort ok.
Styrarmar
Det var meningen att styrarmarna skulle CNC-fräsas. Egentligen inte ett behov, men för att få lite snygg rund radie på ytterkanten så hade det varit smidigt. Tyvärr visade det sig bli alldeles för dyrt att leja bort fräsningen, så istället kläcktes den eminenta idén att laserskära ytterprofilen och därefter bara borra hålen i fräsen. Det visade sig vara en ganska bra idé – ofta är det planing och fräsning av konturer som tar längst tid i en manuell fräs. Att ”bara” borra lite hål med rätta kordinater går ganska fort.
Ovan: Godis. Ny leverans med delar från… Lasermannen! Nya vipparmar, förstärkningar till övre länkarmar, nya infästningar till coilovers i subframen med ett hål till på höjden och sist men inte minst råämnen till styrarmarna (till höger).
Nedan; Lite planing och några hål senare så gick de från stålbitar till styrarmar.
Nedan; Färdiga. 1:10-kona för volvo styrled. Tre hål för att enkelt kunna exprimentera med styrutslag och antal rattvarv.
Ovan och nedan; Slutgiltigt resultat blev bra! Monterad på spindeln, passar som handen i handsken. Styrleden tar inte emot bromsskivan när den sitter i innersta hålet, och det tiden kommer det komma en värmeplåt mellan spindel och skiva som skyddar gummimembranet på leden. Styrväxeln har kortats ca 20cm vilket gjorde att stagen till spindlarna behövde förlängas. Därför har de kompletterats med en skarvmutter (M14 skarvmutter fanns inte som standard, så det blev att svarva en egen…) och en förlängare.
Pga styrväxelns placering blir Ackermann (vinkelskillnad mellan ytter- och innerhjul då dessa har olika svängradie vid stora utslag) ganska lidande. Den blir något bättre när spindelleden flyttas ut till yttersta läget, men är fortfarande inte imponerande. SFRO brukar tycka Ackermann är ganska viktigt, men i mina ögon är det något man behöver när man ska navigera på parkeringsplatser. Enda gången man har väldigt stora rattutslag är i låg fart, övrig tid använder man sällan mycket mer än 10-15° utslag. Får se vad SFRO säger den dagen det blir dags.
Det går att få mer Ackermann genom att tex flytta styrväxeln bakåt. Problemet är ju bara att där finns infästningar för länkarmar. Man kan tänka sig att vända på infästningen på spindeln och lägga styrväxeln ovanför, men där finns ett oljetråg… Kompromisser kompromisser… 😉
Framvagn
Fortfarande jobb kvar, men det är lättare att hitta motivation när det börjar se ut som en bil. Övre och undre länkarmar på plats, push-rods fixade, spindlar monterade och bromsskivorna hänger på mest för att…
Kvar att fixa är bland annat styrarmar på spindlarna, länkaren till styrväxeln, lite shims för att ställa hjulvinklar och annat. Sakerna kvar att fixa är nästan räknade på två händer, vilket innebär att det inte borde ta allt för lång tid.
Kan du som läser här laserskära aluminium, så hör gärna av dig med en kommentar till inlägget.
Ovan; Pushrods (även om vipparmarnas geometri skall göras om), länkarmar, spindlar och styrning på plats. Länkhuvuden kommer få gummiballonger som skydd senare. Även torrsumpstanken till motorn har hittat dit.
Nedan; 18×10″ fälgar, med 285×30-däck. Röret i längst fram är tänkt att bli framtida krängningshämmare. Så fort det finns en närmare viktuppskattning på bilen, kan fjäderkonstanter och krängningshämmarkonstanter börjar räknas ut och därmed knivar dimensioneras. Tills vidare är det bara ett rör med andra ord.
Nedan; En liten avslutande bild som jämförelse i CADen och i verkligheten. Äntligen börjar det se ut som en bil!
Dedion & CAD
Lite försenad uppdatering denna veckan, men här är ett par bilder, varav den ena känns igen från Speedhunter-reportaget.
Ovan: Lite uppdateringar på dedionaxeln är projekt så fort framvagnen blivit färdig. Några mindre justeringar. Som syns, behövde panhardstaget bland annat monteras längre ut på bakaxelröret än vad som var tänkt från början. Lite omsvetsning med andra ord – kanske fanns en anledning till att den bara grundades innan…
Sen är jag lite kluven till om 40x20x2 röret räcker som panhardstag. Egentligen hade det varit bättre med ett runt rör, tex 30×3 det inte finns några moment på axeln, utan bara tryck och dragkrafter
Pushrods
Pushrods på plats! Länkhuvuden blev Mecmove MTE. Helt sinnessjukt dyra, men det verkar vara det enda som håller år ut och år in. Självklart skall de få ballonger för tätningen runt sig också.
Ovan: Mmmm, nu börjar det ju faktiskt se ut som en bil! Allting sitter ihop nu. Väntar på en ny uppsättning vipparmar dock då geometrin behöver finjusteras något för frigång.
Nedan; Som grädden på moset svarvades egna distanser för länkhuvuden. Övervägde att köpa, men de hade ändå behövt stickas av i svarven och då är det lika enkelt att göra egna. 28st blev det totalt. Tog ett antal timmar att göra klart… Rostfritt blev det, även om det är ett material som egentligen hör bättre hemma på båtar…
Ovan; Hyfsad skärpa i bilden förresten… Klicka upp den i stor version och zooma in länkhuvudet. Nu ser man inte det riktigt i internet-versionen men i originalbilden ser man spegelbilden av kameran i kulan till länkhuvudet!
Spindel
Det börjar verkligen ta sig nu. Spindlar på plats, centrummutterinfästningen är färdigkonstruerad. Bromsadapter på plats och egentligen bara lite småfix kvar innan bromsoket kan sättas på plats. Börjar se rätt bra ut i alla fall!
Ovan; Lättade skruvskallar till spindeln. Även passkruvar och skruvskallar till länkarm/pushrods skall bantas. Skruvarna till okadaptern måste försänkas pga platsbrist. Går och drar mig lite för att göra det tills jag är 100% säker på att de verkligen måste försänkas…
Övre länkarmar
Precis som nedre länkarmen, fick även övre (såklart) byggas från scratch. Det är mer pill än vad man tror, men slutresultatet blir bra.
- Kapa upp material och notcha rören
- Svarva hylsor till bussningarna
- svarva axlar till bussningarna eftersom original var för korta för min applikation
- plåtar till infästning för spindelled
- Inpassning mellan rör och plåt vid spindelled
- I med det i en fixtur och sätt några svetsloppor
- Ur med det ur fixturen och provmontera på bilen
- Testa alla maxlägen för att kontrollera att inget tar i
- I med det i fixturen och helsvetsa allting
Som sagt, det blir många timmar… Bra med stabil fixtur inför framtida reservdelar dock.
Nedan; Monterat på bilen. Det blir bara punktat tills att måtten kontrollerats och allt stämmer. Lite förstärkningar är kvar att fixa på armarna, men det blir som sagt vid slutgiltig svetsning…
PLÖTSLIGT är framvagnen nästan komplett! Spindeln sitter där och egentligen saknas bara pushrod och lite finlir med lagringen av vipparmen innan framhjulen kan hängas på för första gången!
Spindelmontering
Delarna börjar hitta ihop nu. Det är en fröjd att kunna skruva i vit labbrock och med nymanikerade naglar.
Bromsar får bli i vinter, när det är för kallt att stå ute i garaget. Kvar är att införskaffa skruvar i korrekta längder. Som det nu är, är det lite temporärt monterat med det som fanns i lådorna.
Mycket egentillverkat på bilden blir det… Spindel, bromsoksinfästning, spacer, pegs och så själva spindeln. Typ allt utom hjullagret med andra ord.
Styrning pt. 2
Alla har känt känslan. Först tänker man ”ja, men det här var visst lite krångligare än jag trodde”, fortfarande entuisastisk. ”Men det ska nog gå bra”. Delar fortsätter trilskas – kanske en felkapning som gör att man måste kasta detaljen och börja om, kanske hade man gjort fel redan i ritunderlaget. Irritationen stiger något och plötsligt är det mindre kul. Plötsligt råkar man ha sönder något som man inte ens planerade att röra vid. Dra en skruv snett i en gänga, råka repa en lackerad detalj, tappa något på golvet så att det går sönder etc.
Vid det här laget lägger den vettige och resonlige människan ner arbetet, rycker på axlarna och konstaterar att det är bättre att fortsätta imorgon. Bilentusiaster tillhör knappast den kategorin. Istället höjs irritationsribban och ett hat mot det man håller på med börjar utvecklas. Inget är kul, skiten ska bara bli klar. Radiojäveln är plötsligt irriterande hög (vem fan slog på den egentligen??!!!), verktygshelvetet som man höll i handfanskapet alldeles nyss är borta och vägrar visa sig. Såklart har man inget ersättningsverktyg heller och plötsligt finner man sig själv planlöst irra runt i garaget, letandes efter verktygshelvetet. ”Var i jävla helvete har jag lagt skiten!?” Det är nu man är nära bristningsgränsen. Nya svordomar skapas – svordomar som mänskligheten aldrig ens hört och som knappast får spridas utanför garaget. Ett oväntat besök från någon i garaget kan få sig en rejäl utskällning, ett klämt finger under något meck kan få liknande konsekvenser massakern på Himmelska Fridens Torg. Motgångarna fortsätter och man skriker svordomar omkring sig – en till motgång och projektethelvetesjävlaskitbilen kapas ner och åker till återvinningen. fy FAN!
Men sen plötsligt faller sista biten på plats, och det man trodde var en felkapning visade sig inte alls vara en felkapning utan blev istället riktigt bra. Slutresultatet fungerar som det ska, ja kanske till och med lite bättre. Genast är den där repan i den lackerade detaljen inte särskilt farlig längre, den skadade gängan kunde visst räddas med gängtappen och blåmärket är ju inte hela världen – sånt som händer.
Det är då man känner den. Segerns sötma. Pundarruset. Kicken av att delarna sitter på plats som de ska och att resultatet blev precis så som man fantiserade om. Genast är ryggen rakare, språket vårdat och egot växer till nya oanade höjder…
…tills nästa gång det är dags att platsbygga något i ett trångt utrymme.
Ovan; Länkage mellan rattstång och styrväxel är på plats. Det var betydligt pilligare än jag trodde, men fasiken vad bra det blev.
Nedan; Grundtanken var först att sätta kullagret (på bilden) direkt i torpeden. Men vinkeln på stången visade sig vara förstor, varför en infästning fick konstrueras. Även på ramen skruvades ett fäste istället för att tex vrida länkhuvudet 90 grader och sätta det rakt in i ramen. Det blir svårt att komma åt med så stora nyckelvidder som länkhuvudet har när väl motorn sitter på plats.
Nedan; Dragningen har gjorts så tight som möjligt mot ramen för att maximera platsen för grenrör senare.
Styrning pt.1
Pilligt det här med styrningen… Först skall styrväxeln specialbyggas. Sen specialfästen för rattstången. Därefter special-elstyrsystem för rattstången och nu är det dags för länkaget mellan rattstången och styrväxeln. Special, så klart.
Eftersom torpedvägg och subframe redan är målade, tog det ”lite” längre tid än det hade behövt.
Ovan: Originalled från styrväxeln (för att få korrekta splines). DD-stång visade sig passa perfekt i andra änden av originalleden (ibland ska man ha tur!). Genomföring till torpedväggen, länkhuvud och totalt två vinklar till. En till styrväxeln och en mitt på stången.
Nedan: Lite tråkigt att börja med sånt här när delarna är lackade, men det går om man är försiktig. Mycket tejp blir det. Riktningen på axeln uppskattades med hjälp av ett bågfilsblad. Högra bilden visar originalaxeln. Karossen är som gjord för denna – det blir helt perfekt med denna länken på insidan då rattstången plötsligt blir oberoende av hur rattaxeln skall sitta.
Nedan; För att vinna plats till grenrör och motor, dras styraxeln så nära ramen som möjligt.
En del kvar med andra ord. Blir fortsättning följer på detta…
Coil Overs
Egentligen inget kritiskt i tidplanen, men en riktigt fin motivationsboost – att få se stötdämparna sittandes på framvagnen. Dämparna är shimsade för en Lister Storm GT (1200kg, 52% bak 48% fram, liknande motion ratio på hjulrörelserna dock inte dedion utan individuell bakvagn). Planen var att köpa sprillans nya dämpare och få dessa shimsade exakt utefter Pontiacens vikt och geometrier. Det föll dock när dessa dök upp, oanvända, för en fjärdedel av nypriset. Det finns pengar kvar i budgeten att utveckla dämparna och ändå hamna under nypris…
Nedan: 30mm stålaxel och en mässinsbussning är tänkt som lager till vipparmen. Skulle detta inte fungera blir det till att testa en mjukare plastbussning eller rullager. Den tiden, den sorgen dock.
Styrväxel
Med subframen på plats finns det inga ursäkter – dags att börja montera komponenter!
Först ut blev att få styrväxeln på plats. Den har figurerat tidigare på sidan, men sedan senaste update har den lackats i samma RAL7015 som resten av underredet. Dessutom har kuggstången hålborrats i den runda delen av stången för att spara vikt. Långhålsborrningen gav 185 gram viktbesparing. Kan låta lite, men varenda detalj vägs på grammet för att hitta onödiga kilon. Fem liknande operationer och 1kg har sparats. 1kg som aldrig hade sparats från en färdigbyggd bil (eftersom man inte bemödat sig att demontera styrväxeln för 0,2kg viktbesparing)…
Ovan vänster: Ingående komponenter är inte särskilt många. Bemödade mig aldrig att demontera rullagret som sitter i botten för ingående axel, så självklart kommer det vara det första som havererar när bilen är färdigbyggd.
Ovan höger: Styrväxel monterad och på plats. Sitter med totalt 5st M8. Även en Flaming River-knut har hittat dit. Tråkigt att någon idiot har satt ett motorfäste rakt i vägen för styraxeln till torpedväggen. Ingenjörjäveln skyller på att styraxeln inte var med på ritningen när motorfästena konstruerades.
Subframe – permanent montering
Permanent som i bemärkelsen att den inte planeras att demonteras någon gång innan bilen regbesiktningen. Skönt.
Dessutom blev det bra! För den som kommer ihåg, har karossen masserats så att subframen kan monteras dikt an mot karossen. På detta sätt erhölls ytterligare 20mm markfrigång. Subframen blir dock fortfarande lägsta punkten på hela underredet. Även om det är tråkigt att få skrapmärken, är den ju tämligen grovt tilltagen och kommer tåla stryk bra.
Ovan: Här är skönheten alltså. Med tanke på antalet timmar det tog att modifiera subframen, behandlas den med mycket stor respekt. Torpväggen fick sig ett otroligt lyft med färg på.
Nedan: Bussningar svarvades i aluminium, ny skruv och bricka inköpt. Loctite medelstark gänglåsning och därefter dra ihop all skruv med moment. Högra bilden visar även att subframen har kompletterats med styrstift. Original finns det ett hål i karossen och ett hål i subframen i de främre infästningarna som ska linjera med varandra. För att förenkla och slippa försöka rikta in ramen när den väl sitter på plats, svarvades styrningar i matchande diameter för karossens hål. Ramen riktar in sig själv numera när man skruvar fast den. Smidigt.
Ovan och nedan; En viss nervositet infann sig när ramen skulle monteras. Det är ändå ca 4 meter svets som lagts på både längsgående originalbalkar, och den nybyggda vaggan i ramen. Trots envetet användande av fixturer, tid för svalning mellan svetsningarna etc så var rädslan att den skulle slagit sig ganska stor. Då hade den inte gått att montera eftersom subframeconnectorsarna (smaka på det ordet, Horace Engdahl!) sluter om rambenen i bakkant.
Ovan; Men den sjönk in som handen i handsken! Otroligt skön känsla! Allt gnetande med svetsfixturer och alla sena kvällar i svetsångor glömdes i samma stund som bussningarna sjönk in i ramen.
Fototips förresten; Det kan vara ganska svårt att ta bra bilder under bilen. Blixten blåser effektivt ut alla färger och förstör ofta bilden. För oss som inte har råd med remoteblixtar och annat kan man, i alla fall på vissa kameror, hålla kameran upp-och-ner samtidigt som man håller blixten med fingret och på så sätt studsa blixten mot golvet och upp i underredet. Resultatet blir betydligt mjukare ljus – se ovanstående bilder.