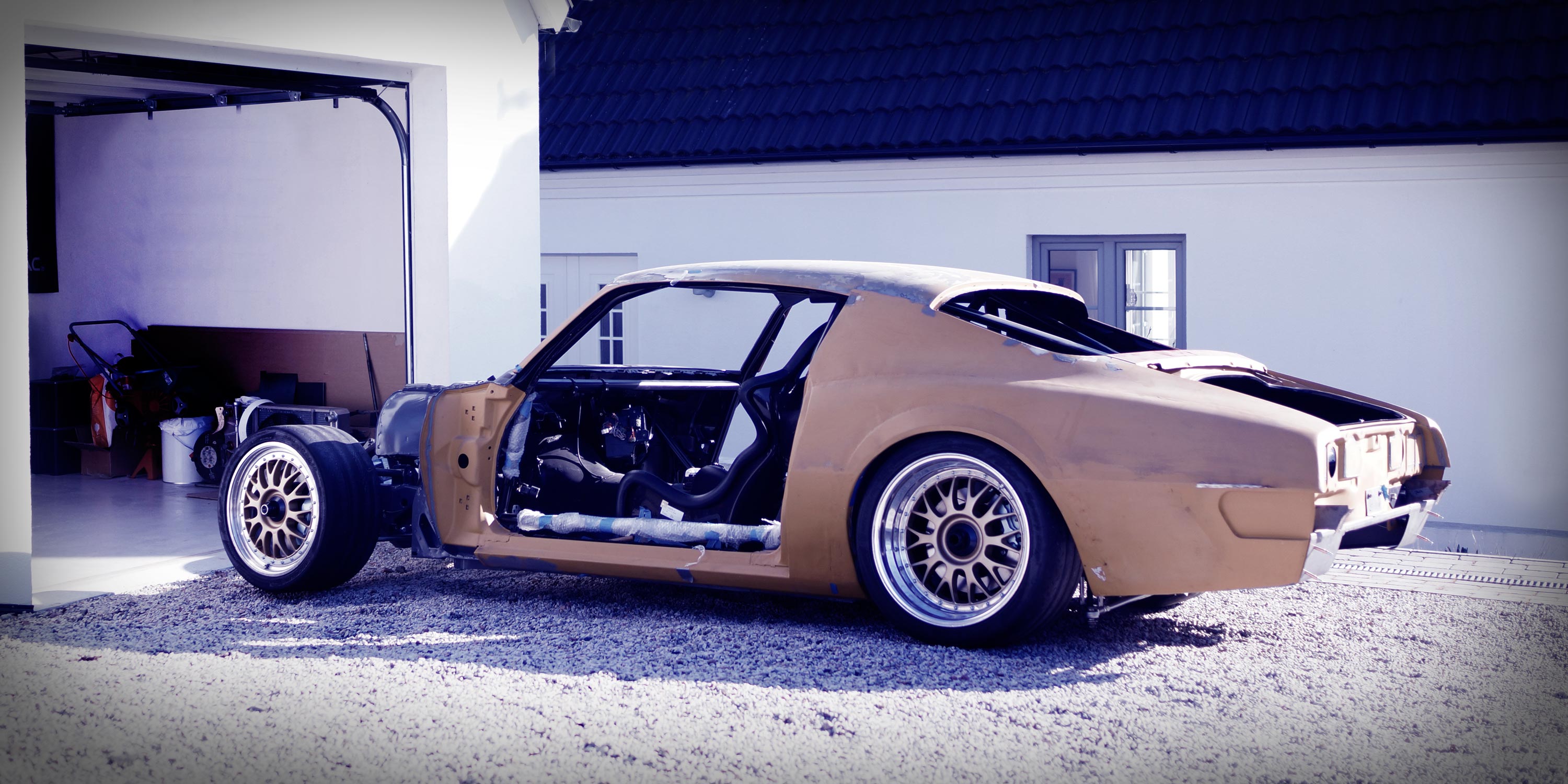
Kategori: Suspension
Ögongodis
Centrummuttrarna är klara!
Fortalmutter på valnötsskiva. Valnöten får dock stanna kvar i köket. Centrummutter, eller centrumbult som många kallar det, M40x3 höger- och vänstergängat, gjord i Fortal-aluminium. 155 gram per styck. Det blir knappast mumsigare än så här…
Det är tur att man har lite kontakter… Samuel, en gammal kollega från svunna tider, jobbar idag med NC-bearbetning och kunde mycket väl tänka sig att hjälpa till med mitt projekt. Samuel är en man som fnyser lite åt detaljer som inte behöver tillverkas med tusendelsprecision och anser att ”ett par stycken” rör sig kring 500 st, men trots detta så var de sex muttrarna en hyffsad utmaning att få till. Utan Samuel hade det varit svårt att ha något annat än vanliga standardmuttrar. Främst för att han efter alldeles för många timmars programmering konstaterade att det nog saknades en nolla på vårt överenskomna pris…
Mmmmm, vackert så det förslår. Samuel står för konsten, brickan till vänster har jag själv svarvat (lite enklare detalj). Det är alltid samma kick att få hålla i verkligheten som man CADat tidigare. Särskilt när de blir så här fina…Det ser kanske lite konstigt ut med femkantiga muttrar, men det handlar om en kompromiss. Femkantiga muttrar innebär att klåfingriga nissar får skaffa en femkantig skiftnyckel för att försöka sno hjulen. Kan vara ganska bekvämt och veta när man är medveten om att bilen sannolikt kommer parkeras på gatan både en och två nätter.
Samuel ställer förresten gärna upp på att NC-svarvjobb åt folk, även om det inte handlar om tusendelar eller 14 000 st till antalet. Om du behöver ”massproducera” någonting med hög precision, både på din fritid eller i ditt jobb, kan jag förmedla kontakten.
Inget vidare slut på 2009
Det första stora bakslaget har drabbat projektet. Trots att det mesta har planerats under en längre tid var inte planen vattentät…
Jag har bara mig själv att skylla och att jag inte läste på tillräckligt om teorin bakom bakvagnskonstruktionen som jag bestämde mig för. Hade jag gjort detta, hade jag insett att länkarmen (den som hjulet sitter fast i) inte kunde fästas så lågt i chassiet som jag hade gjort. En dominerande faktor till att konstruktionen sannolikt kommer underkännas, är att den lider av pro-squat (motsatsen till anti-squat) vilket enklare kan beskrivas som att hjulen vill lyftas från marken under acceleration (bland annat). En högre infästningspunkt hade löst problemet, men det är knappast genomförbart pga en rad andra faktorer.
Ett par hundra CADtimmar är bortkastade pga. detta och bakvagnsprojekteringen är i princip tillbaka där jag började, i april. Dessutom är projektet försenat eftersom det tog längre tid att designa den numera oanvändbara bakvagnen än vad jag planerade med. Grundplanen var att i princip ha bakvagnen installerad i bilen (kanske inte med karossen ståendes på hjul, men nästan) innan årsskiftet. Årskiftet närmar sig dock med stormsteg nu och jag har ännu inte överfört teorin till praktik.
Inget bilrelaterat att fira på nyårsafton med andra ord.
bakre subframe
Oavsett hur bakvagnen byggs, behövs det någonting som håller diffklumpen, bärarmar etc. De längsgående länkarmarna lyckades jag med att montera i originalinfästningar vilket gjorde att inga större modifieringar på karossen behövdes.
När det gäller diffklumpsupphängning finns det egentligen två olika vägar att gå – antingen skär man upp hela golvet och sätter igång med kreativt byggande. Eller så bygger man utifrån det man har och adderar detaljer till originalkonstruktionen. Originalplåten inte hamnar ivägen för bakvagnen, och därför kändes det enklast att göra det sistnämnda. Eftersom jag vill ha möjligheten att kunna ändra bakvagnsgeometrin, utan att för den delen behöver kapa ned hela bilen, blir det en skruvad hjälpram (subframe) som håller diffklumpen och bärarmarna.
Nedan: Röda balken svetsas mellan originalrambenen i karossen. Subframen (som alltså saknas på bilden) håller bärarmar och diffklump. Vad gäller diffklump är jag lite osäker på hur många infästningspunkter den behöver. I dagsläget är det tre punkter, en i bakkant och två i framkant men sannolikt behövs det nog fyra.
Nedan: I sann TV-kocksanda finns redan ett utkast till subframe i samma post! På bilden nedan finns en ram, byggd i 30x3mm. Vikten ligger kring 10kg. Subframen skruvas i den röda balken (som ju var insvetsad i karossen), samt i framkant av originalrambenen.
Att bygga bil (mer än att bara byta fjädrar och dämpare alltså…) kräver sina insatser. Det är inte konstigt att normala bilföretag har så många anställda som de har. I ett ensamprojekt som mitt, får man försöka ha koll på hela kedjan. Undertiden det byggs subframe, ska man ha i åtanke att det skall finnas plats för avgassystem etc. också. Kanske ännu viktigare är att bestämma sig för i vilken ordning det skall gå att montera ned bilen – ska avgassystemet behöva lossas för att bakvagnen skall plockas ned? Skall hela subframen behöva tas bort för att det ska gå att komma åt diffklumpen? Ska alla skruvarna som håller subframen kunna lossas nedifrån? Så där kan det hålla på i oändlighet, men planeringsstadiet är viktigt. Blir det rätt här, slipper man dyra gör-om-gör-rätt-aha-upplevelser senare under projektet.
Centrummutterfälgarna innebar…
…att jag fick tänka om lite. Planen var egentligen att köpa vanliga splitfälgar med traditionellt bultmönster från staterna. Dock dök dessa fälgar från en Porsche Cup-bil upp på begagnatmarknaden och jag kunde helt enkelt inte låta bli att slå till.
Eftersom jag inte var beredd att riskera mitt eget liv genom att räkna fel på dimensionering av centrummuttrarna, lät jag istället någon annan göra det. I detta fall föll lotten på min vän och förre chef, Anders, som gladeligen tackade ja till att omvandla mitt liv till en grekisk bokstav och förpassa den in i någon av hans formler. Anders är en form av supermänniska – han kan 642 decimaler på talet ”pi” och han uttrycker sig ofta binärt istället för i ord. Hans farfars far uppfann matematiken, långt innan Einstein ens var påtänkt. Ibland ser man honom vandra bland vanligt folk, men oftast håller han sig någonstans i närheten av en balk eller något intressant lastfall. Lustigt hur alla förresten heter Anders som är inblandade i detta projekt.
Till skillnad från traditionella fälgar finns här endast en mutter som håller fast hela fälgen mot bilen. Då bilen blir förhållandevis tung (ca 1200 kg) tillverkar jag egna axlar och muttrar, istället för att t.ex. handla formelbilsmuttrar som är avsedda för bilar med halva vikten. Vill man inte tillverka själv, har Porsche muttrar och adaptrar som säkert kan anpassas till det mesta, men så har priset sannolikt lika många siffror som det finns bokstäver i ordet Porsche också…
Ovan: Einst… öh, Anders stannade förbi en kväll på en liten Design Review där det under ett par timmar diskuterades sträckgräns, brottgräns, materialval, gängstigningar och andra nördiga termer. Anders är en formelonanist av rang – det rinner ettor och nollor i venerna på honom och allteftersom jag berättar hur konstruktionen ser ut, gör han beräkningarna i huvudet med tre decimaler. Därefter kontrollräknas det med hjälp av miniräknaren för att få fyra decimaler… Kvällen gick fort och efter att fått diskutera igenom konstruktionen känner jag mig mycket trygg med den. Tack Anders!
Nedan: Efter Anders hade gått hem, dubbelkollade jag genom att fråga det digitala oraklet (Solid Works 2009). Övre bilden visar belastningen som muttern utsätts för vid motsvarande 2G kurvtagning (vilket är mycket, men det kändes som max kurvbelastning plus statlig moms…). Spänningarna i materialet uppgår till ca 50N/mm2 och materialets Rp0,2 ligger kring 550N/mm2. Den lilla bilden visar motsvarande vid 10G – eller en smäll in i en curb/trottoarkant typ… Säkerhetsfaktorn blev i alla fall 11,3:1 även om jag använder aluminium, känns väldigt lugnt eftersom jag siktade på att komma över 5:1.
Nedan: Axeln kördes på samma manér och här hamnade säkerhetsfaktorn på 9,9:1 vid motsvarande 2G kurvtagning.
Nedan: Och så här blir det typ. Om man inte vill göra ett nytt nav från scratch blir det till att addera detaljer till det befintliga. På bilden syns originalnav, förstoringsring för att tillåta större bultmönster, pegs, styrning för fälg eftersom centrumhålet på fälgen är större än vad den var på originalnavet, centrummutter och centrummutteraxel. Utöver detta skall centrummutteraxeln låsas mot navet på ett klurigt sätt som ryms innanför styrningen för fälgen. Ytterligare en bricka ska till mellan fälg och mutter, samt ett säkerhetslås till mutterns om hindrar att den gängar upp sig under färd. Som sagt, mycket delar…
Jobbar du som läser detta med ytbehandling av aluminium, eller har bra kontakter inom det får du väldigt gärna höra av dig till mig! Jag hade behövt muttrarna och ett gäng andra småprylar hårdeloxerade. Posta en kommentar till inlägget, eller sänd mig ett e-mail.
Länkarmen färdigCADad
Nja, nästan i alla fall…
Efter ett gäng olika versioner anser jag mig vara klar med länkarmen och infästningarna till spindel och övriga bärarmar. Vikten hamnade på 4,1 kilo per styck. Jag hade hoppats på ett kilo mindre, men å andra sidan kommer SFRO bli förtjust i den något överdimensionerade konstruktionen. Dessutom kommer den kunna tjänstgöra som skyddsrum under en kärnvapenattack då den är kraftigt överdimensionerad. Skyddsrum för hamstrar eller möss då alltså…
Belastningarna på konstruktionen är ganska enkelt identifierbara tack vare bakvagnens konstruktion – Den längsgående armen tar krafterna från acceleration och inbromsning (det blir till att förstärka den amerikanska Wettexplåten kring infästningen med lite svenskt konstruktionsstål) och de två tvärgående armarna tar hand om de laterala påfrestningarna.
Nedan: Det är just därför man ska börja med att CADa sakerna istället för att gå ut i garaget och värma upp vinkelslipen. På bilden ser man tydligt hur infästningen för länkarmen tar emot fälgbanan. Typisk motivationsänkare efter att man spenderat fyra helger i garaget och slutligen skall sätta på hjulet på den färdigbyggda bakvagnen. Länder har gått i krig med varandra för mindre konflikter än nedanstående…
Nedan: För att få till en bättre infästningspunkt, kommer jag använda ett länkhuvud istället. Det är endast pga utrymmesskäl som det blir så. Ledlager hade också fungerat, men det är tight med utrymme och eftersom belastningarna är så pass uppdelade (Det är bara den där Euler som härskar i de tvärgående länkarmarna, broms- och accelerationsmoment tas upp av den längsgående) kan ett länkhuvud användas utan att få dåligt samvete.
Ovan: En styck färdig länkarm med infästningar för lincolnspindeln och tvärgående bärarmar. Den blev förhållandevis tung, men det beror samtidigt på storleken (ca. 750mm lång). Gjord av 1,5mm, 2mm och 3mm Domex 355-plåt.
Härnäst skall lämplig leverantör hittas som kan ställa upp på att laserskära plåt i lämpliga dimensioner. Sen blir det till att svetsa ihop detaljerna. Lite som att bygga med Lego…
Svingarmsmockup
Efter åtskilliga timmar planering och fundering blev det alltså en individuell bakvagn till bilen. Det gick helt enkelt inte att få till en bra dedionupphängning.
För att försäkra mig om att CADdetaljerna överenstämmer med verkligheten, gjordes en mockup för att kunna testa mot bilen och eventuellt kunna justera dimensionerna innan bearbetat material beställdes. Här på bilden är mockupen fixerad med den underbara uppfinningen silvertejp!
Ovan: Bubblan i främre delen av hjulhuset för bakre bältesinfästningen har tagits bort för att tillåta full bredd på fälgarna. På bilden syns det tvärgående röret som symboliserar bakaxelns kommande position, lincolnspindeln, mockup till länkarmen (samma som på bilden nedan) samt två påsvetsade profiler som agerar nollpunkt vid mätning.
Nedan: I framkant blir det en nylonbussad led från Ballistic Fabrication. Egentligen en off-roadbussning som väger typ 380 kg, men det får gå. Den lär ju i alla fall aldrig slitas ut… Ledlager vill jag helst undvika eftersom det är en gatbil.
Nedan: mock uplänkarm har byggts för att kunna montera hjulet och se hur det sitter i hjulhuset. På den skarpa versionen kommer spindeln monteras i armen med alla tre infästningspunkterna. Länkarmarna som går in mot bilens centrum kommer sedan fästas i länkarmen, inte spindeln.
Ovan: Jag passar på att försöka bli vän med TIG-svetsen när jag bygger mockuper. Det behövs då jag bara svetsat med MIG/MAG tidigare. Resultatet blir rätt OK faktiskt – bra genombränning och till och med snygga svetsar ibland!
Ovan och nedan: Hur tänkte jag nu då? Nja, jag har faktiskt varit fullt medveten om att bakvagnen är något för bred för bilen. Det hade egentligen kunnat avhjälpas med att köpa nya fälgbanor till fälgarna, men fälgkant är snyggt och eftersom jag ändå skulle bygga om hjulhuset (tighta till hjulhuskanten mot kring däcket) så är det inte särskilt mycket extraarbete att bygga ut den ett par centimetrar. Hjulet hamnar egentligen ännu högre upp än vad bilden visar, vilket gör att skärmkanten måste kapas bort – något som jag inte vågar göra förrän bakvagnen är färdigbyggd. Breddningen ska bli diskret och originallinjerna kommer eftersträvas.
Nedan: Dock finns det gott om plats på insidan vilket är bra. Egentligen hade inte bubblan för baksätesbältet behövts tas bort, men det var lika bra att göra det när jag ändå var igång. På detta sätt kan hela hjulhuset utnyttjas om man skulle vilja skaffa bredare däck än 295:or i framtiden…
Nedan: Bakhjulet hamnade 15mm för långt bak och därför behöver länkarmen kortas något. De svarta strecken på karossen är mina trevande försök till att efterlikna plastikkirurgernas anteckningar inför att de ska operera någon. Det blir nog bra. Kanske.
Geografilektion
Att placera infästningarna för bärarmarna, innebar mer än en geografilektion i plåtorientering. Efter en hel del tänkande, ritande och räknande blev det tämligen bra. Jag är långt ifrån någon geometriexpert, men anser mig ha tillräckligt med kött på benen för att kunna komma i närheten av något som fungerar bra. Och om det inte fungerar bra, så låter jag helt enkelt bli att berätta det…
Ovan: På bilden utsätts hjulupphängningen för 2º grader roll. Rollcetrat ligger ganska konstant i förhållande till tyngdpunkten både vid roll och in-/utfjädring. Camberkompensationen är ca 0,5º/grad roll och någon spårviddsförändring att tala om sker inte heller.
Ovan: Länkarmsinfästningarna kommer byggas så att dessa är utbytbara utan att behöva kapa i karossen. Sannolikt hamnar de i samma del som håller diffklumpen, vilket gör att denna enkelt byts ut om man vill testa en annan bakvagnsgeometri, utöver den inbyggda justermånen som kommer finnas. Detta för att underlätta eventuella uppgraderingar/ändringar i framtiden om det nu, mot förmodan, skulle visa sig att Pontiacen inte blivit den ultimata väghållningsmaskinen som jag på fullaste allvar tror att den kommer bli. Jättesnabb ska den bli. Jetesnab. 🙂
Bakvagnstankar
Det nästan svåraste med att blanda in CADkonstruktion i sammanhanget är att mäta upp lämpliga referenspunkter i karossen med godkänd tolerans för att dessa skall vara användbara i CADen. Särskilt när karossen hänger på en vagga. Tack och lov, förfogar jag över en A1-printer vilket gör att jag kan skriva ut många detaljer i full skala och provmontera pappersbiten innan tillverkning i stål görs.
Nedan: Som synes är bilen verkligen konstruerad för en stel bakaxel. Platsen ovanför hjulaxeln är minimal och att montera en traditionell individuell bakvagn med dubbla A-armar sker knappast utan kraftiga ingrepp i karossen. Omregistreringen till ombyggt fordon, gör att jag inte kan börja kapa upp golv hur som helst, utan så mycket av bilens originalkonstruktion måste sparas.
Därför kom det på tal att konstruera en dedionbakvagn. Dels eftersom jag tilltalas av konstruktionen, men även för att dedionbakvagnar brukar kunna göras väldigt kompakta. Efter att ha ritat sju olika versioner som alla var mer eller mindre komplexa, för klena, för tunga eller krävde för stora ingrepp i karossen lades idén på hyllan och istället övervägdes att montera den stela bakaxeln i någon form av trelänksupphängning. Det hade gått att konstruera en bra dedion också men det hade krävt ingrepp i karossen, tyvärr.
Ovan: För att få någon referens i verkligenheten, monterades ett rör där bakaxeln skulle löpa.
Nedan: Istället togs beslutet att konstruera en typ av semiindividuell bakvagn där en längsgående spindel med integrerad länkarm fungerar som tredje infästning. Utöver denna finns två länkarmar som bestämmer camber gain, rollcenter etc. Denna typ av bakvagn är ganska vanligt förekommande på produktionsbilar har jag noterat. Audi TT, Honda CRX, Alfa Romeo 164 m.fl. har alla liknande konstruktioner.
Delarna på bilden är bara ett utkast. Knappast färdigkonstruerade…
Provmontering av hjul
Nja, det är kanske lite tidigt att kalla det provmontering av Pontiacens nya skor, men när det rostlagas behöver det ibland tas till drastiska metoder för att hålla motivationen uppe. Denna gång gjordes det genom att släpa fram BBS E87 fälgarna. 18×10,5″ bak och 18×10″ fram. Däcken som sitter på är utslitna Michelin Pilot Sport Cup. Jag fick dessa av Euromaster på Lundavägen i Malmö för att kunna rulla runt bilen i garaget medan Pontiacbygget tar form. Det känns nämligen lite surt att handla däck, som är färskvara, flera år innan bilen blir klar…
Nedan: 10,5″ fälg är tight i bakvagnen. Mycket pga. att skärmkanterna har en ca 30mm bred läpp inåt, vilket gör att hjulet måste sitta väldigt långt in för att inte förstöras. På insidan finns det dessutom en bubbla för baksätesbältet i framkant av hjulhuset som tar rätt mycket plats. Karossen kommer få en ny skärmkant, som stjäl mindre utrymme och bubblan till baksätesbältet kommer försvinna. Efter det ska det inte vara några utrymmesproblem.
Nedan: Att karossen är avsedd för en stel bakaxel är väl ganska uppenbart när man ser hur hjulet sitter i förhållande till rambenet. Det blir spännande att försöka planera in något annat än en stel bakaxel på detta utrymme!