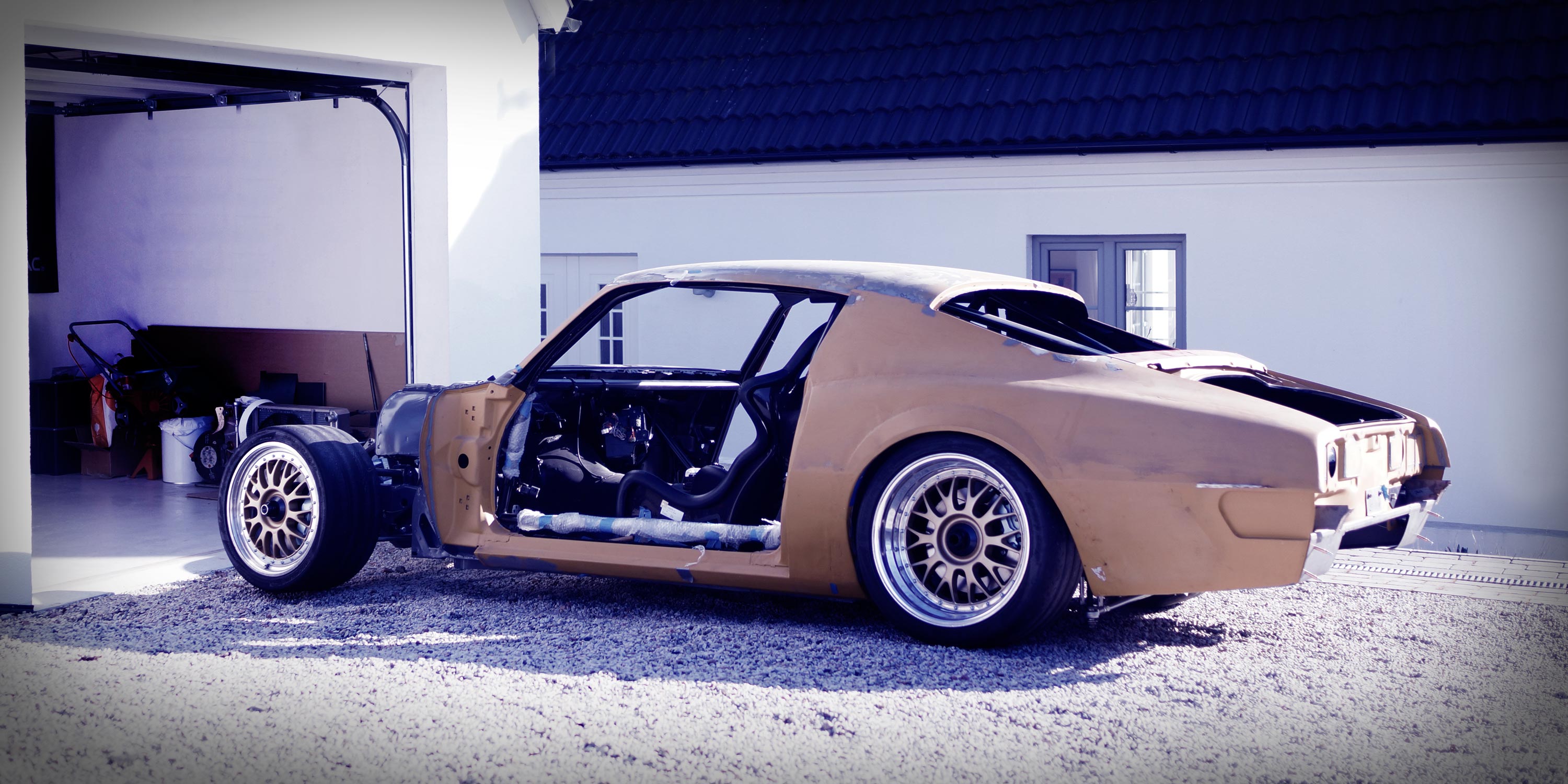
Kategori: The Project
Fortsatt plåtarbete
Aldrig mera rostlagning! Även om det så klart blir bra, börjar det bli ganska mättande att lägga timmar och ännu flera timmar på små plåtbitar som ändå aldrig kommer synas. Små plåtbitar är kanske en underdrift med tanke på bilderna nedan, men det är inte ekonomiplåten som tar tid att pyssla med, utan allt smått kring denna. Nåväl, rostlagningen är på god väg att nå sitt slut! Även om det nog tyvärr inte kommer bli på denna sidan snökaos, minusgrader och hatkärlek till Kung Bore så är det i alla fall på väg mot sitt slut.
Ovan; Den skarpsynte ser att bubblan i golvet för påfyllningsröret till tanken har försvunnit. Eftersom ATL-cellen hamnar högre upp än det gamla påfyllningsröret lades bubblan helt enkelt igen. Det ger ett något mer kvadratiskt bagageutrymme och den lilla plats som kommer bli över efter att tanken installerats kommer, tack vare detta, rymma tre mjölkpaket istället för två.
Nedan; Bakstammens insida rensades på gammal färg och tvättades ren enligt konstens alla regler. Därefter målades den med etsande svetsprimer för att skydda från rost i karosskarvarna.
Ovan; Vissa plåtar nytillverkas inte längre och är lite väl komplexa föra att tillverkas nya från scratch. En lämplig kompromiss är då att rädda all plåt som är frisk på detaljerna och svetsa i ny där den är för rostig. Sen blir det så klart blästring och grundmålning. Dessa sitter ute i bakre kanten av spärmspeglarna och ansluter mot bakstammen. Man kan ana dem på den grundade bakstammen ovanför i denna posten, samt på bilderna strax nedanför.
Nedan; Fantomen är så snabb att blixten står stilla eller nåt sånt. Jag är så snabb att jag både hinner svetsa och ta en bild på mig själv samtidigt. Synd att inte bilskruvandet får smaka på samma snabbhet… Bakstammen svetsas, efter mycket mätande, övervägande och funderande, fast i karossen. Notera hålet för bränslelocket som har lagts igen.
Nedan; Plåten mellan bakhjulet och kofångaren som skärmspegeln sitter fast i var bortom all räddning. Därför byggdes nya från scratch. Dessa har sänkts något för att ge en något renare look under bilen. Dessutom blir fickan som bildas inne i bagaget en finfin plats att tex fästa en liten verktygslåda eller liknande som är bra att ha.
Nedan; Många gånger har jag konstaterat att ”nu måste ändå nollpunkten vara nådd… nu kan det bara gå uppåt från här!”. Bilprojekt verkar vara som aktier – det går alltid att hitta en ny botten man aldrig trodde fanns… Efter ytterligare ett par timmar med tigersåg och vinkelslip ser karossen värre ut än någonsin. Men nu kan det ju ändå inte bli värre… väl?
Nedan; Även vänstersidan är numera bortkapad…
Ändrade tankebanor…
Det finns både för och nackdelar med projekt som löper över lång tid. Nackdelarna är att mycket i tillvaron förändras vilket riskerar att projektet självdör pga. tidsbrist, pengabrist eller andra faktorer som man inte riktigt kan råda över. Fördelarna är dock att man kan hitta riktigt bra köptillfällen för olika saker.
På ett forum där jag hänger frekvent, dök det upp en ATL-cell med bara 1,5 år på nacken som rymde 100 liter. Att säljaren bodde ca 2km från garaget tolkades som ett gott tecken på att cellen var ämnad för Pontiacen och det blev helt enkelt affär.
Grundtanken har hela tiden varit att bilen ska ha en tankvolym som gör att den kan köras längre sträckor än runt kvarteret utan att den behöver tankas. Det innebär alltså en tankvolym på minst 100 liter, gärna mer. I detta fallet blev det ”bara” minimumvärdet, men det kan ju å andra sidan vara skönt att full tank inte kostar mer än 1500:-…
Tanken är en skumfylld gummiblåsa med plastskal vilket känns väldigt bra. En egenkonstruerad tank hade aldrig kunnat ge samma säkerhet som denna. Vid en eventuell krock håller förhoppningsvis blåsan kvar bränslet i cellen. Skulle det gå hål på blåsan, kommer fortfarande skummet bromsa flödet ur tanken.
Ovan; Eftersom cellen kommer hänga under bilen, kommer den monteras i en aluminiumlåda för att skyddas från stenskott osv. På den vänstra bilden syns tanken lite tydligare – den gula kåpan sitter fast i karossen. Tanken ligger i den röda lådan som skruvas mot den gula kåpan. Tankpåfyllningen får flyttas till någonstans kring bakrutan eftersom orignalhålet bakom nummerplåten kommer ge negativt fall (lycka till att hälla i bensin i uppförslutning…)
Nedan; Konstruktionsplanerna på en egen tank hade kommit väldigt långt. Tanken var ritad, en mock-up i papp var tillverkad för att kunna provpassa i bilen och en svetsare var kontaktad. Nu blir det ingen egen tank (men svetsaren får svänga ihop aluminiumlådan dock!) men nedan är några bilder på konstruktionen i alla fall. Upplägget är samma – tanken skulle hänga under bilen, bakom bakaxeln. Därav 10º lutning på bottenplåten…
Skärmspegel
Bakstammen sitter fortfarande fastskruvad i karossen och inväntar svetsning. Det är sannolikt enklare att svetsa både bakstam och skärmar samtidigt så därför sattes det igång med skärmbyte i samma vända.
Ovan; Där bak passades skärmen in mot kofångaren. Tyvärr lämnar kvalitén och passformen en del att önska (bla. olika radier på kofångare och skärm, vilket gör att det blir glapp) men eftersom det är plåt går det mesta att ordna till med vinkelslip och svets… Och kofångaren är röd, inte orange.
[nggallery id=8]
Ovan; (klicka för att byta bild om du inte orkar vänta på bildspelet) Ett bildspel som visar del 1 av bakskärmsbytet. Ser ju enkelt ut på bild som sagt… Är faktiskt inte så jättesvårt heller, bara tids- och tålamodskrävande.
Kan du inte se bildspelet, beror det på att du läser nyhetsmailet. Gå in på hemsidan i så fall.
Ovan; i framkant justerades skärmspegeln tills att den låg jämnt med befintligt karossveck längs sidan. Notera att hålet för dörren är friskt i plåten. Därför skars den delen av den nya skärmen bort. Det blir enklare att spara dörrkanten som referens.
Nedan; Här näst blir det till att bygga upp innerpanelerna bakom skärmspegeln eftersom där i dagsläget inte finns något. Rost – gotta love it!
…och 43 timmar senare…
…kan man konstatera att bakstammen nästan sitter på plats. Arbetet har skett långtsamt och noggrant och en hel del arbete har lagts på sådant som inte synts, tex rostlagning av balkar, bakomvarande plåt osv. Eftersom tröskellådorna bakom bakhjulen också var upprostade, har det mesta upp till bagagerumsgolvet kapats bort. På grund av detta sitter därför bara bakstammen med plåtskruv tills att all plåt bakom bakstammen är fastpunktad.
Ovan; Tadaaaaah! Efterbilden levereras, precis som utlovat!
Nedan; Bakstammen sitter tills vidare fastskruvad med vanlig plåtskruv. Detta för att i lugn och ro kunna passa in kofångare, bakljus osv och enkelt kunna göra justeringar utan att behöva börja borra ur färska punktsvetsar. Referenser från hur den gamla bakstammen satt var svåra att ta, men hur den satt i förhållande till bakomvarande kofångarfästen memorerades för att att ha något att utgå från.
Nedan; Bakstammen visade sig vara av utmärkt kvalité. Varsamt manglad i GMs egna pressverktyg.
Nedan; Det tråkiga med den här typen av arbete är att det inte syns. När väl bakljus och kofångar är monterade ser man inte ens en kvadratmillimeter av bakstammen. Trist, men det ger i alla fall frid i själen och veta att rosten som jag levt med sedan bilen köptes är borta. För övrigt är det snart bud på att börja censurera den där Dodgegrillen som hänger på väggen. Som om MOPAR någonsin skulle vara överordnad GM liksom…
Nothing to see, move along…
Semester innebär sol, bad, avkoppling… och rostlagning.
Om du läser denna bloggen regelbundet, har du säkert noterat varierande bilder där den rostiga bakstammen syns. Eftersom det är ett ganska omfattande jobb att börja byta karosspaneler, sparades det in i det sista i hopp om att någon lämplig period där mycket tid kunde avsättas skulle dyka upp. Det hände också – 2011 års sommarsemester fanns det inget inplanerat på och min bättre hälft jobbar dessutom. Vad kan vara bättre än att spendera soliga sommardagar i garaget? Jag kan komma på många andra alternativ som sannolikt är roligare, men det var bara att bita i det sura äpplet…
Som sagt, ta farväl av den 37 år gamla bakstammen… Nu ska en ny dit!
Ovan; Den obligatoriska före-bilden. En efter-bild kommer… *host host*… senare.
Ovan; I vanlig ordning är rosten man ser bara toppen på ett isberg… När väl kapen åker fram finns det alltid 10 gånger mer rost under ytan. Denna bil är inget undantag.
Ovan; Inte mycket kvar av rumpan nu. Det gäller att hålla tungan rätt i mun och inte kapa bort referenspunkter osv. Det blåa på bilden är Volvos svetsprimer. Kameran hann inte fram innan upprustningen av plåten hade börjat.
Att montera subframen mot karossen…
Det är för närvarande halvtid i bakvagnsbygget. Dvs prylarna sitter monterade i karossen och ”mognar” medans det kluras på infästning av stötdämpare. Eftersom det finns en del annat att pyssla med på bilen innan den blir klar (jo, tjena…) så kländes det lägligt att framvagnen påbörjats. Sannolikt kommer samma typ av konstpauser infinna sig under denna delen av konstruerande och då kan arbetet med bakvagnen återupptas…
Subframen som syns här på bild och hör till originaldelarna på bilen, har varit ute på drift i Sverige. För att göra en lång historia kort, såldes den iväg tillsammans med resterande delar av framvagnen. Eftersom jag börjat halka efter lite i tidplanen, samtidigt som SFRO var lite lätt tveksamma till att montera dit en helt egenbyggd framvagn konstaterades det att det sannolikt är snabbare och enklare att utgå från originalramen. Det visade sig att köparen egentligen inte behövde ramen utan bara var intresserad av de lösa detaljerna (han ville köpa sakerna löst egentligen, men jag ville bli av med ramen pga platsbrist). Snällt nog, fick jag tillbaka ramen när planerna för bygget ändrades. Det hade gått att bygga en egen, men gränsen mellan ombyggt och amatörbyggt fordon hade blivit hårfin och risken för personlig tolkning kändes lite för stor.
Därför föll valet på att utgå från originalsubframen.
Ovan; Det stora problemet med originalsubframen är att den hänger väldigt långt under karossen vilket påverkar markfrigången på låga bilar. Minns inte riktigt, men det handlade om ca 35mm under beräknad lägsta punkt på bygget. Vilket i sin tur hade inneburit en markfrigång på 55mm vid lägsta punkt. Nja, inte så bra.
Subframebussningarna kan kortas utan att ramen behöver genomgå några modifieringar, men för att komma åt de sista 10 millimetrarna, krävdes det lite kapande i ramen.
Ovan till vänster; En uppsättning temporära subframebussningar svarvades till för att kunna provmontera framvagnen. Därefter sattes mätningarna igång för att se var ramen behövde kapas (höger bild). Efter många dubbelmätningar (och trippelmätningar) plockades kapen fram och ett 14mm urtag gjordes i rambenen. Är man lite fiffig, kan man dessutom fälla i originalplåten i det nykapade hålet, vilket innebär att ramen inte ens är modifierad eftersom den fortfarande består av originalmaterial *host host*.
Nedan; Färdigt resultat! Ramen sitter ca 25mm högre upp mot karossen än tidigare. Nu är den bara knappa 10mm under lägsta punkt på karossen. Att ha ett par glidmedar i form av subframe som eventuellt kan skydda vid curbs eller annan närkontakt känns rätt bra. Dessutom är de oömma, och gör egentligen ingenting om de tar i någonstans.
länkarmar, bakvagn
Det är inte supertempo i garaget för närvarande av olika anledningar. Inget allvarligt, utan om ett par veckor kommer det återgå till det vanliga några-dagar-per-vecka-mecket. Tills vidare bjuds det på något som blev klart för några veckor sedan; Länkarmarna är färdiga för provmontering. De är bara punktade samman, så när väl bakvagnen demonteras igen kommer det bli många många många timmars svetsning av diverse detaljer…
Ovan: Ballisticbussningarna lär aldrig slitas ut. Någonsin. Med tanke på att de är gjorda för off-road-racing inser man snabbt när man håller dem att de är tämligen överdimensionerade för track-day-åka. Nåja, desto bättre…
Ovan; Hemmasvarvade vantstag. M20x1.5-gänga. Att notera nästa gång man gör egna nyckelfattningar på saker; Det är bra att först kolla upp vilka standardmått fasta nycklar har innan man sätter upp sina svarvade saker i fräsen. Då slipper man stå med nyckelfattning 29mm när det är 30mm som är standard… Den typen av misstag händer en gång som sagt.
Nedan; Lite svårt att få bilder på sånt här monterat, men här är i alla fall en där man kan ana de tre längsgående länkarmarna. Hade varit skönt att åtminstone få lite grundfärg på karossen snart så att den får samma färg överallt. Börjar bli rätt trött på ”flerfärgat”.
Houston, we’ve got touchdown!
Bakvagnen sitter monterad i bilen! Förvisso i temporära träbärarmar (för att testa ut korrekt längd) men den sitter där ändå. Underbart! Det var förvånansvärt enkelt att montera bakvagnen i bilen – lite som lugnet före stormen, men stormen lyser fortfarande med sin frånvaro (tack och lov). Bredden på bakaxeln visade sig vara ca 10-20mm för bred för att passa i karossen; ovankanten på hjulen sitter någon millimeter utanför hjulhuset med 1,5° camber. Det hade varit bättre att ha dem sisådär 5mm innanför hjulhuskanten på varje sida istället. Tur nog är det ganska enkelt att korta bakaxeln eftersom fixturen för att svetsa den i inte ens behöver modifieras. Det är dock ingen brådska med kortningen, utan hela bakvagnen (länkarmar, panhardstag, coiloverinfästningar osv) kommer sannolikt att byggas klar innan det tas ställning till om bakaxeln måste kortas eller ej.
Ovan; När man tittar på den här bilden, är det kanske inte bakvagnen som ögonen fastnar på. Inte heller fälgarna eller att höger bakskärm delvis är bortkapad (ett framgångslöst meckpass avslutades med att plocka fram vinelslipen och kapa av den rostiga bakskärmen i ren ilska) , utan snarare den förskräckligt skabbiga bakstammen – vilken tur att det ligger en sprillans ny på hyllan och väntar på montering…
Ovan; Några mindre justeringar kommer behövas, men i övrigt passade bakvagnen som det var tänkt.
Ovan vänster; det ser genast mer ut som en bil när bakhjulen har något att sitta i. Så fort bakvagnen är klar, är det dags för framvagnen och när den är på plats kommer nog bilutseendet hitta tillbaka ganska snabbt.
Ovan höger; Hjulhuset är inte särskilt runt. Funderingar på att bygga om hjulhuskanterna och tighta till dem kring hjulen finns. Får se om det blir verklighet – det är ganska pilligt att få till sånt där bra.
Bakvagn! Bakvagnen! Den är ihop!
Det är verkligen 100% tempo på projektet för närvarande! När ”målet” kan börja sniffas ökar viljan av att korsa mållinjen. I detta fallet är mållinjen att få in bakvagnen i bilen för att få känna känslan av att projektet går framåt. Även om det återstår mycket jobb med att prova ut plats för fjädring, karossfärstärkningar osv. så är detta ett stort framsteg för mig.
Målet var att bakaxeln skulle vara testmonterad i bilen innan den siste maj. Med andra ord är man för en gångs skull före tidplanen, något som inte händer särskilt ofta i bilbyggarkretsar…
Ovan; Fläskiga fälgar och ball hjulupphängning. Det här kan bli ungefär hur bra som helst! Tänk om man hade kunnat köpa det här som byggsats istället! Vad najs det hade varit! Många timmar har lagts ned på svarvning, fräsning, kapning,, ritande, svetsning, räknande, konstruerande, funderande osv innan dags datum. Notera även mina billet MDF-bärarmar. Tack vare träets fjädrande egenskaper behöver man inte gummibussningar, utan kan klara sig med solida bärarmar. MDFen måste dock fuktskyddas för att klara av att köras i regn. Jo men visst…
Ovan; 34 svarvade detaljer, 2,4 meter svets (när den väl är helsvetsad), okänt antal kapningar, några kvadratmeter plåt och några hundra timmars nagelfarande i CADen så blev det till slut en bakvagn. Här syns även bromsokshållarna (tandpetarna ovanför hjulnaven).
Ovan; Med 295x30x18″ så ser det rätt kaxigt ut faktiskt. Den totala vikten på delarna som syns på bilden ligger bara några kilo över en tom 10-bultad originalbakaxel – med andra ord har tämligen många kilo sparats in på bakvagnen. Exakt hur mycket kommer bli väldigt intressant att se, men det rör sig om mer än 50 kg ofjädrad vikt som har bantats bort.
Ovan; Kan man inte ha en genomskinlig kaross så att konstruktionsporr av den här kalibern kan visas för omvärlden på ett enkelt sätt? Bakaxeln är nästan lite för mumsigt för att gömmas undan under en gammal 70-talskaross…
Så, då var det dags att montera den i bilen. Men vi kan väl dra ut på spänningen ytterligare några dagar, va?
Centrummutteraxlar
Redan i förra uppdateringen kunde navet provmonterat på fälgen skådas. Det innebär såklart att centrummutteraxlarna bak redan var klara då – dock måste man ju spara lite på godiset och fördela det jämnt till läsarna, haha.
Anyway – centrummutteraxlarna har varit tämligen pilliga att tillverka – svarvning, gängning, svarvning igen, fräsning, fräsning på rundmatningsbord osv. De har varit på gång ”till och från” under flera månader. Men till sist blev resultatet riktigt bra!
Ovan; Vi får väl börja med det färdiga resultatet. Här är centrummutteraxel och låsning för den samt nav på bilden. Centrummutteraxeln skruvas direkt på drivaxeln istället för den vanliga muttern. Därefter träs en låsning över axeln som fixerar den i förhållande till navet. På så sätt riskerar inte axeln att gängas upp. Därefter träs en centreringsbricka över (eftersom Porschefälgarna har större centreringshål än lincoln) och till slut låses allt axiellt med en segersäkring. Centreringsbrickan och segersäkringen finns på bild längre ner.
Ovan; Centrummutteraxeln. Total vikt 336 gram/st, gjorda av Impax Supreme. M40x3-gänga. På högra bilden skymtar även ett ämne till de främre axlarna.
Ovan; En lite mer förklarande bild. Det vänstra patentmecket föreställer drivaxlen, därefter kommer navet (saknas på bilden), en bricka, centrummutteraxel, låsning (mellan axel och navet), centreringsring och till slut segersäkring. Normalt brukar folk tillverka en riktigt tjock spacer och sen gänga ett rör i denna för att på så sätt få en centrummutterlösning. Problemet är att det bygger väldigt mycket utåt, scrubmåttet ändras och hjullagren slits i onödan. Min lösning är något mer komplex och kräver lite mer pillande, men i slutändan blir det riktigt, riktigt bra.
Ovan; Färdigmonterat! Eftersom styrpegsen inte är tillverkade än (har du en styrd svarv, så kan du väldigt gärna få hjälpa mig!) fick det duga med en uppsättning gamla originalskruvar istället.
Sådärja! Nu är det faktiskt klart för provmontering av bakvagnen i bilen! Mycket jobb återstår ju såklart innan den kan kallas ”färdig”, men det är såklart bra att provmontera innan den är helt färdig. Då svider det inte lika mycket om något skulle visa sig vara fel…
hjulnav
Med bakaxeln färdig för provmontering, hamnade fokus istället på kringdetaljer som måste vara klara inför testmonteringen. De detaljerna som kommer från Lincoln Mark VIII i bakvagnen är inte riktigt anpassade för Pontiacens behov, så därför är viss modifiering nödvändig. Naven är tex gjorda för bultmönster 5×108 och inte 5×130 som BBS-fälgarna kräver. Såklart fanns det inte tillräckligt med material på flänsen för att borra om bultmönstret utan operationen blev större än vad det var tänkt från början. Som vanligt.
Ovan: Här är patienten, ett nav från Lincoln Mark VIII, som kanske har sett sina bästa dagar vad gäller puts – ingenting som inte ska gå att ordna…
Ovan; Eftersom navet är för litet för att borras om till 5×130, svarvades en ring som pressades utanpå för att på så sätt få en tillräckligt stor fläns. Navet kyldes därefter ned till -40°C och ringen värmdes till 250°C. Därefter bar det snabbt av mot pressen…
Nedan; …där delarna sedan pressades ihop med varandra. Sen fick det svalna. Resultatet syns på högra bilden nedan.
Nedan; Därefter svarvades navet både på fram och baksida.
Nedan; Efter en stund i fräsen finns det numera både GM 5×120.65 (som även får fungera för BMW…) och Porsche 5×130 i naven. Det går dessutom både att köra centrummutter eller traditionellt fembult, så fälgmöjligheterna känns ganska framtidssäkra….
Nedan: Naven fick en omgång plasticote gjutjärnsgråa värmetåliga färg på sig för att behålla en någorlunda finish även om några år (dvs när bilen börjar bli körbar…).
Ovan: Woho!!! Titta, det passar! Titta titta!!! provmonterat för första gången! Härlig känsla att faktiskt börja montera saker, istället för att demontera hela tiden!
Nedan; Spindlarna glasblästrades för att passa in i resten av nybilsfinishen som komma ska. Den tillhöger är inte blästrad…
Nedan; Därefter svarvades bussningar som pressades i de nedre bussningshålen samt bromskylningen tillverkades också. Blank plåt är perfekt när det handlar om värmereflekterande prylar – sån tur att det låg lite spillplåt i en hörna på jobbet då…
Nedan: Bonusbild. Nu ska nytt hjullager monteras och därefter åker navet i.
bakaxel nästan färdig… som vanligt.
Det här med hemmapulade saker tar sin lilla tid. Så här när bakaxeln börjar närma sig färdig hade det varit ganska intressant att veta hur lång tid den faktiskt har tagit att sammanställa. Alla svarvade detaljer, alla konstiga rörkapningar, alla dubbelmätningar innan kapning osv. En sak är klar dock – jag har sparat åtskilliga timmar på att få laserskuren plåt levererad. Det är lätt att inse de gångerna då någon enstaka plåt har behövt tillverkas. Därför vill jag rikta ett extra tack till Mats och Henrik som har ställt upp med plåtleveranser i tid och otid.
Nåväl; Bakaxeln är sammanpunktad! Äntligen! På bilden nedan sitter visserligen tvärsträvorna med maskeringstejp, men även dessa punktades fast strax efter att bilden togs. Tredje länkinfästningen skall också stagas upp lite mer än vad bilden visar.
Ovan: Några extra bilder på bakaxeln
Nedan: Där finns en hel del knasiga rörkapningar i konstruktionerna. Särskilt där rören möter två ytor eller fler. Eftersom det tar en evinnerlig tid att sätta upp rören i fräsen, kapa med hålsåg en, eller två gånger skrivs istället omkretsen ut på ett papper som därefter hålls runt röret och ritas av. Därefter är det inga problem att kapa röret med vikelslipen och jämna till det i bänkslipen. 1 minut totalt, jämfört med 15-20 minuter i fräsen…
Nedan: Spindelhållarna till bakaxeln, som är lösa för att kunna shimsas till rätt toe, är också klara. Här är ju inte mycket att testmontera, utan de helsvetsades med en gång.
Nu är det lite modifieringar på naven och färdigställande av centrummutterlösningen som väntar innan hjulen kan monteras och bakaxeln kan skruvas dit. Kul!
Rörkapning
De som är flitiga läsare här, kommer säkert ihåg att bakaxelkonstruerandet började med att hitta lämpligt material?
Eftersom jag bara har en rörstump gällde det att ha tungan rätt i munnen när det var dags att sätta kapen i det. Efter ett par hundra överdrivna dubbelkollar mot CADen hamnade så röret äntligen i sågen för kapning.
Ovan till höger: Eftersom röret skulle snedkapas i båda ändarna och kapningarna skulle vara parallella med varandra behövdes det ett referensplan för att mäta in det i sågen. Referensplan är ju lite svårt på runda tingestar, men ibland är det svåra enkelt – loppa dit en fyrkantsprofil innan kapning och placera den med lämplig vinkel i sågen så blir båda sidorna parallella!
Ovan: Tadaaah! 4º snedkapat i båda ändarna, redo för att monteras i fixturen.
Nedan: och då blir det så här fint! Nu börjar man snart kunna gissa att det ska bli en bakaxel…
Ovan: Mmmmmm, härlig kick när man monterar rören i fixturen och det bara passar direkt… CAD är Guds gåva till… typ hela mänskligheten! Röret har 4mm gods, så självklart fasades kanterna inför svetsningen…
Nedan: Fin passform ute i kanterna också.
Härnäst blir det till att punkta samman bakaxeln och släpa ut den till bilen för att kontrollera att verkligen allt passar som det ska.
Bakaxelfixtur
Det är effektiva dagar i verkstaden just nu. Inför att bakaxeln ska svetsas ihop måste den fixeras. Annars slutar det sannolikt med att den kommer se ut som en banan.
Tyvärr har jag inte riktigt resurserna att CNC-fräsa den där billet-alufixturen utan får nöja mig med betydligt mindre exklusiva material än så. MDF är tex.ett alldeles utmärkt material att bygga med. Sagt och gjort fick Bauhaus såga upp 25mm MDF-plattor i lämpliga storlekar som sedan borrades i fräsen för att hålen skulle hamna så exakt som möjligt. Man kan ju tycka att en fixtur i trä borde gå ganska snabbt att slänga ihop. Det gör det inte – det tar flera efter-jobbet-vardagskvällar innan det blir klart. Dessutom hamnar hålen spegelvänt mot vad man tänkte att de skulle göra… Oftast är det fräsens fel, inte han som styr den…
Men efter en veckas flitigt jobbande är den numera klar.
Ovan: För att få hålen så rätt som möjligt i förhållande till varandra, borrades dessa i fräsen. Lite pilligt när träskivan är större än fräsbordet…
Nedan: Och såklart CAD-referensen så att man ser vad det ska bli i slutändan.
Nedan: Här är dedion-fötterna, som jag kallar dem, monterade i fixturen.
Nedan: Tadaaah! Färdigt. Nästan i alla fall. Lite stagning mellan ändarna återstår för att få den tillräckligt styv inför svetsning. Som sagt, lätt som en plätt att bygga fixtur…
Så, då var det dags att kapa röret i lagom stora bitar då… Något jag dragit mig för ganska länge eftersom det blir väldigt dyrt att köpa ett nytt om jag skulle göra fel. Vid närmare eftertanke går det att dra ut på det någon vecka till… Eller månad.
En pall kommer lastad….
…Med vad då?
Ovan: Med bakaxelplåt såklart!
Det finns vänliga människor, och sen finns det ännu vänligare människor. Mats på Habo Rostfria och Henrik på en annan firma (hans chef kanske läser här… Haha!) har varit mycket hjälpsamma och försett mig med plåt baserat på mina CADunderlag. Jag slipper med andra ord att stå med vinkelslipen och karva ut detaljerna. Istället kan jag genast börja pussla ihop delarna med varandra (den skarpsynte ser att jag redan tjuvstartat när denna bilden togs).
Nedan: Här är ändarna på dedionen. Inte så mycket att säga om det hela mer än att det är kul att leka med TIG:en när det är så bra passform på delarna. CADbilderna längst nere är bara som referens. Prylarna ser som sagt ut lite mer kompletta i verkligheten eftersom jag inte orkade rita de enklaste plåtarna i CADen.
Det mesta arbetet sker just nu framför datorn och svarven/fräsen. Karossen får vänta på bättre tider, men lite småsaker som är relaterade till bakvagnen sker dock fortfarande.
Nedan: Diffen monterad i karossen för att prova ut lite olika upphängningar av bakre infästningspunkten. Som synes är det ganska ont om plats. Desto bättre att börja med pappmallar innan detaljerna tillverkas…