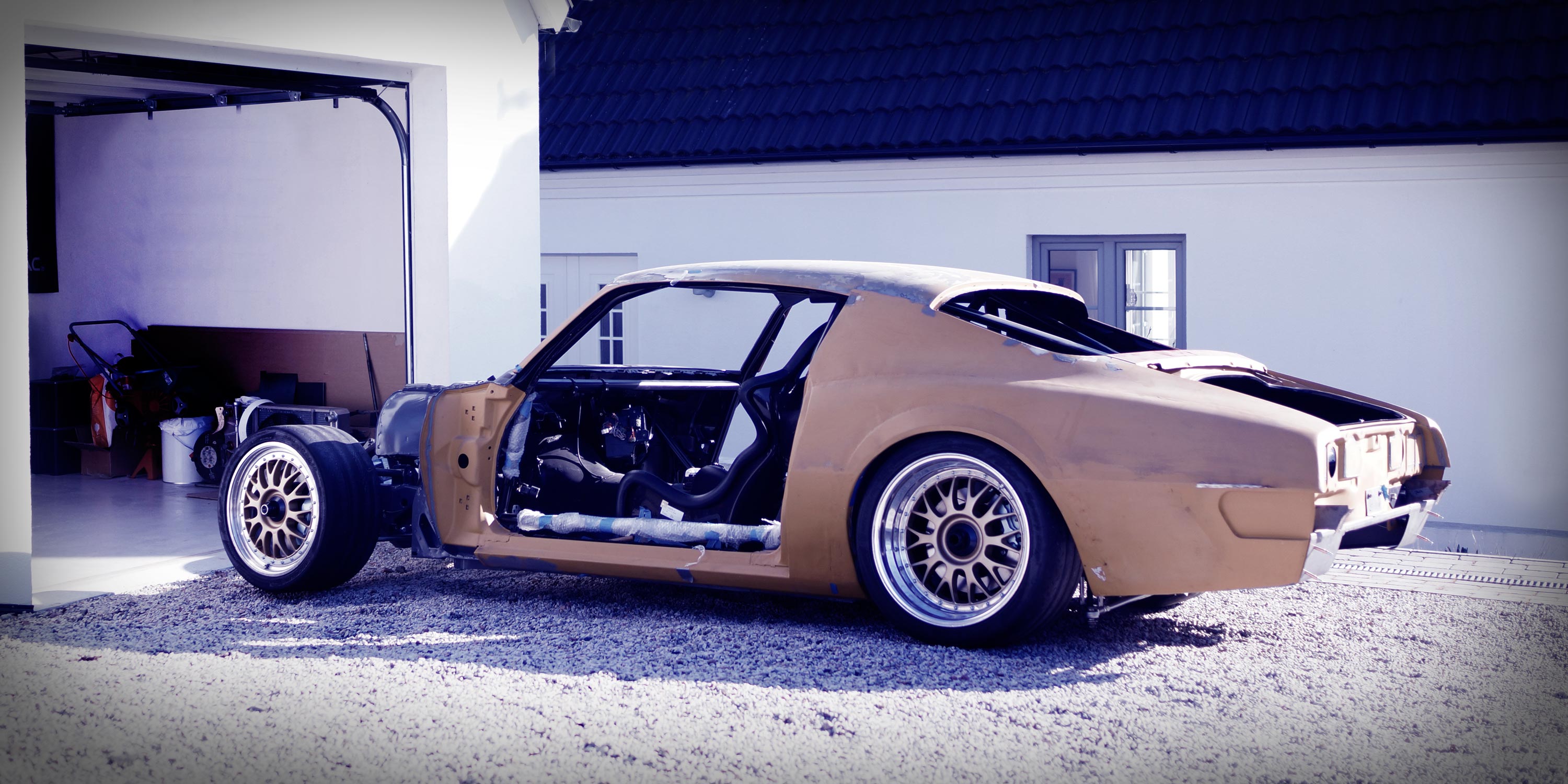
Kategori: The Project
(Kaross)kitt vad häftig den kommer bli!
Karossen har äntligen fått färg på både underrede och kupé, vilket är ett av de största stegen i projektet! Detta markerar tid för att vrida om låset på spärrskaftet och faktiskt börja montera fast saker på karossen. För den som aldrig hållit på med bilprojekt är det nog svårt att föreställa sig, men de flesta som läser här kan nog sätta sig in i glädjen (och även lättnaden över att rostlagningsjobbet är avklarat) som detta innebär. Alla saker som monteras tillbaka är nya eller renoverade. Det innebär i princip att det kommer vara vita bommulshandskar som gäller… Skön känsla som sagt.
Men vi tar det från början…
När plåtarbetet har varit så här grundligt, kändes det högst motiverat att skydda det inför framtiden. Därför har såklart den bästa av den bästa grundfärgen – Hagmans CA-primer – valts. Först sprutades ett förtunnat lager på och därefter lades ytterligare ett lager ovanpå. Även om det ligger färg i skarvarna, är de såklart inte täta. Därför lades det karosskitt i varenda skarv. Varenda skarv. Alla skarvarna… Det är rätt många på en sån här bil, inte bara pga att den rostlagats utan för att det redan från början bestod av mer än en plåt.
18 timmars penslande och dragande med pekfingret för att jämna ut fogarna innan jag blev nöjd. Terapiarbete är bara förnamnet. På frågan om man tycker allt bilrelaterat arbete är jättekul finns det ett väldigt enkelt svar; Nej. Men bra blev det och nästa gång Pontiacen rullar i ösregn ska jag skänka underredet en tanke…
Sen var det dags att skydda hjulhusen. Här finns egentligen inget 100 procentigt skydd. Bilen kommer förhoppningsvis både rulla på slicks och R-däck i olika omgångar, och båda dessa däckstyper är klibbiga vilket innebär att det i princip blir en stentrumlare i hjulhusen. Men det tar vi i morgondagens post.
Bur, etapp 3
De sista detaljerna på buren är gjorda och nu väntar bara svetsning innan buren äntligen kan betraktas som klar. Det är gott om rör. Totalt handlar det om 49,5 kg rör. Karossen har totalt lättats på 16,5 kg så det handlar ändå om 33 kg viktpålägg. Inte så mycket att göra åt, vridstyvhet och säkerhet får värderas högre än låg vikt i vissa lägen.
Ovan; Det tog ett tag innan kragningarna i hålen gick att få till. Ett par pressverktyg fick tillverkas, men slutresultatet blev riktigt bra. Dock är det ganska tufft att handbocka 1,5mm plåt med korta plåtytor och långa bockningar. Slutresultatet blev dock oförskämt bra!
Nedan; Och med stolarna i kunde även höjden på bältessträvorna spikas. Har fått en del kommentarer på att strävorna sitter olika högt, men det har med att stolarna sitter på olika höjd att göra. Passagerarstolen skruvas direkt mot golvet, medans förarstolen hamnar på ett justerbart underrede. Passagerarstolen hamnar ca 35mm närmare marken än förarstolen vilket är bra vad gäller tyngdpunken.
Ovan; Höjden på de övre sidosträvorna blev också bra. Fortfarande ganska enkelt att kliva i och ur bilen. De demonterbara ändarna kommer från Demon-Tweeks.
Nedan; Det tråkiga med karossjobb är att arbetet inte syns då det täcks med färg på utsidan, inredning på insidan och matta i bagaget. Dessutom är bilen för låg för att någon faktiskt ska kunna tex syna underredet. För att ändå göra någon sorts subtilt klargörande om att detta är ett bilbygge som är lite mer utöver det vanliga, tillverkades det ett par plåtar mellan A-stolpen och buren. Även om de, precis om buren, kommer vara mattsvarta kommer de ändå gå att skönja. Högra bilden visar lite nödvändiga fix för att slippa mysko håltagning i instrumentbrädan…
Nedan; Ja, jo… Men det här blir nog rätt bra faktiskt! Även om buren som sagt blir svart (och även inredningen) kommer det nog bli ganska stiligt. Om det inte redan framgått, är jag fan av ”diskret utstrålning”. Högra bilden visar att man får ha huvudet med sig när buren byggs… Det var inte helt självklart att batterilådan skulle kunna trasslas in bakom krysset och placeras på golvet. Efter några övningar gick det dock. Tur, så slipper man ha den monterad för all framtid…
Det är nära nu!
De senaste dagarna har spenderats på att förbereda lackering av underrede och kupé, något som behöver göras innan termometern kryper allt för nära nollan.
Så här såg det ut för bara en liten stund sedan och när du läser detta finns det en stor chans att bilen redan har fått färg på sig. Om detta har skett smärtfritt, är det en av de största händelserna genom projektet. Det sätter nämligen stopp för mer svetsande i karossen och från och med nu kan alltså fokus riktas på renodlad konstruktion, samt permanent montering av diverse detaljer. Otroligt skön känsla!
Bara nedförsbacke härifrån med andra ord!
Sektionering och försänkning
Att något behövde göras för ett modernare utseende på kofångaren var klart. I detta fallet blev det en försänkning av kofångaren, in mot karossen, och på så sätt få den något mer strömlinjeformad. Detta kräver inte bara modifiering av karossen, utan även sektionering av kofångaren. Tyvärr är exemplaret på bilderna lånad, så jag söker efter en 70-73 Firebirdkofångare att sätta kapen i. Skicket är inte så viktigt, så har du något liggande får du gärna höra av dig!
Ovan; Ett par plåtar för att fylla gapet under kofångaren knackades till. Då de är dubbelkrökta gick de inte att göra i en och samma bit. Högra bilden visar tydligt att kofångaren måste sektioneras ca 3cm på varje sida av karossen. 6cm lägre vikt är ju alltid trevligt… 😉
Ovan och nedan; Plåtbitar fästa. För att hålla koll på at kofångaren ligger horisontellt, tejpades horisontalplanet upp på karossen (blåa tejpen).
Nedan; Det här blir nog rätt bra. Som synes kommer diffusorn i mitten bli lika hög som kofångaren vilket nog kommer ge ett ganska mäktigt utseende åt bakändan (bye bye subtila utstrålningen…). Att bagagegolvet och nedre kant på kofångaren hamnade i samma höjd var ren tur dock. Ibland ska man ha sånt också.
Nedan; Byta en sprillans ny och ordentligt svetsad bakstam för att årsmodellen byts kommer inte på tal. Istället tillverkas det nya lampinfästningar. Eftersom bakljusen ändå lär LED-konverteras, kändes detta som en ganska bra lösning på årsmodellsproblematiken.
Nedan; Något som dock inte visade sig lika enkelt var att skruvtornen på bakljusen såklart inte ligger i samma plan. Detaljgranskande på högra bilden ovan gör att man kan ana nedanstående operation; För att få bra anläggningsta för skruvtornen, fick helt enkelt plåten pressas lokalt kring hålen. Det tog ett tag att få rätt vinkel, men tålamod är en dygd sägs det… Varför det gjordes så stora pressningar (D30mm) är för att muttrar med karossbricka skall få plats.
Framvagnsbalken
Subframen låg som sagt färdigkonstruerad i datorn under nästan ett år innan det var dags att faktiskt sätta igång med den. När det väl var dags att sätta ihop den gick det på ett (långt) meckpass innan den kunde betraktas som färdig för helsvetsning.
Ovan; En hög med profiler kapades upp och gjordes i ordning. Detta är ju den stora fördelen med CAD – man bygger efter ritningen och behöver inte mäta tretton gånger för att vara säker på att allt fick plats, vilket kortar byggtiden avsevärt.
Nedan; Likaså har svarven fått arbeta lite innan det var dags att bygga framvagnen på riktigt. Infästningar för styrväxel, länkarmar osv sker alltså genom båda väggarna på profilen för att maximal styvhet. Nya subframebussningar svarvades också till och nya skruvar köptes. Funderade på att hålborra skruvarna för att spara vikt, men orkade inte räkna på de inblandade lasterna, så det lämnades orörda.
Nedan; Som alltid är det svårt med svetsfixturer och hur ambitiösa dessa skall bli. Eftersom detta är lite av ett budgetprojekt, finns det inte utrymme för stora påkostade fixturer utan istället får man jobba med det som finns. Eftersom det var kritiskt med hålens inbördes placering, borrades dessa istället efter att framvagnsbryggan svetsat.
Ovan (igen…); Fast det blev ju trots allt en ganska fancy fixtur ändå. Plattan mäter 500x800x25mm och har M12-hål borrade med 100mm mellanrum. Fungerar väldigt bra som all-roundfixtur när något skall svetsas…
Nedan; Alla fickor grundas såklart. Även hål borras så att risken för frostsprängningar undviks.
Nedan; Hålen borrades som sagt efter att bryggan svetsats klart. På så sätt kommer alla hålen med inbördes korrekta placeringar. Eftersom det i detta fall handlar om inre länkarmsinfästning och styrväxel är det väldigt bra att ha kända mått mellan dessa hål. Det sparar en hel del arbete och huvudkliande när det är dags att shimsa bump-steer senare.
Hålen för länkarmarna borrades 0,5mm under angiven dimension och brotschades därefter till korrekt håldiameter för att inte riskera att hålen blir för stora för skruvarna. Den skarpsynte ser att det både finns horisontella och vertikala hål för infästning av länkarmarna. De horisontella är för vanliga polyurethanbussningar, medans de vertikala är för länkhuvuden (som då medför att infästningen plötsligt kan shimsas uppåt och nedåt om det skulle behövas.
Nedan; Slutresultatet skäms verkligen inte för sig. Helt klart över förväntan. Tillsammans med stagen som går bakåt på ramen och möter upp vid de inre karossfästena kommer ramens vridstyvhet (som är hela chassiets akilleshäl) förbättras radikalt!
Framvagnen
Efter att framvagnsgeometrin bestämts, spindlarna designats och bärarmsinfästningarna koordinater mot chassiet definierats var det dags att göra något åt ramen [eller subframen som den också kallas]. Då befintlig ram visade sig vara i sämre skick än väntat, konstruerades det en ny balk mellan de längsgående rambenen. Det gjordes en hel del experimenterande i datorn för att uppnå bra styvhet kontra vikt.
Efter några månaders ströCADande fanns en vettig konstruktion framtagen. Därefter gjordes de sista finjusteringarna sporadiskt under nästan ett år innan resultatet kändes säkert att tillverka (alltid enklare att göra om i datorn än i verkligheten…).
Slutresultatet blev riktigt bra. Tack vare buren ansluter i vipparmsinfästningarna kommer karossen bli radikalt mycket vridstyvare än original. Dessutom med något lägre totalvikt än original.
Ovan; Några sporadiska skärmdumpar från FEM-körningarna. Kurb-studs och närkontakt med trottoarer skall inte vara några problem med slutresultatet. Rätt många geometrier kördes igenom för att hitta en bra kompromiss mellan vikt och styvhet.
Nedan; Slutresultatet blir såhär. Rördragning över motorn kan möjligtvis skilja sig då det är svårt att kontrollera detta mot karossformen.
Bur, etapp 2
I och med att nya stolar levererats, kunde dessa temporärt monteras i bilen inför att prova ut de sista rören i buren.
Stor vikt har lagts vid att prova ut körställning. Problemet med sidosträvorna är att om de hamnar för högt finns risken att man slår i dem eller (ännu värre) fastnar med armbågen vid styrutslag. Kanske inget man vill vara med om.
Samtidigt skall strävan sitta så högt som möjligt om den skall göra någon nytta och skydda vid en eventuell olycka.
Ovan; Med stol på plats fästes en temporär rörstump i karossen för att simulera burrör. Därefter provsvängdes det helt enkelt (med vilda rattrörelser) för att kunna hitta en lagom höjd. En knytnäve mellan armbåde och rör bedömdes vara rimligt avstånd.
Nedan; Och med stolen monterad kunde även rören till bälten provas fram. På vänstra bilden skymtar även förstärkningsstaget mellan diffinfästningen och karossen. Tyvärr blev det inget hjälmkrossarstag som högerbilden visar. Karossen är väldigt välvd vilket gör att det är tight mellan huvud och sidoruta. Staget stjäl en hel del utrymme. Även med ett böjt stag hade det sannolikt blivit för tight med plats.
Nedan; Övre dörrsträvan blir löstagbar för att inte göra bort sig allt för mycket vid glasskiosken… Delarna kommer från Demon Tweeks.
Konverteringen börjar
Det låg ett mail i inkorgen morgonen efter nyheten om att projektet blir -70 istället för -77. ”Hej, det är Joakim. Jag har en bakre kofångare som du kan låna om du vill”. Sagt och gjort – Joakim besöktes och kofångaren hämtades upp. Planen är såklart att köpa en egen, men ett kofångarlån gör att fästen och den ombyggnation av karossen som krävs redan nu kan förberedas. Därefter kan det letas kofångare i lugn och ro.
Ovan; Joakim är ägare till en hyfsat potent Firebird han också. Dock med ett lite annat syfte än min. Respektingivande motor som sticker upp ur huven…
Ganska snabbt visade det sig dock att kofångaren aldrig kommer kunna monteras som det såg ut original. Inte för att det inte går, utan för att det rent ut sagt ser för jävligt ut. Det ser ju ut som att en järnvägsräls har råkat fastna utanpå bilen när den kör iväg. Det händer bara inte. Ta inte illa upp, alla ni andra som äger 70-73-modeller. På en originalbil ser det ju inte konstigt ut, men på en modifierad bil blir det plötsligt avigt…
Kofångaren måste smalas av och fällas in bättre mot karossen för att det ska bli någon stil på det. Ett jobb som egentligen inte tar mycket längre tid än konverteringen, men det blir svårt att fullgöra eftersom kofångaren är lånad. Jag vill inte gå över gatan en kväll och höra ljudet från en rivstartande kompressor samtidigt som jag bländas av strålkastarna från en svart hämnare…
Karossen kan dock fortfarande modifieras. Resten får bli ett senare dilemma.
Ovan; Det är svårt att fånga på bild, men man kan ana utsticket på sidorna här och att kofångaren faktiskt sitter ca 2cm utanför karossen runt omkring. Vilket i mina ögon inte ser så bra ut… Möjligt att det ser OK ut på bilden, men i garaget ser det i alla fall slarvigt ut.
Nedan; Det ser betydligt bättre ut i svart, även om jag misstänker att just den där kofångaren faktiskt är lite masserad. Sen finns det andra som väljer att vända på utseendet, som den röda modellen. Just den modifieringen är väl kanske inte min kopp te, men det är i alla fall någon till som har förstått problematiken.
Ovan och nedan; En snabb Photoshop visar det jag försöker förmedla i ord ovan. Kofångaren behöver alltså sektioneras uppskattningsvis 60mm på bredden. Motsvarande försänkningar får göras i plåten på karossen för att tillåta att kofångaren har något att sjunka in i.
Styrspindlar
Det blev ett tiotal varianter av spindlar innan jag till slut bestämde mig. Det som skapade problemen var den radiella infästningen av bromsoken. Kan ju enkelt lösas med en adapter, men jag ville konstruera smart och minsann inte ha någon adapter mellan spindel och bromsok. Till slut blev det adapter ändå…
Ovan: en rad olika material och godstjocklekar användes. Sannolikt något överdimensionerade delar, men hellre det än att det går sönder. Styrspindlar är trots allt en ganska komplex detalj som tar laster i många riktningar. Trots överdimensioneringen är vikten lägre än för motsvarande vattenskuren spindel i aluminium…
Ovan; Modularitet och byggbarhet har blivit lite av projektets ledord. För att inte behöva kapa och svetsa för mycket i karossen i framtiden, har tex extra fästen placerats på strategiska platser (i bakvagnen tex om man i framtiden vill uppgradera…). På samma sätt består övre infästningen i spindeln av två alubitar (och genomgående skruvar, men de var visst slut i CADen så brickorna får vara ensamma tills vidare) som enkelt kan shimsas för att få olika SAI/KPI-vinkel
Ovan; En variant av alla spindlar som ritades. Lite dålig bild egentligen, men den består av vattenskuren 40mm aluminiumplatta med utskuren mitt för att tillåta kylluft (under scoopet) passera ut till bromsskivan. Det blev dock stål i slutet pga två anledningar; Alut visade sig behöva vara upp emot 60mm för att infästningarna för bromsarna skulle få plats. För 60mm aluminium gick det inte att hitta någon som kunde vattenskära för under 6000:- för 2st spindlar. Det skall jämföras med ca 350:- som stålspindlarna ovan kostade…
Nedan; Den skarpsynte noterar även att bromsoken lutar något nedåt. Kan tyckas vara ett löjligt argument – men allt görs för att få en låg tyngdpunkt. Nedanstående modifiering resulterade i ca 3% lägre tyngtpunkt på spindelpaketet. Många bäckar små…
Växellådsfäste
Drivlinan flyttas så långt bakåt att växellådsfästet hamnade lagom i höjd med den befintliga förstärkningsbalken i karossen. Istället för att montera ytterligare en profil, kändes det vettigare att nyttja den som redan fanns där.
Ovan; Friskt vågat hälften kapat! Fram med vinkelslipen… igen… Grundfärgen är bra, riktigt bra. Det är slitigt att få bort den från plåten när det skall svetsas.
Nedan; Infästningsplåtarna monterades på en fixtur för att C-C-måttet mellan skruvarna skulle bibehållas under svetsning. Installationen mättes in så att den ligger parallellt med karossbalken och därefter punktades plåtarna fast. Högra bilden visar en av mina andra kunskaper – att upphäva gravitation…
Nedan; Tanken är att ha den här typen av växellådsbalk istället. Förutom att det väger mindre, ger det även mer plats till avgassystemet. Med tanke på hur låg bilen blir, är det välkommet…
Foto: Speedhunters.com
Batteri
Vikt är ju högprioriterat i detta projektet. Även om det inte blir en flugviktare, gäller det att alla tunga saker hamnar på strategiskt bra platser. Grundidén var ju att bränsletanken skulle hamnat framför bakaxeln (två tankar på varje sida om kardantunneln). När det tyvärr inte visade sig vara möjligt om man samtidigt ville kvala in som Ombyggt Fordon hos Transportstyrelsen fanns det istället en möjlighet att placera andra tunga saker där. Bilbatteri är en tung komponent och kompenserar bra för förarens vikt. Därav placeringen på passagerarsidan.
Eftersom det monteras inne i kupén, fick det bli i en tät låda med avluftning genom golvet för att undvika intressanta gasfenomen i kupén…
Ovan; Gott om plats är det ont om. I alla fall går det att lyfta in batteriet mellan bursträvorna. Tur det, för annars hade bakrutan behövts plockas ur varje gång batteriet skulle bytas. Kanske inte så bra lösning…
Nedan; Ursäkta dålig bildkvalité på vänstra bilden – bilder tagna med blixt blir aldrig bra…
Ovan och nedan; På undersidan monterades förstärkningar för att sprida lasten vid en eventuell krock. Ena förstärkningen hamnade i balken vilket krävde en kreativ lösning på hur förstärkningen skulle monteras. En 12x5cm stor bricka stacks in genom ett hål i balken. Därefter vinklades den rätt med hjälp av en magnet. När brickan satt någorlunda rätt, kunde gängstången (som för övrigt är 8.8-kvalité) skruvas genom muttern och en bit in i balken tills att den kunde prickas genom hålet i tunnplåten. Efter det skruvades gängstången genom hålet och låstes med en mutter från kupén. När brickan satt låst mot plåten, svetsades den genom två borrade hål.
Luftkonditionering – Vintage Air
Sval luft är skönt. Man håller sig koncentrerad och ser inte nyduschad ut när man kliver ut ur bilen. Eftersom Pontiacen är en icke-AC-bil från början sneglades det omkring på diverse donatorer på skrotarna. Ganska snabbt konstaterades det att det nästan skulle bli enklare att köpa ett eftermarknadssystem. Inte billigare, men enklare. Tid är också värt något… ibland i alla fall…
Därför föll alternativet på ett Vintage Air-system. Systemet är ju ultrapoppis i USA, så då kan det ju åtminstone inte vara helt skräpigt. Helt rätt visade det sig vara – prylarna kändes väldigt förtroendeingivande vad gäller kvalitén. Hur kylprestandan är blir intressant att se.
Ovan; Systemet känns ganska proffsigt och levereras med noggranna instruktioner om hur inkoppling etc skall ske. Kvalitetsmässigt är det rostfria skruvar överallt, stegmotorer för spjällen och vacuumformade plastkåpor. Känns helt OK för pengarna.
Nedan; Men det som inte framgick innan köpet var att systemet inte har något förberett friskluftsintag, utan istället använder den luften som redan finns i kupén. Personligen trodde jag det skulle vara en självklarhet att systemet hämtade in friskluft så jag brydde mig aldrig om att kolla upp det noggrannare. Detta får åtgärdas genom lämplig fläktkanal fram till ACn från friskluftsintaget vid torpedväggen. Notera även att det faktiskt sitter en Spal-fläkt där och inte något kina-mumbo-jumbo.
Ovan; Även kontrollpanelen är hyfsat gedigen. Frästa aluknoppar, graverad text och bakgrundsbelyst. Blir bra det här! Kommer hamna på mittkonsollen eftersom det kommer bli omöjligt att nå till instrumentbrädan med bältet på.
Styrväxel… Ford Sierra
Till Opel Corsa C-servot/rattstången kopplas sedan en manuell styrväxel. Eftersom det nu för tiden är ganska ovanligt med manuella styrväxlar får man gå ett par år tillbaka för att hitta något vettigt. För att ha tillgång till ett stort antal eftermarknadsprylar, valdes en Ford Sierra-styrväxel. En ganska populär variant, som dessutom har många delar gemensamt med den ännu populärare Escort II-växeln. På sikt kommer sannolikt en kuggstång som ger färre rattvarv införskaffas, men den typen av uppgraderingar kommer först bli verkliga när bilen rullar.
Ovan; Detta var alltså utgångsmaterialet. Talmetern visar hur långt det är meningen att huset ska bli. Skulle det bli fel är det inte hela världen – de går att hitta på skroten för några hundralappar.
Nedan; Hepp! Friskt kapat hälften vunnet. Högra bilden visar geometrin uppifrån. Pga den låga scrubradien hamnar bromsskivan väldigt nära och det är svårt att få styrleden längre ut än spindelleden. Det innebär i sin tur att det inte blir jättemycket Ackermann, men det känns inte särskilt viktigt. För gatbilar som mest rullar på parkeringar i promenadhastigheter är det väl kanske viktigt, men för bilar som används känns det inte så högt prioriterat. SFRO delar kanske inte riktigt mina värderingar här, så byggbesiktningen blir… intressant.
Ovan och nedan; Styrväxeln blästrades och kapades ner till korrekta dimensioner. Tittar man på referensbilden med en iPhone 4 får man ganska enkelt en uppfattning om hur kort den faktiskt är!
Rattstång, el-servo
Traditionell servostyrning har frångåtts till förmån för elektriskt servo. Tidigare kördes både styrning och bromsar på hydraulik, men det fanns stora problem med skumning i oljetanken (och medföljande luftbubblor i systemet) samt överhettning. Eftersom så mycket ändå byggs om, kändes det logiskt att göra ett försök med ett nytt system. Därför plockades servopumpen bort, vilket även frigjorde välbehövlig plats kring motorn. GM-rattstången byttes ut mot ett Opel Corsa C elservo istället.
Corsa-stången är CAN-buskontrollerad, så bytet kräver lite tilläggselektronik för att fungera. Fördelen är att servoverkan kan regleras med en potentiometer vilket gör att vid krypkörning kan servot vara max och i högre hastigheter kan man enkelt sänka servoverkan. Smidigt.
Ovan; Elservot var inte riktigt som klippt och skuren för Pontiacen utan det krävdes en adapterplåt mellan kaross och rattstång. För att styva upp infästningen, monterades rattstången i bursträva samt originalinfästningen (som även delar plats med pedalstället). Infästningen i bursträvan lär göra susen för rattstången, samt även bidra till att styva upp pedalstället.
Nedan; Originalhålet för rattstången lades igen. Blir till att ta upp nytt hål när det är klart var axeln kommer hamna. Keep it inside the family säger de som vet. Opel är ju GM – kul med GM dekaler på lösa komponenter till bilen. Förstärker originalkänslan, haha!
Nedan; En bild på kontrollelektroniken till stången också. Original-ECU till vänster får sin CAN-signal från den lilla svarta plastlådan.
Ovan; ytterligare en bild på positioneringen. Det hade känts tryggt att testa den mot instrumentbrädan också för och se att den inte hamnade för högt. Men eftersom instrumentbrädan inte passar i bilen längre pga buren och det är tänkt den skall gjutas av (och avgjutningen justeras så att den passar i bilen…) handlar det alltså om ett skott från höften. Galet… Men å andra sidan sitter rattstången skruvad i en adapter av plåt som enkelt kan modifieras om det skulle behövas lite finjustering i framtiden.
Hatthylla
Eftersom original hatthylla var tämligen uppskuren, kapades den ganska tidigt bort (för att underlätta åtkomligheten vid nybyggnation av stötdämparfästen etc). Nu när buren är på plats, tätas utrymmet mellan bagage och kupé med aluminiumplåt.
Måste förresten passa på att slå ett slag för Cleckos-nitar! Temporära nitar som fixerar paneler på ett ypperligt smidigt sätt. Hade varit kanon att ha tex vid rostlagning av bakstammen, skärmspeglarna osv. Otroligt smidiga!
Ovan; Hatthylla provisoriskt monterad för att kontrollera passform.
Nedan; Problemet med vanlig tunnplåt är att den är ganska klen. Klen plåt brukar dessutom ge resonanser, vilket kan vara bra att förebygga. Rillor i plåten är ett enkelt knep för att styva upp den och på så sätt minska risken för resonanser. Tre rillor i bliden till höger gjorde att 1m låg aluminiumplåt (1mm) inte böjdes nämnvärt av sin egenvikt.
Nedan; Högra bilden visar andra ypperliga ändamål för Cleckosen… Injustering av panelen pågår, den har aldrig haft särskilt bra passform och nu är ett bra läge att åtgärda det. Högerbilden visar fortsatt provmontering av hatthyllan.
Ovan; Så här blir det alltså. Snart dags att montera den permanent.
Nedan; Panelen limmas och nitas mot plåten. Även ytan där ryggstödet var innan kommer täckas med plåt. Eftersom tanken sitter i bakluckan, måste detta utrymmet vara skiljt från kupén.
Nedan; Och så här blev resultatet! Lite färg på det så kommer det bli lagom anonymt.