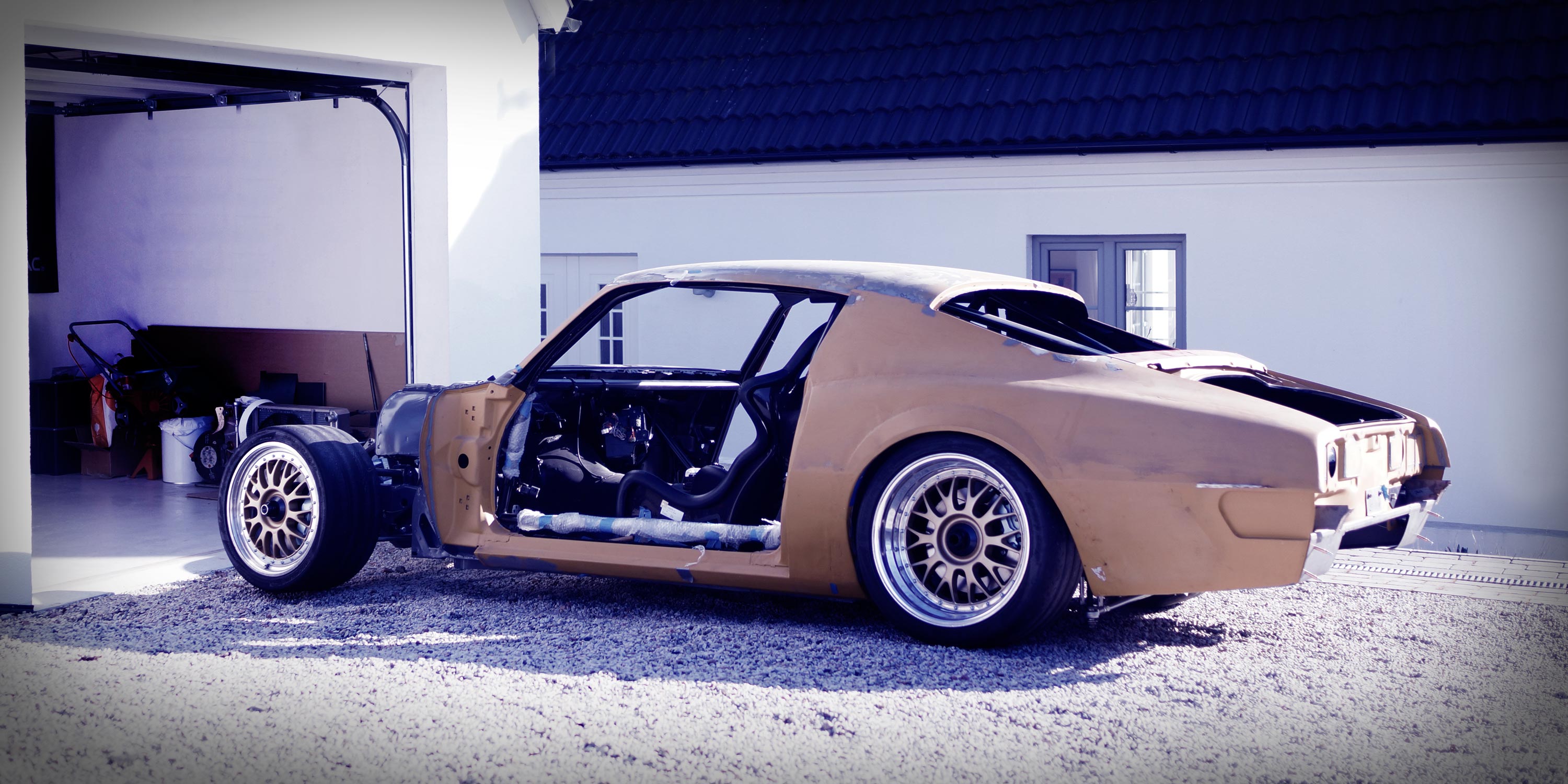
Kategori: The Project
Montering, bakvagn
Det börjar ta sig!
Nedre länkarmarna sitter på plats. Den övre fick avvakta och blev istället i trä. Samma med stötdämparna för att få bakvagnen i ride height. Generellt är det en nästan euforisk känsla att få börja skruva på delar på bilen. Bakaxeln behöver fixas några mindre saker på, därav att den fortfarande är senapsgul. Ett tränat öga skymtar dessutom att växellådan sitter på plats till vänster i bild. Det går bra nu!
Montering, länkarmar
Bakvagnen gjordes klar förra året. Därefter har den legat i bitar och vissa detaljer lämnades in för ytbehandling. Eftersom det var gängor, interna ytor med presspassning osv. var det enklare att gulkromatera detaljerna än att lackera dem. Baserat på samma resonemang ytbehandlades även vantstagen (i aluzink) eftersom de har nyckelgrepp för justering.
En rad andra saker har också kromaterats och förzinkats istället för lackering. Dels är det snyggt och väger lite, men fördelen är främst att det täcker bra och är okänsligt för stenskott.
Ovan vänster; Vantstag hamnar närmare bakvagnen än karossen. Karossen var i vägen för att tex ha den mitt på staget. Högra bilden visar en del av den överkurs som görs i samband med projektet – självklart får det ju tillverkas ett verktyg för att kunna spänna bussningarna. Ytbehandlat och märkt med rätt bilmärke, så klart!
Motorfästen del 2
När det gäller val av motorfästen, blev det helt enkelt vanliga bussningar. De har, till skillnad från många riktiga motorfästen, fördelen att vid tex brand i motorrummet gör det inget om plasten smälter. Eftersom det sitter genomgående skruv i hylsan. Motorpaketet kan skramla bäst det vill vid en avåkning/olycka, men det kommer aldrig släppa från infästningarna. I teorin i alla fall…
Ovan; Powerflexbussningar används som motorfästen. Henrik skar till några plåtar till mig och hylsan svarvades själv. Generellt kan det vara svårt att få till hundradelarna på invändiga mått, men i detta fall förenklades det genom att det ”råkade” finnas en 28mm brotsch liggandes. Den rostfria axeln som följde med bussningen kortades ca 10mm. Skruvhålet är bara 8mm, men skall tas upp för att passa M12 var det tänkt. Plåtarna på bilden är bara punktade samman. De ska såklart helsvetsas senare. Bussningarna är köpta på Demon Tweeks, artikelnummer; PFXPF99-102
Nedan; Andra röret mellan ram och drivlina sitter på plats. Stabilt, hade Dr Alban beskrivit det som.
Ovan; Och så här blir det. Tack vare att motorn sitter bakom framvagnsbalken, blir det ett helt annat utrymme för grenrören. Även dessa kommer behöva byggas eftersom motorn är sänkt… Suck. Det finns inga genvägar till den perfekta bilen!
Motorfästen
Med subframen hopsvetsad finns det egentligen ingenting att skylla på, utan det var bara att sätta igång direkt med att börja mäta in drivlinan inför byggnationen av motorfästen. Motor och växellåda hamnar ca 20cm längre bakåt än original, samt 2cm förskjutet åt passagerarsidan. Förskjutningen fick göras för att rädda utrymmet kring gaspedalen – annars hade alla pedaler fått flyttas åt vänster, vilket resulterat i att de inte suttit rätt i förhållande till ratten. För att undvika detta, flyttades som sagt motorpaketet ett par centimeter mot passagerarsidan. Med lite tur, kan det till och med kanske vara så att viktfördelningen höger-/vänstersida blir jättefin eftersom motorpaketet förhoppningsvis kompenserar för förarvikten. Med lite tur som sagt…
Ovan; Motorpaket på plats. 200mm längre bak, 20mm mot passageraren och ca 60mm lägre än original. Hade inte svänghjulet varit så stort, hade motor kunnat sänkas ytterligare ca 50mm utan att för den delen hänga ner under bilen… Frestande! Men jobbet med att konstruera ett nytt svänghjul, ny koppling, ny startmotorposition osv känns lite lågprioriterat i dagsläget. Fullt möjligt att det blir någon gång i framtiden.
Nedan; Henrik som skär plåt åt mig karvade ut ett par bitar till motorfästen blixtsnabbt utefter mina CAD-filer. Förutom motorfästet kan jag inte låta bli att glädjas åt CADen ibland. På den vänstra bilden syns infästningen till motorfästet i framvagnen, vilket till synes hamnar rakt under motorfästet. Delarna byggdes oberoende av varandra, utan att provpassas innan hålet borrades i framvagnen men tack vare CADen linjerar sakerna fint. Underbar känsla. Nördigt, men underbart.
Ovan; med hjälp av karossens referenspunkter, mättes ett koordinatsystem ut på golvet. Därefter måttades vevaxel och utgående axel på växellådan in 20mm offset från karossens mittlinje (mittlinje är den röda tråden, blått streck på silvertejpen är vevaxeln). När det var uppmätt, fixerades växellådan med hjälp av en temporär växellådsbalk.
Nedan; Motorbussning monterad och därefter kapades ett rör till. Ytterligare en förstärkning hamnar mellan bussning och rörstump på högra bilden.
Nedan; Tittar man på lutningen på motorfästena här, ser man tydligt att motorpaketet sitter något förskjutet.
Pallbock
Färg på underrede, nygjutet innertak och allt plåtjobb färdigt… Inte mycket användning för karossvaggan längre, utan istället är det dags att ställa karossen på pallbockar. Kanske inte alla som känner så när deras bil hamnar på pallbockar, men i detta fall är det ju ett stort framsteg som sagt. Ett steg närmare att stå på fyra hjul.
Ovan; inga konstigheter – lossa skruvarna som håller fast karossen, lyft karossen med hjälp av tvåpelarlyften…
Nedan; …och sänk ner den på lämpliga flyttdon för att kunna hasa tillbaka den till garagefållan.
Nedan; Det är som med triss – Plötsligt händer det!
Subframe påbörjad!
Att hålla på med den här typen av projekt kräver en hel del planering, både vad gäller logistik, få hem köpta komponenter i tid, samt fördela resurser på det som för stunden är bäst. En enkel lösning hade varit att köpa hem allt direkt, men risken finns alltid att man ändrar sig lite under projektets gång och plötsligt behövs det nya delar. Dessutom binder det kapital, och om projektet av någon anledning skulle läggas ner, är det onödigt att tex sitta på 100 000:- i delar som är svårsålda. Utan att avslöja för mycket, är det en liten garageflytt på gång under vintern, vilket skapar lite oreda i planen. Plötsligt måste vissa som inte var lika brådis med färdigställas snarast. Bland annat måste subframen vara tillräckligt färdig för att kunna provmontera drivlina och tillverka motorfästen till denna. På bilderna nedan finns alltså fas1 av subframen. Utöver det som syns på bilderna, tillkommer övre länkarmsinfästningar, krängningshämmarinfästningar, burrör, vipparmsinfästningar och då såklart motorfästen. Dvs nu blir det motorfästen, resten kommer i framtiden.
Av besiktningstekniska skäl, återanvänds de längsgående rambenen (för mycket saker får inte ändras)… Egentligen skulle bryggan också användas, men den visade sig tyvärr vara för rostig kring infästningarna och arbetet skulle bli för stort för att rädda den. Därför föddes idén om en ny framvagnsbalk, vilket i sin tur tillät tillbakaflyttad motor, lägre vikt osv.
Ovan; Precisionen blir riktigt bra, trots den något primitiva fixturen. En fullskaleritning skrevs ut för att bygga framvagnsbryggan av. Därefter positionerades denna med hjälp av utmätning av centrum mellan infästningarna i karossen. Precisionen blev bra som sagt, uppskattningsvis mindre än +-1mm. Gissningsvis bättre, eller i klass med de stora biltillverkarna.
Nedan; Vänster; Vaggan ligger högre än de längsgående benen. Detta är pga de längsgående benen egentligen ligger för lågt, trots att de sitter så högt upp i karossen som möjligt. De får helt enkelt betraktas som skrapskydd för resten av underredet.
Ovan; Hålen närmast i bilden ska såklart läggas igen också. I övrigt ser den ju ganska stöddig ut, subframen. Lite mer triangulerat än tidigare och betydligt styvare.
Vaggan till framvagnen klar
I somras påbörjades framvagnsvaggan. Den har därefter fått ligga till sig lite pga andra prioriteringar i projektet, men nu börjar det bli dags för att färdigställa framvagnen också.
Den har på bilderna kompletterats med bakåtgående profiler där bla. bakre infästningen av nedre länkarmen hamnar, samt även motorfästen.
Ovan; Total vikt blev 11,0Kg, jämfört med originalbryggans 17,5kg som den ersätter. En rätt trevlig viktbesparing med andra ord, även om den råkar vara lågt placerad.
Nedan; Det som skiljer köpta komponenter från hemtillverkade är att man har möjlighet till längre arbetstid på de hemtillverkade. Mycket svets blir det…
Ovan; Alla infästningar görs i hylsor, som svetsas i båda profilerna. På detta sätt fördelas lasterna fint över ett större område. Bilden visar ett par hylsor till motorfästen. Även om de ”bara” ska svetsas, måste såklart kanterna brytas – något annat vore slarv.
Nedan; Färdigt resultat att svetsa på de längsgående ramdelarna. Blir bra det här…
Innertak pt.II
Efter att taket fått torka kom den stora dagen då det skulle visa sig om släppmedlet fungerade eller inte. Är nu tanken att det ska vara löstagbart, är det ju trevligt om det är så också…
Ovan; Ser rätt bra ut faktiskt. Blir snygga former på taket, och buren smälter bra in mot taklinjen längs rutans ovankant, samt A-stolpen.
Nedan; Jodå! Det släpper ju fint, även om lite extra våld krävdes på vissa platser. Det kom en del frågor på vilket material som användes för att skapa övergångar mellan de olika delarna. Sibatol heter det och finns i olika densiteter, allt från fräsbara material till modellen som påminner om det där gröna som man ställer växter i. Detta var åt det hållet, men lite hållbarare. Gick dock fint att skulptera med kniv. Det hade gått lika bra med frigolit, men i detta fall råkade jag ha lite liggandes.
Nedan; Och här är alltså resultatet. Två bitar innertak som kommer göra mycket för känslan. Nu läggs det på hyllan tills att det är dags att ta itu med inredningen.
Innertak
Bilen ska trots allt bli gatreggad och nakna plåtinredningar hör endast hemma i bilar som alltid framförs med hjälm och öronproppar. Entusiaster är alltid olika hardcore – i just mitt specifika fall skippas asfaltsmattor för viktens skull men däremot täcks all plåt med inredning. Det blir inte många extra kilon…
Genom att vara lite förutseende, kunde en stomme till innertak gjutas redan innan karossen plockades ur vaggan. Det är svårt att gjuta saker upp och ner, så detta var nog enda sättet att kunna göra det. För att öka den subtila utstrålningen, skall såklart buren döljas så gott det går. Det finns två fördelar med detta – det sticker inte för mycket i bilprovningens ögon, samt den kan stoppas och bli riktigt mjuk och skön.
FIA-godkänd burisolering införskaffades. Den är stenhård, sannolikt hade man kunnat använda isoleringen som brännbollsträ. Det handlar dock om att sprida extremt höga laster på så stor yta som möjligt och det är helt enkelt omöjligt att simulera med ett knytnävsslag (som sannolikt resulterar i blåmärken…).
Ovan; Fyra nyanser av… svart! Inte helt lätt att urskilja, men på de längsgående rören sitter det burisolering. En avbärare skars också till.
Nedan; När isolering, avbärare samt några temporära bitar för att ge snygga övergångar mellan de olika ytorna skurits till, täcktes allt med tejp. Blå sådan.
Ovan; Och när tejpen var klar, tejpades den över med alutejp. Ovanpå alutejpen penslades släppmedel.
Nedan; Två lager 300-gram väv på det och därefter dags att börja kladda med polyestern. Skruvtvingen sitter där pga plåten som utgör rund-och-snygg-profil mot rutramen inte hade några vettiga skruvinfästningar i taket.
Därefter var det dags att fly garaget med tanke på stanken…
Montering av stolar
Innan kupén lackerades, provmonterades stolarna för att se var håltagningen skulle göras.
Ovan; stolen står utplacerad på ungefärlig plats.
Nedan; Infästningarna för stolen har fått förstärkningar från undersidan, enligt rekommendationer från SBFs tekniska regler. Även bältesinfästningen (högra bilden) har FIA-godkända plattor på baksidan.
Ovan; Devil is in the details säger de som vet… Man kan så klart fylla på med brickor till stolsunderredet går fritt. Men ska man göra det riktigt, svarvar man såklart en distans med korrekta dimensioner när väl höjden är spikad. I plast så klart – viktbesparing på ca 35 gram jämfört med stålbrickorna!
Nya stolar!
Nu när det blir så mycket nytt på bilen, kändes det lite tråkigt att sätta tillbaka MOMO-sportstolarna som satt där innan. Det var visserligen inget fel på dem och de var väldigt bekväma också. Dock fanns det helt enkelt ett behov av förnyelse.
Det finns en rad stolar på marknaden, men är man 2 meter lång finns det bara ett litet fåtal stolar kvar som passar. Alla Sabelt gick bort, alla (med vettig budget) Cobra och i princip alla Sparco. Sparco Evo+ funkar bra längmässigt men problemet är att den är gjord för folk som väger 140 kg, inte 85…
Det finns dock andra företag än de stora och så länge stolarna är FIA-godkända innebär det, i mina ögon, på en kvalitetsstämel som gör att man vågar handla oavsett vad det råkar stå för tillverkarnamn på stolen.
Därför köptes det två stolar från Bimarco då jag sitter väldigt bra i dem. De har en av de högsta stolsryggarna på marknaden, är lätta och går att få med olika färger. I mitt fall blev det att slanta upp extra för att få äkta skinn på stolarna istället för det lite vanligare nomex-tyget (eller vad det nu är) som alla stolar har. Skinnet gör att det ser lite mer tidstypiskt ut, även om man ser direkt att det inte är tal om några originalstolar. Dessutom luktar det ju gott när man sätter sig i kupén.
Förarstolen hamnar på justerbart underrede, medans passagerarstolen blir fast monterad. För att hålla koll på viktfördelning, monteras den ganska långt bak, samt framför allt så nära golvet som möjligt.
Och en liten krock som avslutning… Tänk på säkerheten.
Framvagnsupphängning
Man kan såklart inte bygga ramen till framvagnen utan att ha gjort klart hjulupphängningarna. Efter att geometrin spikades ritades spindel, länkarmar och andra tillhörande komponenter. När dessa var färdiga, var det enkelt att se var infästningspunkterna skulle hamna på ramen.
Några saker i konstruktionen förtjänar ett extra omnämnande;
Push-rods: Då nedre länkarm är 530mm lång och en stötdämpare skall placeras så nära spindeln som möjligt var det svårt att montera coil overn utan att vinkeln skulle bli väldigt flack (vilket gör att fjäderkonstanten minskar med ökat fjädringsväg). För att komma tillrätta med detta, och ha möjligheten till en linjär fjädringsrörelse över hela hjulrörelsen (coil over och hjul rör sig 1:1) beslutades det om att sätta coil overn via någon form av länkage.
Många försök med att få plats med ett pull-rod system gjordes då detta kan göras lättare än ett push-rod länkage. I båda fallen satt det en motor i vägen, vilket gjorde att de fick monteras i längsled istället för tvärs över framvagnen. Möjliga placeringar blev då ovanpå (bilden nedan) samt under rambenet. Pull-rod hade placerat coil overn under rambenet. Tyvärr föll det på att coil overn inkräktade på nedre länkarmens utrymme vid fjädring, samt att den helt enkelt hamnade för nära grenröret. Synd eftersom det hade blivit en väldigt tilltalande lösning.
Istället valdes push-rods. Resultatet skäms inte för sig då det, efter mycket trixande och justerande, som sagt blev linjärt förhållande mellan hjulrörelse och dämpare.
Styrväxel: originalets styrsnäcka är ett minne blott. Istället blir det kuggstång! För att undvika att bygga in överstyrning skapat av flex i konstruktionen gäller det att ha koll på hur spindeln belastas. Genom att placera styrväxeln i den nedre kvadranten framför hjulaxeln, eller den övre kvadranten bakom hjulaxeln skapas gynnsamma styregenskaper även under belastning. Pga motorn fanns det bara en enda naturlig placering som lyckligtvis sammanföll med tesen ovan – nämligen framför och i höjd med nedre länkarmen. Infästningen blir justerbar för att kunna finjustera bumpsteer och ackerman senare.
Krängningshämmare: Egentligen inte så mycket och skriva kring detta, mer än att det blir kniv-baserad krängningshämmare för att enkelt kunna finjustera chassiet. Kniven tillverkas specifikt efter chassiet, dvs fjäderkonstanterna som max och min är anpassade för att få ett stort justerspann.
Ovan; Det var svårt att hitta vyer där konstruktionen framgår klart och tydligt, men på ovanstående bild och vänstra nedre kan man i alla fall ana styrväxelplacering. På bilden skymtar även huvudbromscylindrarna och bromsservot. Mer om detta senare…
Ovan; Pushrods och längsmonterade dämpare användes för att skapa ett 1:1 rörelseförhållande (linjärt över hela rörelsen) mellan hjul och kolvstång i dämparen. Det ser ju enkelt ut på bilden, men det var väldigt mycket pusslande och passande innan det gick att få till. Det är rätt ont om plats, och den behövde planeras väl för att dämparen inte skulle krocka med tex övre länkarmen vid infjädring.
Nedan; En bild på bakvagnen på Porsche GT1 – även om den inte fungerat som inspiration för projektet kan man ju konstatera att placeringen av komponenterna (krängningshämmare, push-rods och dämpare är ungefär samma. Högra bilden visar nedre kvadranten framför hjulaxeln (grön), respektive övre kvadranten bakom hjulaxeln (blå) vilka lämpar sig bra för styrväxelplacering då belastningarna på spindeln skapar understyrning istället för överstyrning vid flex. Pga bojsänket till motor, blev den naturliga placeringen i den gröna fyrkanten. Motorn är visserligen tillbakaflyttad, men inte tillräckligt för att remhjul ska sitta bakom bakaxen. Något som gjorde att styrväxeln var tvungen att placeras under motorn, i höjd med nedre länkarm.
Nedan; Ytterligare en bild på hjulupphängningen utan ramen. Det är rätt många komponenter… jobbigt läge när man inser att nästan inget på bilden går att köpa utan allt måste tillverkas… Aja, gick bakvagnen att tillverka så ska nog det här också vara görbart.
Nedan; Gamla F1 bilar är alltid intressanta att studera, främst pga de tekniska lösningarna idag kan klassas som möjliga att härma för gemene man. Nedan finns några exempel på pull-rod länkage. Försök gjordes att göra liknande lösning på Pontiacens framvagn, men tyvärr erhölls aldrig någon riktigt bra fjädringskarakteristik.
Och kupén…
Så fort färgen på underredet hade torkat, var det dags för kupén. Då buren skulle lackas samtidigt, var detta lite svårare än att måla ett förhållandevis slätt underrede. Då kupén dessutom skulle lackas svart, vilket gör att ljuset försvinner ju mer ytor som lackas, visade det sig i princip… skitsvårt att lacka. Hade jag orkat, hade buren lackats svart och resten av plåten i samma grå som golvet. Men egentligen kvittar det – allt skall ju täckas med inredning ändå…
Ovan; Bagaget målades också svart. Hålet för tanken visade sig nödvändigt för att kunna komma åt under hatthyllan.
Nedan; De sista bilderna på en omålad kupé
Nedan; Några bilder på genomförandet finns inte, men det slutade med att det fick göras två gånger pga att det kom för tunt lager färg på buren. Andra gången blev resultatet dock bra.
Ovan; Svart är svart. Svart är ju helt omöjligt att ta bilder på! Det blir till att börja plåta med stativ och långa slutartider om man ska kunna urskilja sakerna som monteras tillbaka… Den vänstra bilden är belyst av torklampan som ger ett rätt gulaktigt ljus, därav den lite lustiga färgen.
Som sagt, en stor milstolpe är passerad! Otroligt skön känsla att veta att saker som monteras på underrede och i kupé sker permanent.
Färg på underredet… Episkt!
Bodyn fick torka en vecka, och därefter var det dags att ÄNTLIGEN lägga översta skiktet. En händelse som knappast passerar obemärkt i projektets historia med tanke på att det efter detta går att börja slutmontera vissa komponenter!
Egentligen var det ganska tidigt klart vilken kulör underredet skulle få. Den exakta nyansen behövde visserligen funderas lite över, men kort sagt är svart alldeles för mörkt att ha. Vitt är ju visserligen rejsigt, men bara de första 15 minuterna efter att bilen tagits i bruk. Därefter upplevs den som skabbig. En mörkgrå nyans är som gjord för ett underrede – damm och smuts får ungefär samma nyans och det är enkelt att hålla rent tack vare den släta ytan.
När det gäller typen av färg valdes, efter en del diskuterande med lackerare och färgleverantörer, en polyurethanfärg istället för traditionell billack eller epoxifärg. Polyurethanen blir hårdare och lämpar sig bra för den här typen av applikationer. Lastbilschassien, lantbruksmaskiner osv brukar lackeras med denna typ av färg. Med andra ord duger den nog för det Pontiacen kommer utsättas för… Färgen hette Temadur 20 och köptes på Färgprodukter i Malmö.
Ovan; För att snabba på torkprocessen och härda ut färgen direkt, torkades den med infrarött ljus.
Nedan; Resultatet pratar för sig självt. Så här fint har nog aldrig underredet varit, någonsin!
Ovan; Färgen flöt ut bra och var lätt att lägga utan att få rinningar. Dvs resultatet blev bra, även om jag aldrig hållit i en spruta innan.
Skydd av hjulhusen
Med karosskitt i alla skarvar lades ett tunt lager Body i hjulhusen och bakom bakhjulen. Det tog emot i hjärtat att spruta på denna förhatliga gummimassa (den som skrapat av sådan vet vilket skit det är att bli av med). Hagmans Body i detta fall – lika bra att hålla sig till samma märke så vet man att komponenterna är kompatibla och slipper råka ut för otrevliga överraskningar…
Eftersom det ändå skulle målas över valdes vit kulör. Enkelt och se att det täckt överallt…
Ovan; Den skarpsynte ser maskeringstejpen för stötdämparhålen. Just denna ytan kändes inte så lönt att lägga body på då stötdämparna monteras där.